Sheet metal fabrication is a fundamental form of modern manufacturing that is used to create parts utilized in robotics, medicine, home appliances, and consumer electronics. Because of its many applications, knowing the main sheet metal fabrication processes can save your company time and money and help you make high-quality components.
Sheet metal fabrication is the process of cutting and shaping thin metal sheets (less than 6 mm thick) into the parts you desire. This process includes shearing, blanking, punching, piercing, and more. Each of these processes has its own benefits and is necessary to produce the parts you need for your products.
By mastering these different processes, you can make your manufacturing process more efficient and improve the quality of your products. Let’s look at the main sheet metal fabrication processes, how they work, what their benefits are, and what their limitations are. Knowing this information will help you determine which processes you need to use to make your parts.
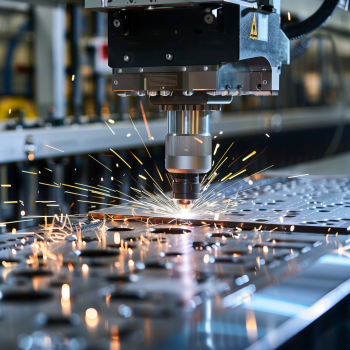
What is Shearing in Sheet Metal Fabrication?
Shearing is a fundamental process in sheet metal fabrication. It's cutting in a straight line in metal sheets without forming chips or using burning/melting. Here's how it works:
• How It Works: The metal sheet goes between two blades. The bottom blade doesn’t move, and the top blade slices through the metal in a fast, powerful motion. This process requires the blades to be aligned perfectly to make clean cuts.
• Tools: Shearing equipment can be manual, electric, pneumatic, or hydraulic. Manual shears are used for small-scale operations or thinner metals. Electric and pneumatic shears are used for medium-scale operations because they provide more power and efficiency. Hydraulic shears are used for heavy-duty applications because they can cut thicker and harder metals with high precision.
• How It’s Used: Shearing is excellent for cutting large sheets into smaller, manageable pieces. It’s used often as a first step in metalworking to get the raw material ready for further processing.
Benefits of Shearing
Shearing is cost-effective for high-volume production because it lets you cut fast with minimal waste. Shearing doesn’t make a big cutting kerf, which is the material that’s removed by the cutting process, unlike thermal cutting processes. This efficiency is critical to maintaining the integrity and size of the material and makes it ideal for making large, straight cuts across different metal thicknesses.
Limitations of Shearing
Despite its benefits, shearing has some limitations. It’s not good for cutting metals into complex shapes or intricate designs. Harder materials, like tungsten, can damage the cutting blades, which makes it more expensive to maintain. Sometimes burring can happen, which is a rough or raised edge, especially with larger-diameter metals or when the blades don’t have enough clearance. Making sure the metal is clamped securely is critical to minimize these issues.
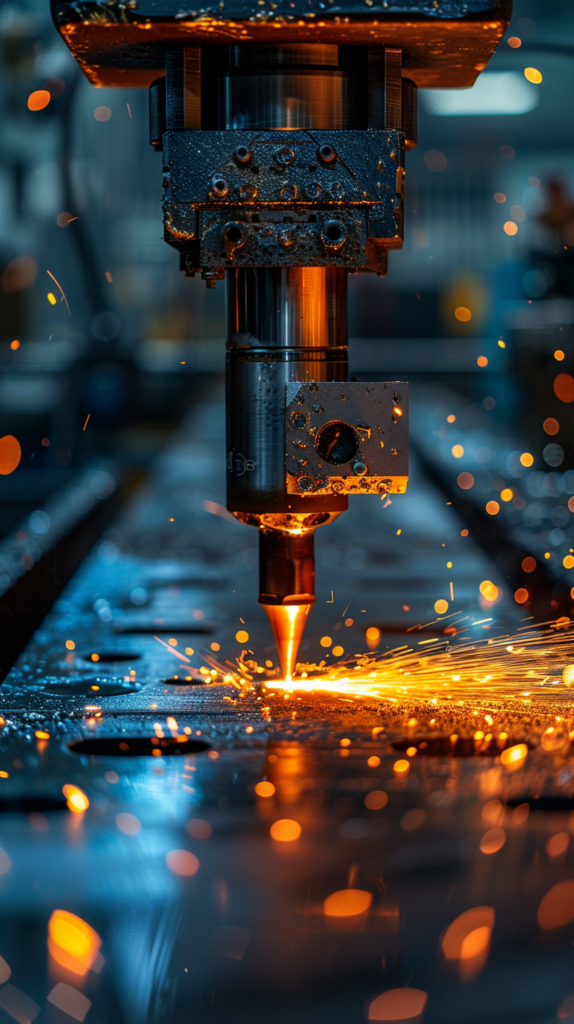
How Does Blanking Work?
