Choosing the right material for sheet metal fabrication can be overwhelming. From aluminum to stainless steel, the options are endless. The wrong choice could mean costly rework, delays, or worse, project failure.
You don’t want to waste time or money. It’s frustrating when your sheet metal parts warp, rust, or fail under pressure. Trust me, I’ve seen it all in my 30 years in the industry.
Let's simplify things. In this guide, I’ll break down the most common materials used in sheet metal fabrication, their properties, and the best applications. Whether you’re working on aerospace, consumer electronics, or construction projects, I’ve got you covered. Let's dive in!
The best material for your sheet metal project depends on the application, environmental factors, and your budget. Aluminum alloys, stainless steel, cold-rolled steel, and specialized materials like Inconel or Beryllium Copper offer a range of properties tailored to specific needs. Choosing the right one could save you headaches and money in the long run.
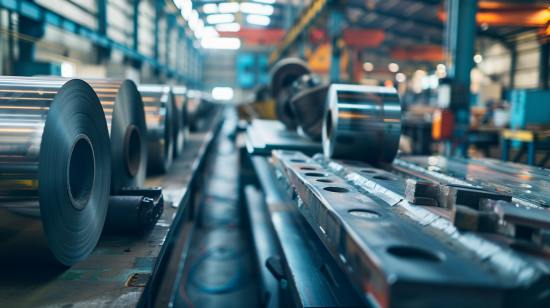
Why Is Choosing the Right Sheet Metal Material So Important?
You can’t build an airplane from any metal. I’ve seen clients spend thousands of dollars on projects that failed because they picked the wrong material. Picture a marine part corroding a few months after installation or an aerospace part failing in-flight. Not good, right? Don’t worry. By the time you finish this post, you’ll know exactly which material you need for your next project.
Which Aluminum Alloy Should I Choose?
Aluminum is one of the most versatile materials in sheet metal fabrication. Whether you’re working on a lightweight aerospace structure or an automotive component, aluminum has you covered.
- 5052 Aluminum: If corrosion resistance and flexibility are what you need, 5052 Aluminum is your go-to. It’s perfect for marine applications, fuel tanks, and household appliances. This alloy has excellent resistance to saltwater and is highly formable, making it great for parts that need to be bent or shaped.
- 6061 Aluminum: Need something a bit stronger? 6061 Aluminum is a workhorse alloy. It's used in everything from bike frames to airplane wings. It offers a solid mix of strength, corrosion resistance, and machinability. Whether you’re working on an automotive project or a structural component, 6061 delivers.
- 7075 Aluminum: Now, if you’re looking for aerospace-grade strength, 7075 Aluminum is the champ. This high-strength alloy is used in aerospace and military applications due to its superior fatigue resistance. However, it’s a bit pricier than other aluminum alloys. So, unless you really need that strength, 6061 might be more budget-friendly. But if you do, 7075 is the way to go.
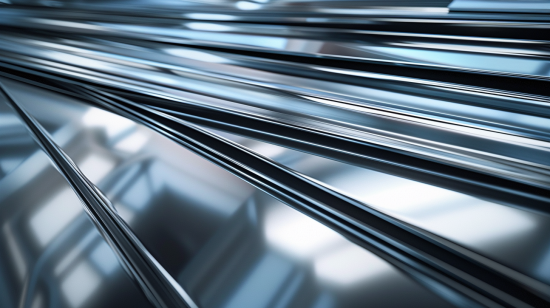
Should I Use With Stainless Steel?
Ah, stainless steel—the superhero of corrosion resistance. But did you know there are different types of stainless steel for different jobs? Let's break them down.
- 304 Stainless Steel: This is the most common type of stainless steel, and for good reason. It’s durable, corrosion-resistant, and relatively easy to work with. If you’re in the food processing, medical, or architectural industries, 304 Stainless Steel is likely your best option.
- 316 Stainless Steel: For projects exposed to chlorides, like marine environments, 316 Stainless Steel is what you need. It offers better corrosion resistance than 304 and is often used in surgical instruments, chemical processing equipment, and marine applications.
- 430 Stainless Steel: Need something cheaper but still corrosion-resistant? 430 Stainless Steel is magnetic and has decent corrosion resistance. It’s commonly used in automotive trim, dishwashers, and other appliances where extreme corrosion resistance isn’t as critical.
When Should I Use Cold-Rolled Steel?
Cold-Rolled Steel (CRS) is great for projects that require precision and a smooth finish. But let me warn you, it doesn’t have the same corrosion resistance as stainless steel.
- 1008/1010 Cold-Rolled Steel: Need something easy to shape and weld? 1008/1010 CRS offers good formability and is often used in automotive parts, home appliances, and furniture. It’s cheap, strong, and versatile, but don’t use it for outdoor projects unless it’s coated.
