Sheet metal bending is a big deal in manufacturing. It’s how we make everything from car panels to computer casings. But it’s also something that can be a little intimidating. You might work in automotive, aerospace, electronics, or another industry. Regardless, understanding sheet metal bending could help you a lot in your business.
Sheet metal bending is when you apply force to a piece of metal to create a bend with a specific radius. You do this using a press brake and it’s how you make metal into the shapes you need for whatever you’re working on.
Let’s talk more about sheet metal bending. We’ll define it, talk about why it’s important, how it works, the benefits, and give you some real-world examples. If you understand these things, you can make your business more efficient and make better decisions on your sheet metal projects.
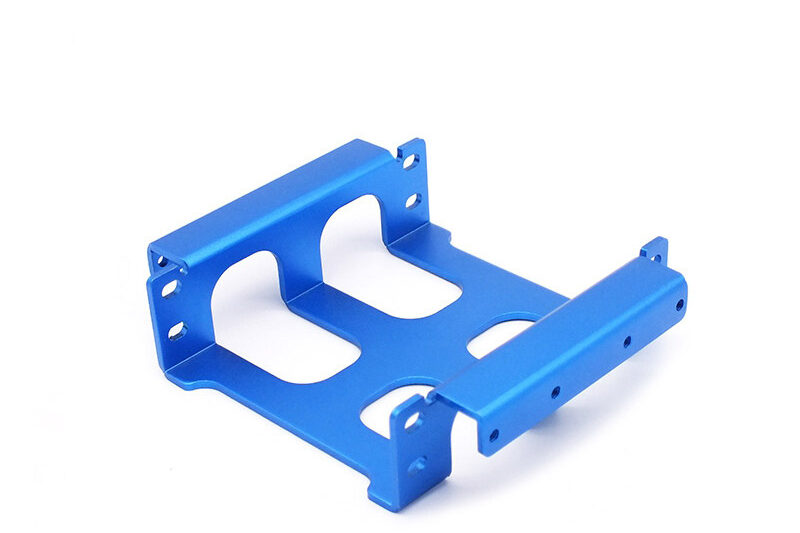
What Is Sheet Metal Bending?
Sheet metal bending is the process of forming metal into different shapes by applying force to deform the metal. This is done by various methods such as V-bending, U-bending, rotary bending, and roll bending. The most common method is using a press brake machine, which can be mechanical, hydraulic, or CNC controlled. The thickness of the sheet metal can vary from 0.127 mm to 6 mm.
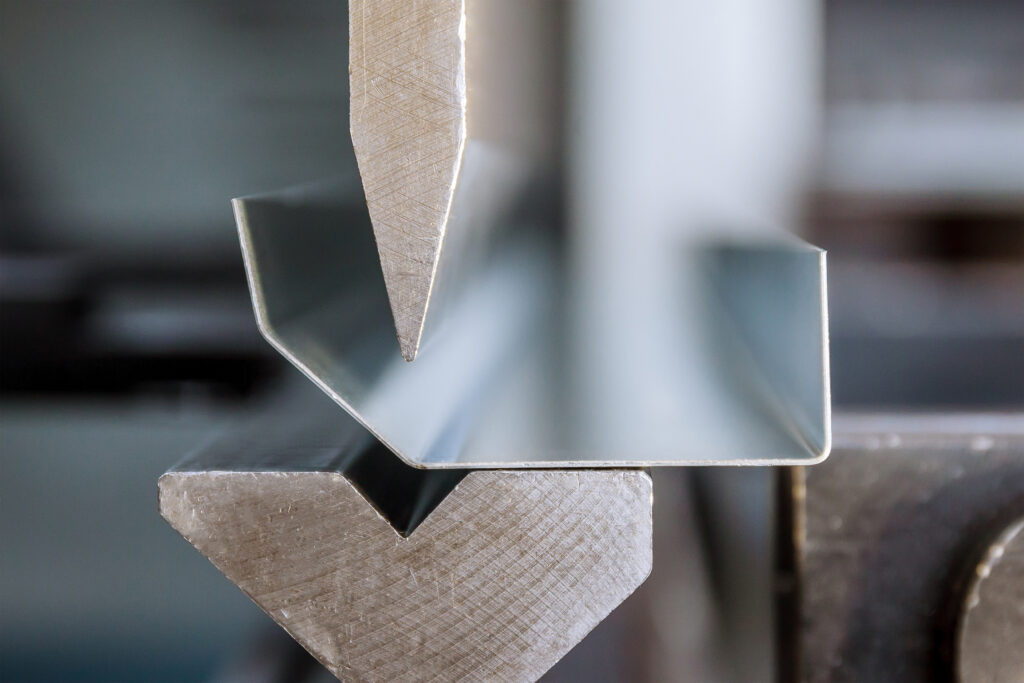
Purpose of Sheet Metal Bending
The main reason for sheet metal bending is to create features in a piece of metal for a variety of applications. This allows manufacturers to quickly and easily create body panels, reinforcement struts, brackets, and other parts. It’s especially useful for low production volumes and for products that require very thin metals where casting wouldn’t work. The automotive, aerospace, and consumer electronics industries use this process to create high-quality, functioning parts.