Blanking is the process of cutting a part out of sheet metal using a punch and die. It uses extreme shearing forces to remove material, with the blank being the part you want. Here’s what you need to know:
• Standard Blanking: Uses one downward force to cut out the shape from the sheet metal. This process tends to produce more scrap material because it doesn’t control the flow of metal as well as other methods.
• Fine Blanking: Uses three loads—holding force, counterforce, and blanking force. This process clamps the sheet tightly and applies a counterforce underneath the sheet to minimize burrs and create smoother edges. Fine blanking allows for tighter tolerances and smoother finishes, so it’s great for precision parts.
Materials and Use Cases
Blanking is versatile and can be used on a variety of materials, including aluminum, alloy steel, brass, copper, and stainless steel. It’s commonly used to make auto parts, electronics, and other industrial items where you need precise shapes and sizes.
Advantages and Disadvantages
Blanking is fast and effective for high-volume production. By setting up tools and planning correctly, you can significantly reduce scrap, which improves the overall efficiency of the material. However, the process is expensive. The tools for blanking have to be made and maintained precisely, and the equipment is costly. Additionally, blanking often requires secondary operations like deburring to remove burrs on the edges and achieve the desired finish.
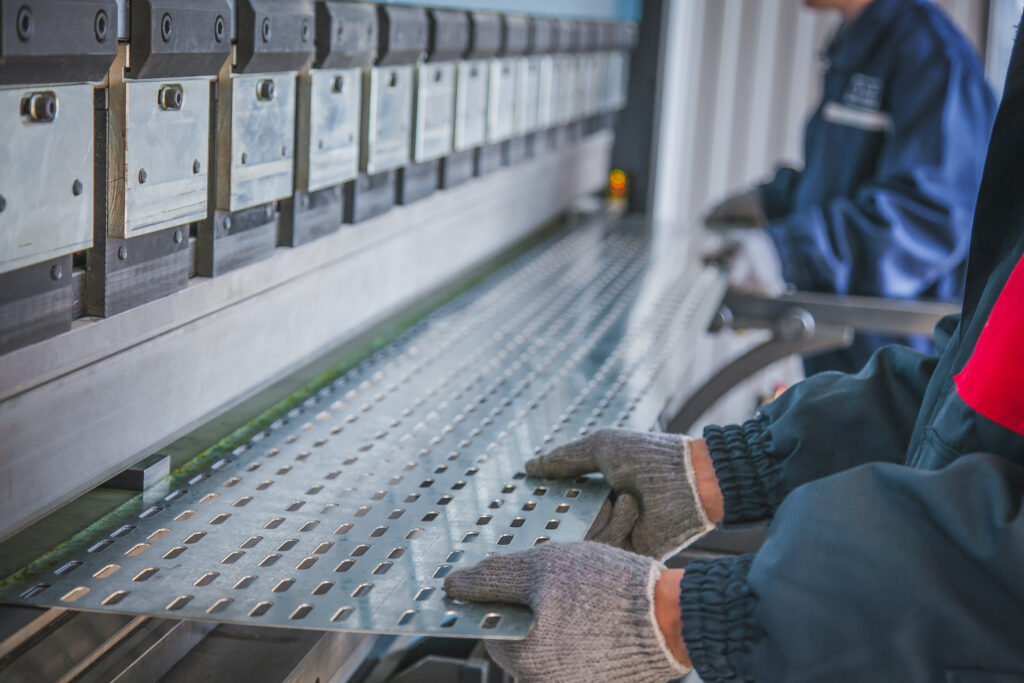
What is Punching in Sheet Metal Fabrication?
Punching is the process of creating holes or shapes by removing material from metal sheets. The material removed, unlike in blanking, is scrap. It is particularly useful for creating patterns or features in the sheet metal.
• How It Works: Punching machines can be manual or CNC-controlled. CNC (Computer Numerical Control) punching machines offer better precision and automation because they can continually feed and process sheet metal. The sheet metal goes under a punch, which moves down to remove the material.
• How It’s Used: Punching is used to make automobile frames, create ventilation holes, and produce household items. It’s necessary for applications where you need repetitive, consistent holes or shapes.
