Are you struggling with finding the best material for your custom battery needs in new energy vehicle sheet metal fabrication? The automotive industry is evolving rapidly, and the right choice of materials can make a significant difference in performance and reliability. In this post, let's explore why T2 copper has become the go-to material for custom batteries in electric vehicles.
T2 copper stands out due to its high electrical conductivity, durability, and malleability, making it ideal for custom battery fabrication. It ensures efficient power distribution, withstands harsh conditions, and can be easily shaped to meet specific design requirements. These properties make it a preferred choice for creating battery enclosures, connectors, and conductive busbars.
To fully appreciate why T2 copper is a leading choice for new energy vehicles, it's crucial to understand the unique properties that set it apart. This metal's combination of high conductivity, resistance to corrosion, and ease of fabrication has made it a staple in the automotive industry. As electric vehicles gain popularity, custom battery fabrication requires materials that can handle the demands of high-current applications while remaining cost-effective and durable. Let's delve deeper into the reasons behind T2 copper's rise to prominence in this context.

What Makes T2 Copper Ideal for Custom Batteries?
The demand for new energy vehicles has soared, leading to increased scrutiny over the materials used in their production. Why is T2 copper the preferred material for custom batteries in electric vehicles?
High Electrical Conductivity
The primary reason T2 copper is favored for custom batteries is its exceptional electrical conductivity. This characteristic ensures efficient power distribution throughout the vehicle's battery system, reducing energy loss and enhancing overall performance. For electric vehicles, which rely heavily on efficient energy transfer, T2 copper's conductivity is a game-changer.
Durability and Corrosion Resistance
Another crucial factor in favor of T2 copper is its durability and resistance to corrosion. Custom battery components need to withstand harsh environmental conditions, including exposure to moisture and temperature fluctuations. T2 copper's natural resistance to corrosion ensures longevity, reducing the need for frequent maintenance or replacement of parts.
Malleability and Custom Fabrication
T2 copper's malleability makes it an ideal choice for custom fabrication. The metal can be easily shaped into various forms, allowing for intricate designs and custom solutions in battery enclosures, connectors, and other critical components. This flexibility is invaluable in the automotive industry, where innovation drives demand for unique and efficient battery systems.
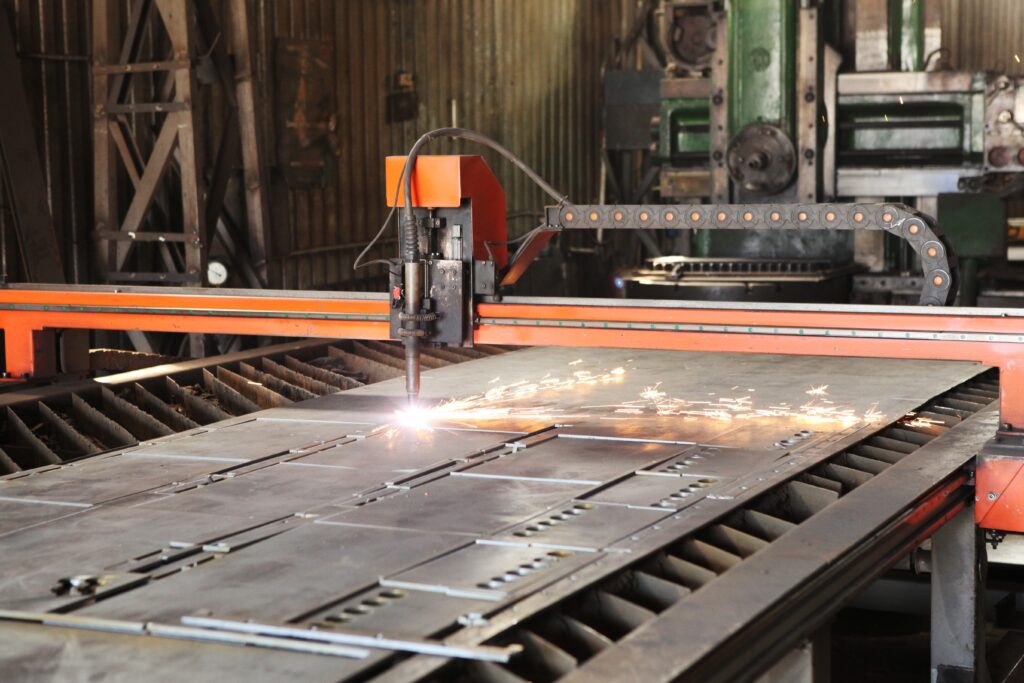
What Are the Key Applications of T2 Copper in New Energy Vehicles?