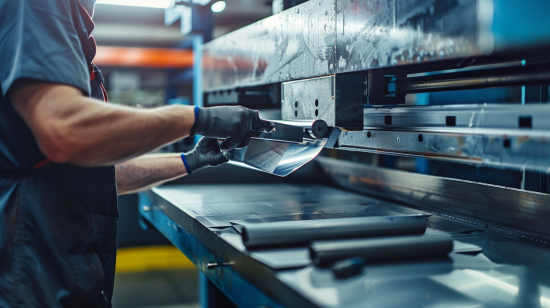
How It Works
Basic Principles of the Bending Process
- Force Application: A force is applied to a sheet of metal to bend it into the desired shape.
- Elastic and Plastic Deformation: Initially, the metal undergoes elastic deformation, where it bends but can return to its original shape. With more force, plastic deformation occurs, permanently bending the metal.
Common Bending Techniques
- V-bending: The metal is bent into a V-shape using a V-die.
- U-bending: Similar to V-bending but forms a U-shape.
- Rotary Bending: Uses a rotating die to bend the metal.
- Roll Bending: Passes the metal through rollers to create large, gentle bends.
Equipment Used
- Press Brakes: Mechanical, hydraulic, and CNC press brakes apply precise force to bend the metal.
- Roll Benders: Use rollers to bend the metal into curves or cylindrical shapes.
- CNC Bending Machines: Computer-controlled machines that accurately and automatically bend metal.
Factors That Impact Bending
• Material Thickness: Thicker materials require more force and have a larger bend radius.
• Bend Radius: The bend radius should be equal to or greater than the material thickness.
• Metal Grain Direction: Bending across the grain can help prevent cracking.
• Springback: Metal has a tendency to return to its original shape after bending, which must be accounted for.