Benefits of Punching
Punching is cost-effective for making standard shapes and sizes because you typically don’t need custom tooling for each shape. It can also make dimples and louvers, which are helpful for creating structural features and improving the functionality of metal parts. You don’t need secondary operations, like drilling, when you use this process, so it simplifies your manufacturing process.
Limitations of Punching
Setting up for punching can take time, especially for custom shapes that require specific tool setups. While it’s economical for mass production, it’s not cost-effective for one-off parts because of the time and expense of setting up the tool. Custom tooling can be expensive, so it’s not ideal for low-volume production runs.
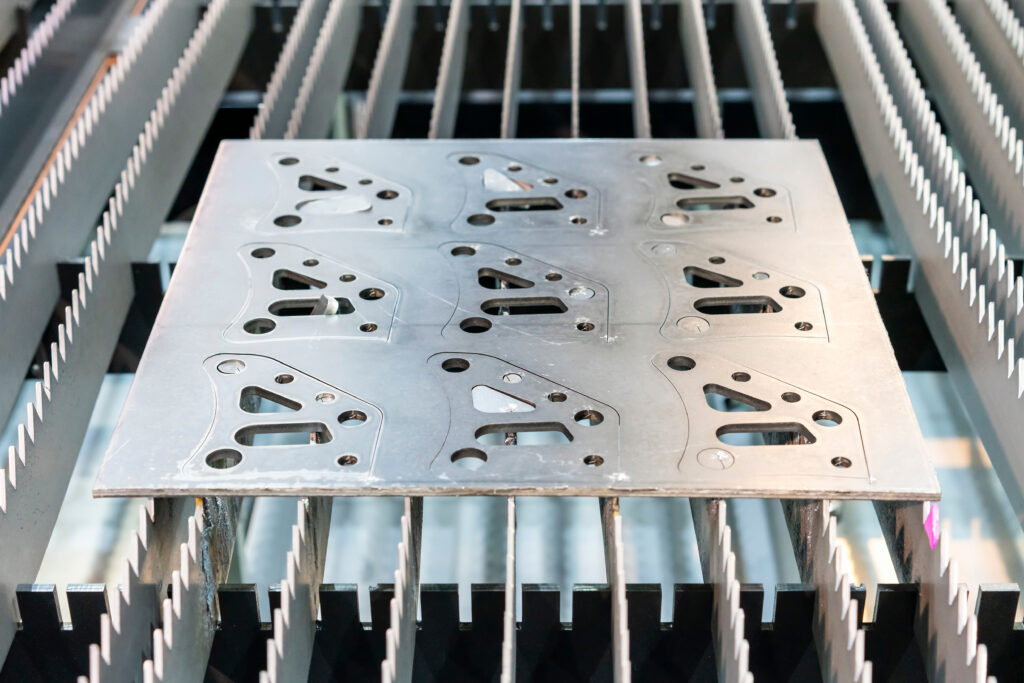
Exploring Piercing and Other Processes
Piercing
Piercing is similar to punching, but it is used to create small holes or intricate patterns where the material you punch out is scrap. It uses the same equipment as punching, typically a punch and die setup. It is great for applications where you need precision and high detail, like creating vent holes or decorative patterns on metal surfaces.
Slotting and Perforating
Slotting
Slotting is punching out rectangular pieces from a metal sheet. This process is used to create slots or notches in sheet metal that are needed to assemble components or create specific designs. Slotting is common in the manufacturing of electrical panels and enclosures where you need precise slots for placing components.