- SPCC Cold-Rolled Steel: If you’re working on electronics or office equipment, SPCC CRS is a solid choice. It offers a smooth finish, which makes it perfect for consumer electronics casings.
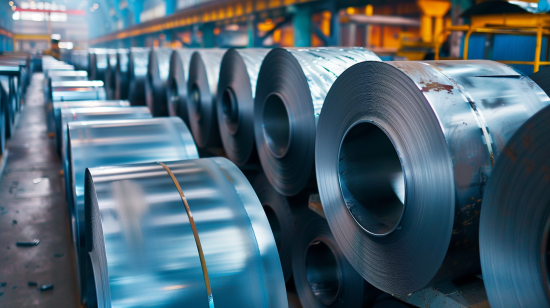
What About Galvanized and Galvanneal Steel?
If your project needs corrosion resistance, but you’re not quite ready to invest in stainless steel, Galvanized or Galvanneal Steel might be the middle ground you're looking for.
- G90 Galvanized Steel: With its thick zinc coating, G90 Galvanized Steel offers excellent protection against rust and corrosion. It’s used in roofing, fencing, and outdoor structures. I’ve seen this stuff hold up for decades.
- A40/A60 Galvanneal Steel: Need something that’s easy to paint? Galvanneal Steel has a zinc-iron coating that provides a better surface for painting. It’s often used in the automotive industry for body panels and in home appliances where aesthetics matter just as much as durability.
What Makes Copper and Brass So Special?
Copper and Brass might not be the first materials that come to mind for sheet metal fabrication, but they’ve got some fantastic properties.
- C110 Copper: For electrical applications, C110 Copper is unbeatable. It has excellent conductivity and is used in electrical wiring, heat exchangers, and plumbing. If you need a material that conducts electricity like a champ, this is it.
- C260 Brass: Want something that’s both strong and good-looking? C260 Brass (Cartridge Brass) has excellent formability and is often used in decorative hardware, plumbing fixtures, and ammunition casings. It combines functionality with aesthetics.
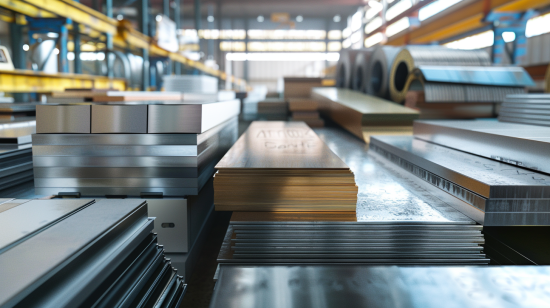
Is Zinc Just for Coating?
We often think of zinc as just a coating for steel, but it deserves more credit.
- Hot-Dip Galvanized Zinc: This is your classic zinc coating, applied to steel by dipping it in molten zinc. It’s a cost-effective way to protect steel from corrosion in outdoor applications like construction, roofing, and fencing. Think of it as armor for your steel components.
- Zinc-Aluminum Coating (Galvalume): This one’s a mix of zinc and aluminum, offering even better corrosion resistance and heat reflectivity. It’s popular in roofing and siding, especially in climates with high heat exposure.
How Does Nickel Silver Fit Into My Project?
Nickel Silver (German Silver) might sound fancy, and it is. But it's also incredibly useful in certain applications.
- Nickel Silver 752: This alloy is strong and has excellent corrosion resistance, making it perfect for decorative hardware and musical instruments. And let’s be honest—it looks pretty sharp too. It’s also commonly used in cutlery and jewelry, where aesthetics are key.

When Should I Consider Magnesium or Inconel?
When weight is a concern, Magnesium might be your best friend.
- AZ31B Magnesium Alloy: It’s one of the lightest structural metals, making it ideal for aerospace, automotive racing, and electronics. Plus, it’s easier to machine than you might think.
For extreme environments, Inconel is the way to go.
- Inconel 625: If you’re working in aerospace or chemical processing, Inconel 625 can handle the heat. It’s corrosion-resistant and maintains its strength at high temperatures, making it perfect for gas turbines and exhaust systems.
How Do I Choose the Right Material for My Project?
That depends on what your project needs. Is it going to be outside? Does it need to be light? Are you trying to save money? If you’re not sure, don’t worry. I’ve been doing this for 30 years, and I’m still learning new things every day. But I can tell you one thing for sure: the right material makes all the difference.
If you need something that’s strong and won’t rust, stainless steel or galvanized steel could be the answer. If you need something for electrical purposes or for its looks, copper and brass are great. And if you need something that’s light and strong, aluminum and magnesium might be right for you.
Conclusion
Choosing the right material is the foundation of a successful project. Whether it's aluminum, stainless steel, or a specialized alloy like Inconel, each material has its place in the world of sheet metal fabrication. Need help making a decision? I’ve got 30 years of experience and I’m here to guide you every step of the way. After all, a well-informed choice today can save you a lot of trouble tomorrow.