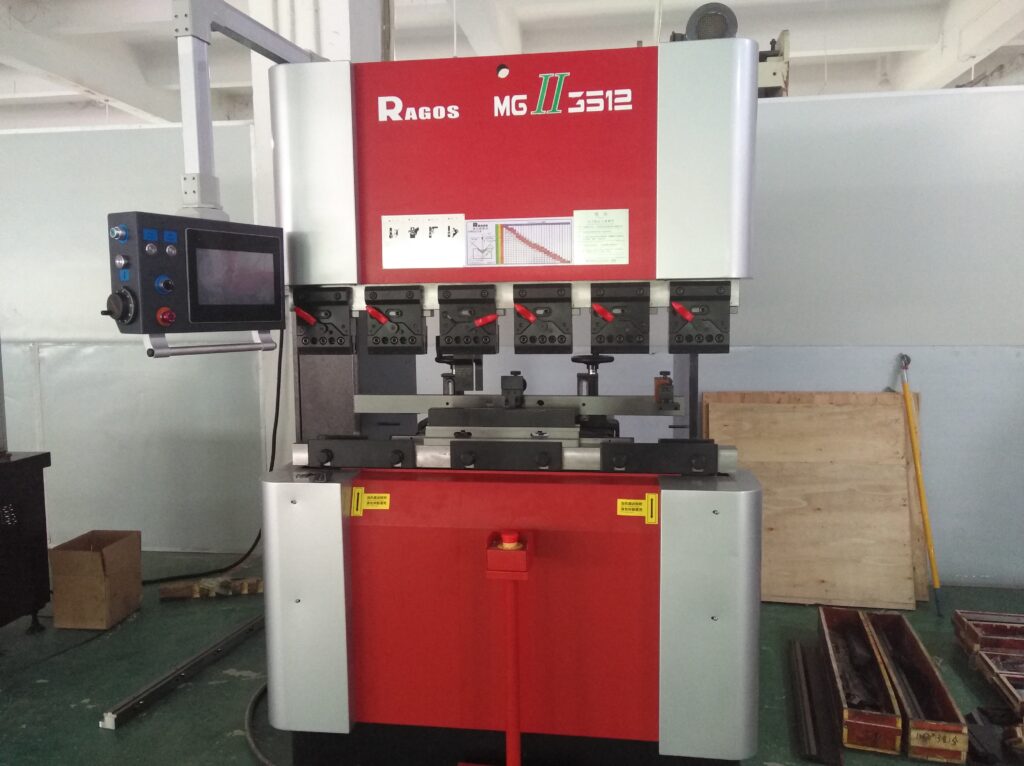
Quality Control and Standards
Importance of Quality Control in Bending Processes
Quality control ensures that the bent parts meet the required specifications and standards, minimizing defects and ensuring consistency.
Common Standards and Certifications
- ISO: International standards for quality management.
- ASTM: Standards for material properties and testing methods.
Inspection Techniques
- Visual Inspection: Checking for visible defects and ensuring the correct bend angles.
- Measuring Tools: Using calipers and micrometers to measure dimensions accurately.
- Non-Destructive Testing: Techniques like ultrasonic testing to detect internal flaws without damaging the part.
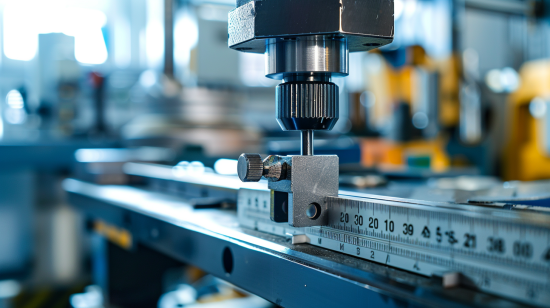
Applications
Automotive Industry
• Car Body Panels: Sheet metal bending is a big deal in making the external panels on cars. These panels need to be exact and smooth to fit right and look good while keeping the vehicle safe and looking good.
• Exhaust Systems: Sheet metal bending is used to make the various shapes and curves needed for exhaust systems to fit right and work well within the car’s design.