Given its unique properties, how is T2 copper used in the custom fabrication of batteries for electric vehicles? Let's explore the key applications where T2 copper excels.
Custom Battery Enclosures
Battery enclosures made from T2 copper benefit from the metal's high conductivity and durability. These enclosures protect the internal components while ensuring efficient energy transfer throughout the battery system. The custom fabrication potential of T2 copper allows for tailored enclosures that meet specific design and performance requirements.
Battery Connectors and Terminals
The malleability of T2 copper allows for the creation of intricate connectors and terminals within the battery system. These components play a vital role in ensuring secure and efficient connections between battery cells and other electrical parts. With T2 copper, custom connectors can be designed to meet the unique demands of electric vehicles.
Conductive Busbars
Conductive busbars are another key application of T2 copper in new energy vehicles. These busbars are used in high-current applications, ensuring stable energy distribution across the battery system. T2 copper's high conductivity and durability make it a reliable choice for this critical component.
What Are the Benefits of Using T2 Copper in Custom Battery Fabrication?
The benefits of using T2 copper in custom battery fabrication extend beyond its high conductivity and durability. Let's explore some additional advantages that make this material a top choice for electric vehicle manufacturers.
Enhanced Battery Performance
T2 copper's exceptional conductivity contributes to enhanced battery performance. Electric vehicles require efficient energy transfer, and T2 copper ensures minimal energy loss, resulting in better overall performance and longer battery life.
Cost-Effective Production
Despite its high quality, T2 copper offers cost-effective solutions for custom battery fabrication. The metal's malleability reduces manufacturing complexities, allowing for streamlined production processes and lower costs. This cost-effectiveness is a significant advantage for electric vehicle manufacturers looking to optimize their production budgets.
Reliable and Durable Construction
The durability and corrosion resistance of T2 copper ensure that custom battery components can withstand the test of time. This reliability translates into reduced maintenance costs and fewer replacements, providing long-term value for electric vehicle owners.
Why is thermal management critical in custom batteries for electric vehicles?
Thermal management is essential in electric vehicle batteries to prevent overheating, which can lead to reduced performance, safety risks, and shortened battery life. T2 copper's high thermal conductivity allows for efficient heat dissipation, keeping batteries within safe temperature ranges. This thermal management ensures the longevity and reliability of custom batteries, providing electric vehicle manufacturers with a robust solution to the common challenges associated with battery heating.
How does T2 copper's compatibility with other materials benefit custom battery fabrication?
T2 copper's compatibility with commonly used materials like aluminum and steel offers seamless integration into electric vehicle designs. This versatility allows manufacturers to incorporate copper components into various assemblies without extensive redesign or retooling. It also simplifies the production process, as the copper can be easily integrated with other materials, contributing to efficient and cost-effective custom battery fabrication.
What is the environmental impact of using T2 copper in custom batteries for electric vehicles?
Using T2 copper in custom batteries for electric vehicles can positively impact the environment. T2 copper is recyclable, meaning that once a battery has reached the end of its life, the copper components can be reclaimed and reused. This recyclability reduces waste and contributes to sustainability efforts in the automotive industry, aligning with the growing emphasis on eco-friendly practices and resource conservation.
How does T2 copper comply with industry standards in electric vehicle battery fabrication?
T2 copper meets various industry standards for electrical and thermal conductivity, ensuring compliance with automotive regulations. Compliance is essential for electric vehicle manufacturers, as it allows them to market their products globally without legal or safety issues. By using T2 copper, manufacturers can be confident that their custom battery components adhere to the necessary standards, providing a reliable and safe solution for electric vehicle battery fabrication.
What role does T2 copper play in enhancing resilience to mechanical stress in custom batteries?
Custom batteries in electric vehicles often face mechanical stress due to vibrations, movement, and other physical impacts. T2 copper's durability and flexibility help components withstand these stresses without damage or failure. This resilience is crucial for maintaining battery integrity and performance over time, reducing maintenance costs and improving the overall lifespan of custom battery systems in electric vehicles.
Conclusion: Is T2 Copper the Best Choice for Your Custom Battery Needs?
T2 copper is the preferred choice for custom batteries in new energy vehicles due to its exceptional conductivity, durability, and malleability. Its unique properties support efficient power distribution and cost-effective production, ensuring reliable performance in electric vehicles. T2 copper also excels in thermal management, compatibility with other materials, and resilience to mechanical stress. Its environmental impact, owing to its recyclability, adds to its appeal. If you're in the market for custom batteries, T2 copper's versatility and proven track record make it the ideal material for your needs.