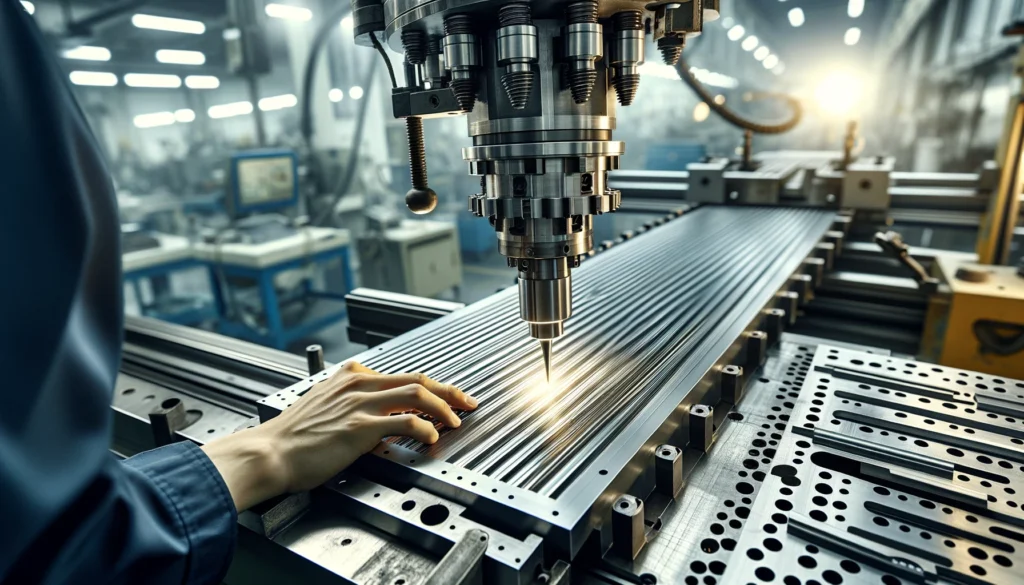
Perforating
Perforating is punching out small, often repetitive patterns from sheet metal. You can do this in one operation for large sheets using a roller conveyor system. Perforated metal sheets are used in filters, grilles, and decorative panels because they let air or light pass through while maintaining structural integrity.
Notching and Nibbling
Notching
Notching removes extra material from the edges of sheet metal. It’s used to create precise edge profiles and prepare metal pieces for bending or forming operations. Notching is common in the production of frames, supports, and various structural components.
Nibbling
Nibbling uses a series of punches that go up and down to create specific cutouts in sheet metal. It’s great for making complex shapes that would be hard to make with one punch. It’s very precise and flexible, so it’s good for custom and intricate designs.
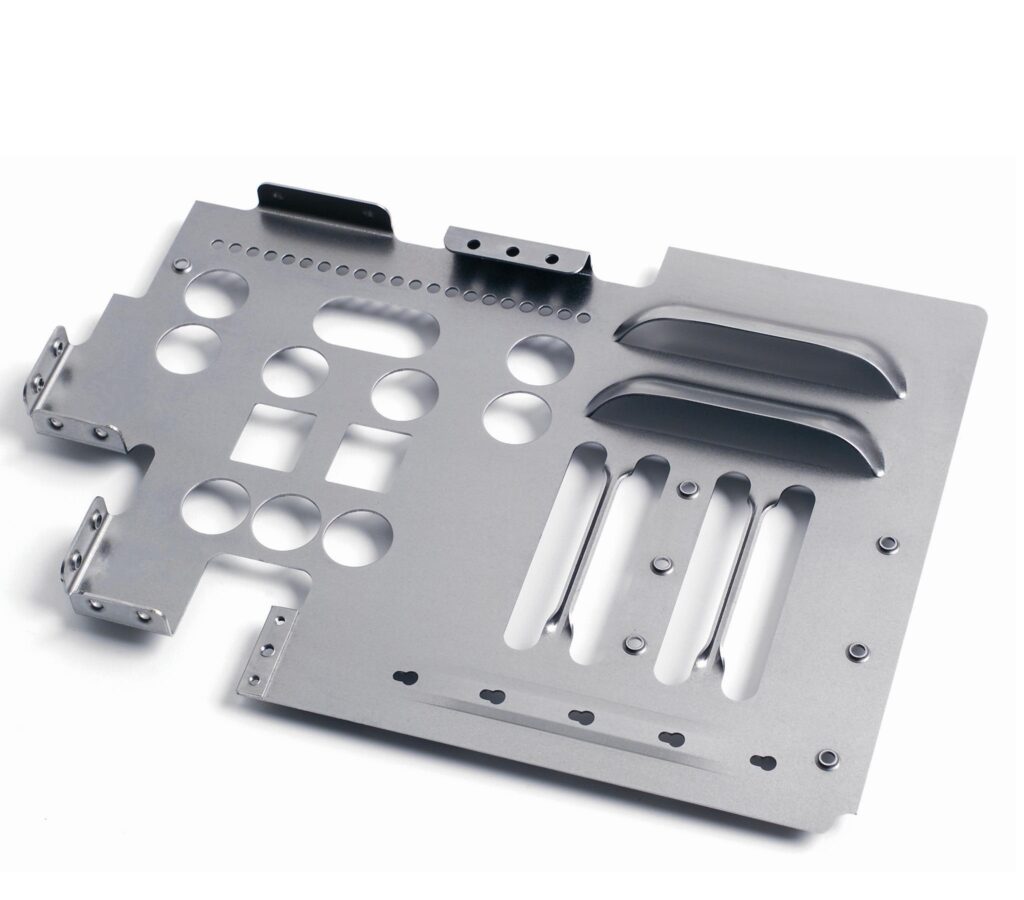
Lancing and Slitting
Lancing
Lancing is making partial cuts through sheet metal without removing any material, so you have no scrap. You can then bend or form the attached material into various shapes. Lancing is used to make louvers, tabs, and vents, which are common in automotive and appliance components.