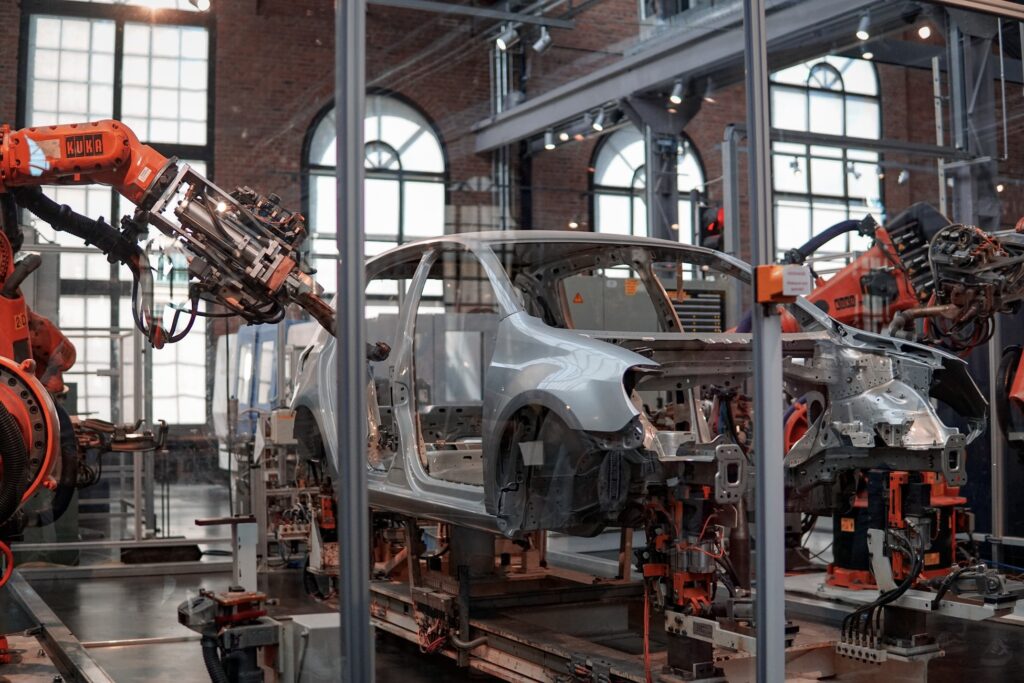
Aerospace Industry
Aircraft Fuselage Components: You need to bend metal precisely to make the shapes needed for fuselage components that are aerodynamic and meet strict safety and performance standards.
• Engine Parts: Different engine parts, like brackets and housings, are bent to exact specifications to handle the high pressures and temperatures they’ll see while flying.
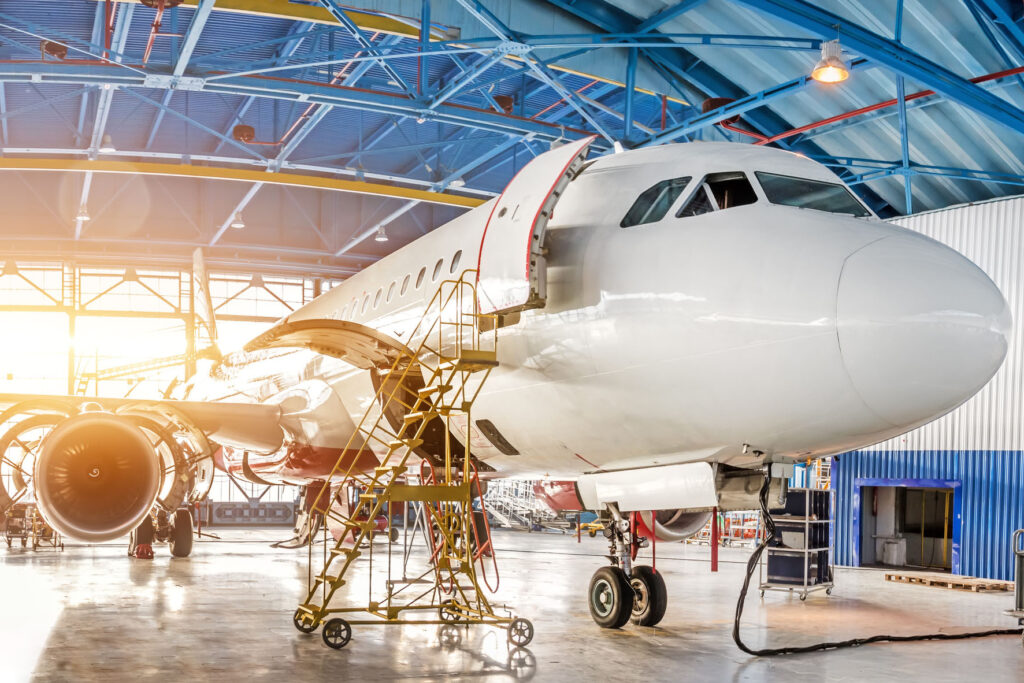
Consumer Electronics
• Enclosures: You have to bend metal precisely to make enclosures for electronics to protect the stuff inside and make the outside look good and work right.
• Frames: You bend metal to make frames for things like laptops and tablets to be strong and hold everything together while still being light.
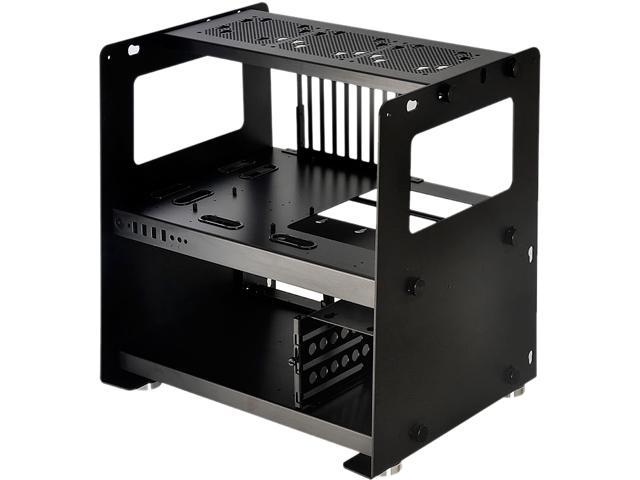
Industrial Applications
• Machinery Housings: You use bent sheet metal to make protective housings for machinery to protect the important stuff inside from weather and wear.
• Control Panels: You bend metal to make control panels that fit the design you need and are easy for people to use.

Medical Equipment
• Device Casings: You need custom casings to protect the sensitive equipment in medical devices and make them easy to use in hospitals and clinics.
• Instrument Panels: You bend metal precisely to make instrument panels that are easy to use and reliable for doctors and nurses.
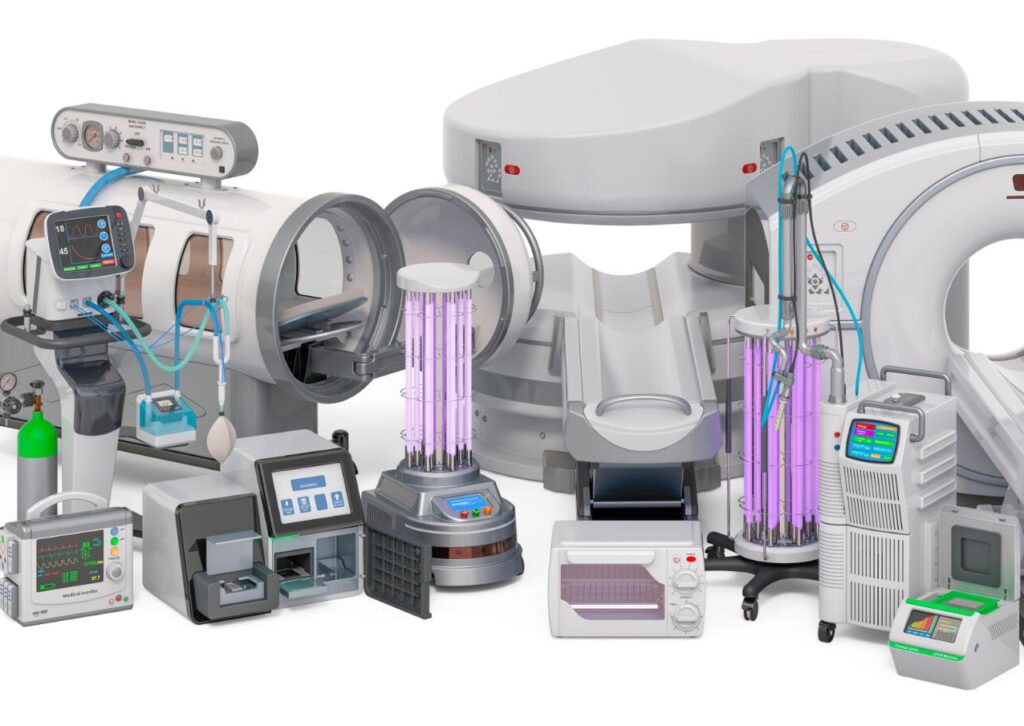
Detailed Processes and Techniques
Step-by-Step Process of Sheet Metal Bending with a CNC Press Brake
- Calculate the Design Parameters: You need to know the force you need, where to bend, and what order you’re bending.