Slitting
Slitting is making lengthwise cuts through coiled metal sheets to make narrower strips. This is essential for preparing materials for further processing, like roll forming or stamping. Slitting is efficient and doesn’t produce scrap, making it a cost-effective choice for cutting large sheets into smaller, more manageable widths.
Parting, Cutoff, and Trimming
Parting
Parting is separating sheet metal into individual pieces by removing the material that connects them. It’s often used with other cutting operations to make final parts that are ready for assembly or further processing. Parting is common in making complex assemblies where you cut multiple pieces from one sheet.
Cutoff
Cutoff is making straight-line cuts to separate a piece from the main sheet. This is typically done in high-volume production settings where you need to keep feeding the sheet continuously. This doesn’t produce scrap, and you can make straight, curved, or angled cuts depending on your design requirements.
Trimming
Trimming is removing extra material and irregularities from the edges of sheet metal parts to get precise dimensions and a clean finish. This finishing operation is used for components that need tight tolerances and a polished appearance, like in the automotive and consumer electronics industries.
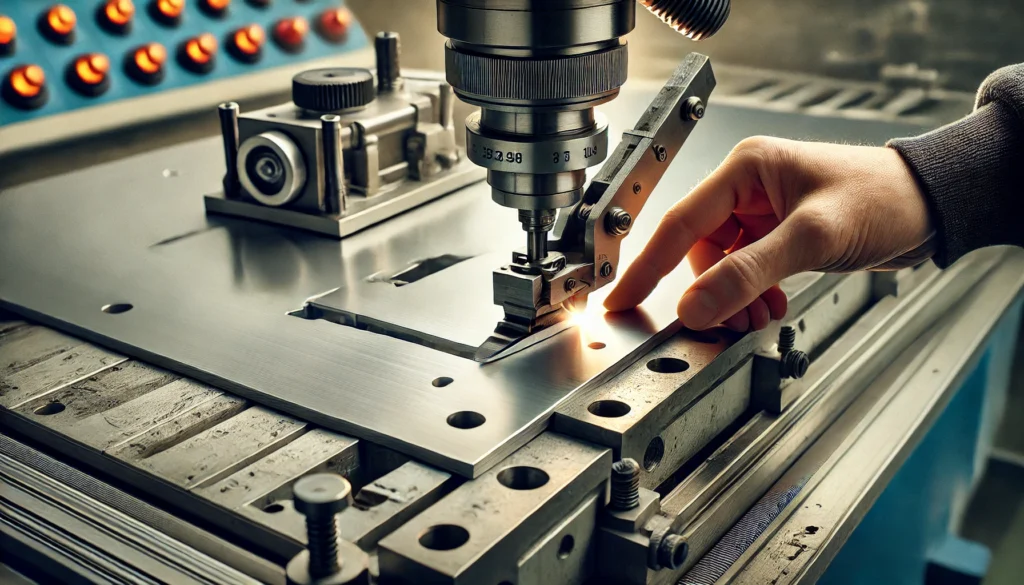
Shaving and Dinking
Shaving
Shaving is a finishing operation that shaves off small amounts of metal from a piece you’ve already blanked or punched. It improves the accuracy and smoothness of the edges, getting you tolerances down to 0.025 mm. Shaving is used in high-precision applications where exact dimensions are critical.
Dinking
Dinking, or die cutting, uses hollow dies to punch through soft, low-strength metals like aluminum and brass. This is typically done with a mechanical press, and the edges of the dies are often beveled to reduce wear. Dinking is used for making shapes in soft metals that need very little force to cut.
Conclusion
Sheet metal fabrication processes are critical to producing precise, durable parts for a wide range of industries. By knowing the different methods like shearing, blanking, punching, and piercing, you can improve your manufacturing capabilities, making high-quality parts that meet industry standards. As technology continues to advance, these processes become faster, more efficient, and more precise, allowing for innovation and better manufacturing practices.