- Set Up the Press Brake: Input the design parameters into the CNC machine, put the right tool and die in place.
- Align the Part: You put the metal between the tool and die.
- Engage the Press Brake: You push the button and it bends the metal where you told it to.
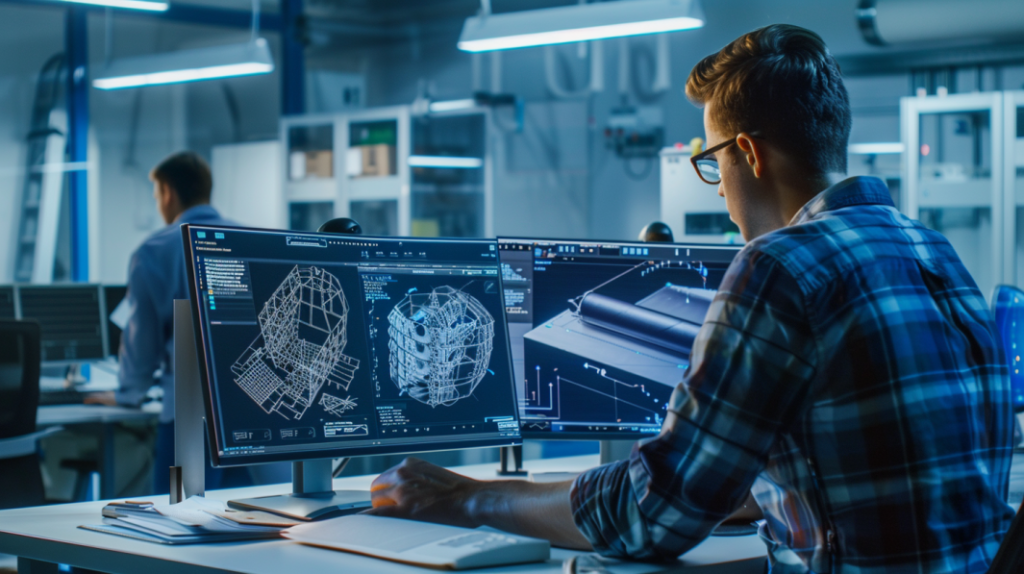
How Laser Cutting Makes You Better at Bending
Laser cutting helps you bend better by making a nice, clean edge on the metal that makes it easier for you to bend it where you want it to go. It also saves time for you to get ready and make it easier for you to bend stuff.
How Fiber Laser Cutting Makes You Better at Bending
Fiber laser cutting helps you bend better by making fewer mistakes and throwing away fewer parts. This helps you save money and make better use of your material. It also makes it easier for you to cut stuff faster to bend it better.
Types of Metals for Bending Sheet Metal
• Steel (Mild Steel, Stainless Steel): Really strong metal that can be used for a lot of things.
• Aluminum: Light and doesn’t rust, so it’s great for aerospace and electronics.
• Copper: Conductive and easy to bend, so it’s perfect for electrical stuff.
• Brass: Looks good and is easy to work with, so it’s used in a lot of decorative things.
• Galvanized Steel: Doesn’t cost much and doesn’t rust, so it’s used for a lot of industrial things.
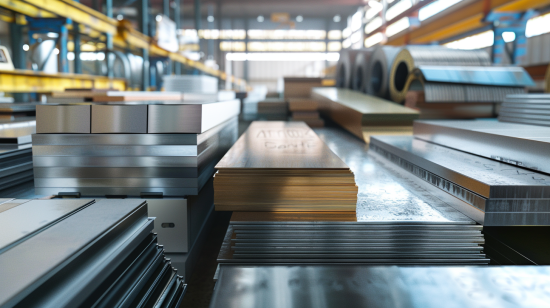
Common Questions and Answers
Accuracy of Sheet Metal Bending
You can hold tolerances of +/-0.004 inches, especially if you use laser-cut edges and CNC machines to bend your stuff.
How Much Does It Cost to Bend Sheet Metal?
It depends on how hard it is to bend, how many bends you have to make, and how much work it is. If you bend a lot of stuff, it’s cheaper to do it with a machine.
Should You Bend Sheet Metal or Die Cast It?
If you’re making a few parts, it’s cheaper to bend it. If you’re making a lot of parts, it’s cheaper to die cast it. It’s easier to set up and costs less to start to bend stuff
Pros and Cons of CO2 Laser Cutting
• Pros: Super accurate, automatic, faster, and cheaper.
• Cons: Costs a lot, need to know what you’re doing, might make stuff you don’t want to breathe, uses a lot of power.
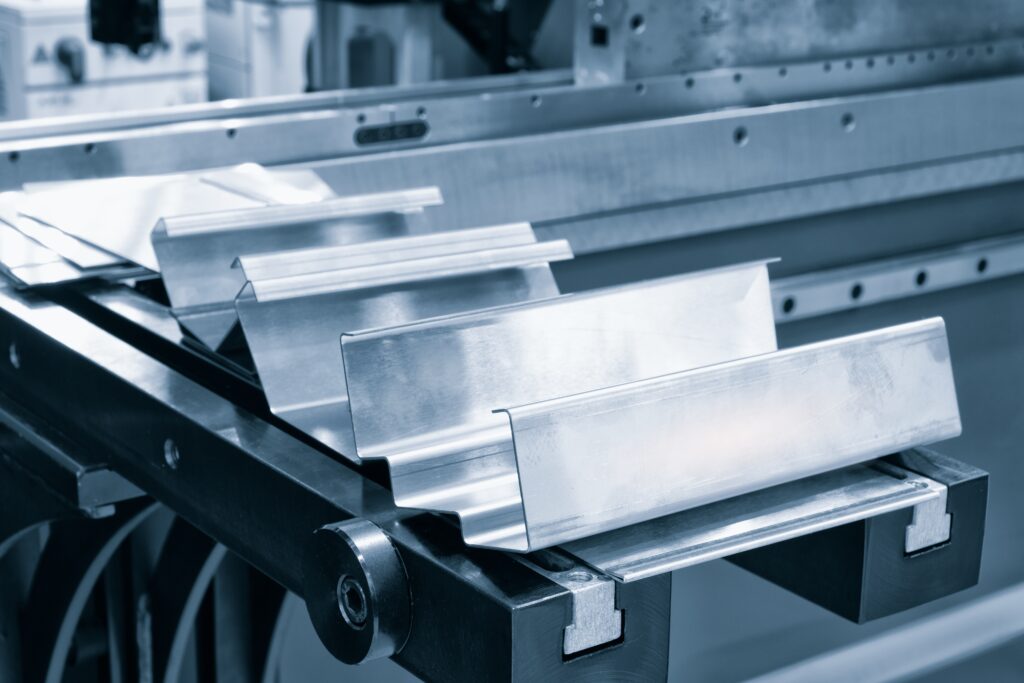
Conclusion
Sheet metal bending is a big deal in manufacturing because it’s accurate, can be used in a lot of ways, and doesn’t cost a lot. If you know what you’re doing, you can make good stuff that lasts and works for a long time.