If you’ve ever wondered how sheet metal parts get those nice, folded edges, you’re thinking about hemming. Hemming is important because it makes parts safe to handle, adds strength, and makes sheet metal parts look better. In industries like automotive and aerospace, you need to hem precisely for both function and looks.
Sheet metal hemming is a fabrication process where you fold the edge of a sheet metal part over to create a smooth, strong edge that looks good. People use hemming to make parts safe, add strength, and make the parts look good. There are different ways to hem parts, including conventional, roll, table, press, and robot hemming, and they all have unique advantages for specific applications.
When you understand the different ways to hem parts, you can pick the right way to hem your parts. Each way to hem parts has unique advantages and is good for specific applications. From conventional to robot hemming, I’ll explain the different ways to hem parts, the benefits of each, and how they can help you with your fabrication projects.
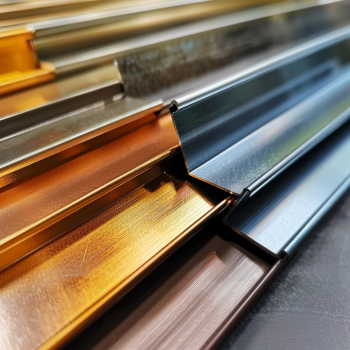
What is Sheet Metal Hemming?
Sheet metal hemming is folding the edge of a piece of sheet metal over to create a smooth, rounded edge. People do this in manufacturing to make the edge of the metal stronger, make it safe by getting rid of sharp edges, and make it look good. People use hemming in automotive, aerospace, and other industries where they need things to be accurate and last a long time.
Types of Hemming Processes
Conventional Hemming
Conventional hemming is the simplest way to hem parts. You use a press to fold the metal edge over. People use this when they don’t need to make a lot of parts and when they’re making simple parts. People use conventional hemming in automotive and appliance manufacturing. The good thing about conventional hemming is that it’s simple to do and set up, but it’s not good for complicated shapes or making a lot of parts quickly because it’s slower.
Roll Hemming
Roll hemming uses a roller to fold the metal edge. It’s an automated process that gives you better results than conventional hemming. People use roll hemming when they’re making a lot of parts or when they’re making parts with complicated shapes. People in the automotive industry use roll hemming to make car doors, hoods, and other parts. The good thing about roll hemming is that it’s more accurate and faster, making it good for high-volume manufacturing.
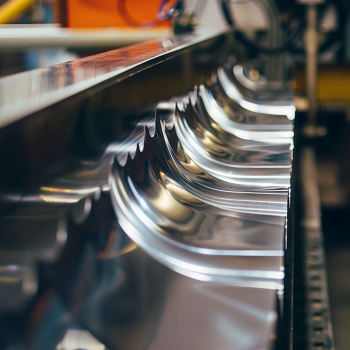
Table Hemming
Table hemming is when you put the sheet metal on a table and use a press or roller to fold the edge. It’s a good process because you can do a lot of different sizes and thicknesses of sheet metal. People use table hemming when they’re making a lot of different parts and need a lot of different hemming processes. The good thing about table hemming is that you can work with a lot of different materials and thicknesses, making it good for making a few parts at a time.
Press Hemming
Press hemming is when you use a press machine to fold the metal edge. It’s a lot like conventional hemming, but it’s more accurate and controlled. People use press hemming when they need to make parts that have to be perfect and strong. People in the aerospace and automotive industries use press hemming when they need to make parts that have to be perfect. The good thing about press hemming is that you get the same results every time, and you can use it to make a few parts or a lot of parts.
Robot Hemming
Robot hemming is when you use a robot arm to hem parts. It’s an automated process that gives you accurate and repeatable results. People use robot hemming when they need to make a lot of parts that are complicated. People in the automotive industry use robot hemming to put cars together. The good thing about robot hemming is that you can use it to make a lot of different parts, and it’s accurate and can handle complicated shapes.
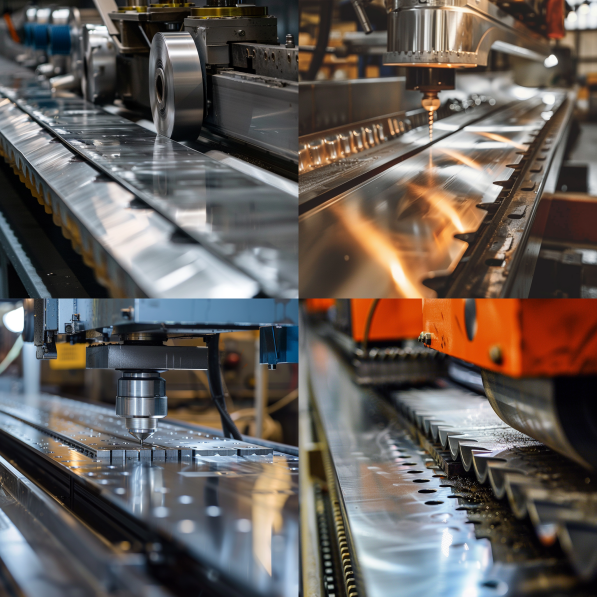
Hemming Techniques
Flat Hem or Closed Hem
When you fold the edge of the metal all the way over, that’s called a flat or closed hem. You use this when you need a strong, rigid edge. You see closed hems a lot on automotive and appliance parts because they’re tough and strong. They look better and they keep the weather out.
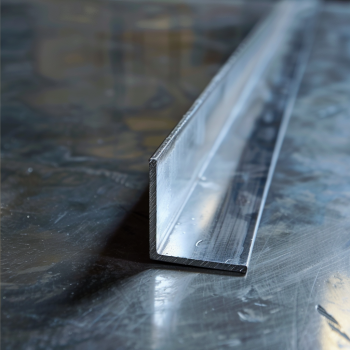
Open Hem
When you fold the edge of the metal over but don’t fold it all the way closed, that’s an open hem. You use this when you want the joint to have some flexibility. You see open hems a lot on parts that need to fit together but also need to move a little. They’re easier to make and are more forgiving if you’re a little off on your fit and alignment.
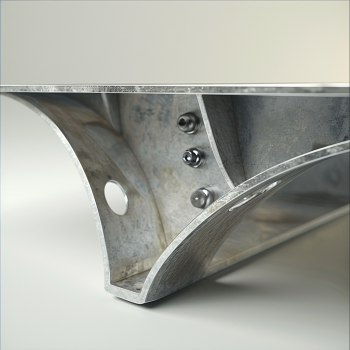
Teardrop Hem
When you fold the edge of the metal over to create a loop, it creates a teardrop shape. This is a teardrop hem. You use this for looks and to make the edge smoother. You see this on decorative metalwork and consumer products. It looks cool and keeps you from cutting yourself on a sharp edge.
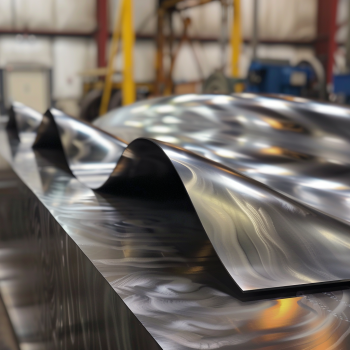
Rope Hem
A rope hem is when you fold the edge of the sheet metal over to create a rounded shape that looks like a rope. You use this for looks and to give the product a cool look. Rope hems make things look nice and also make the edge stronger.
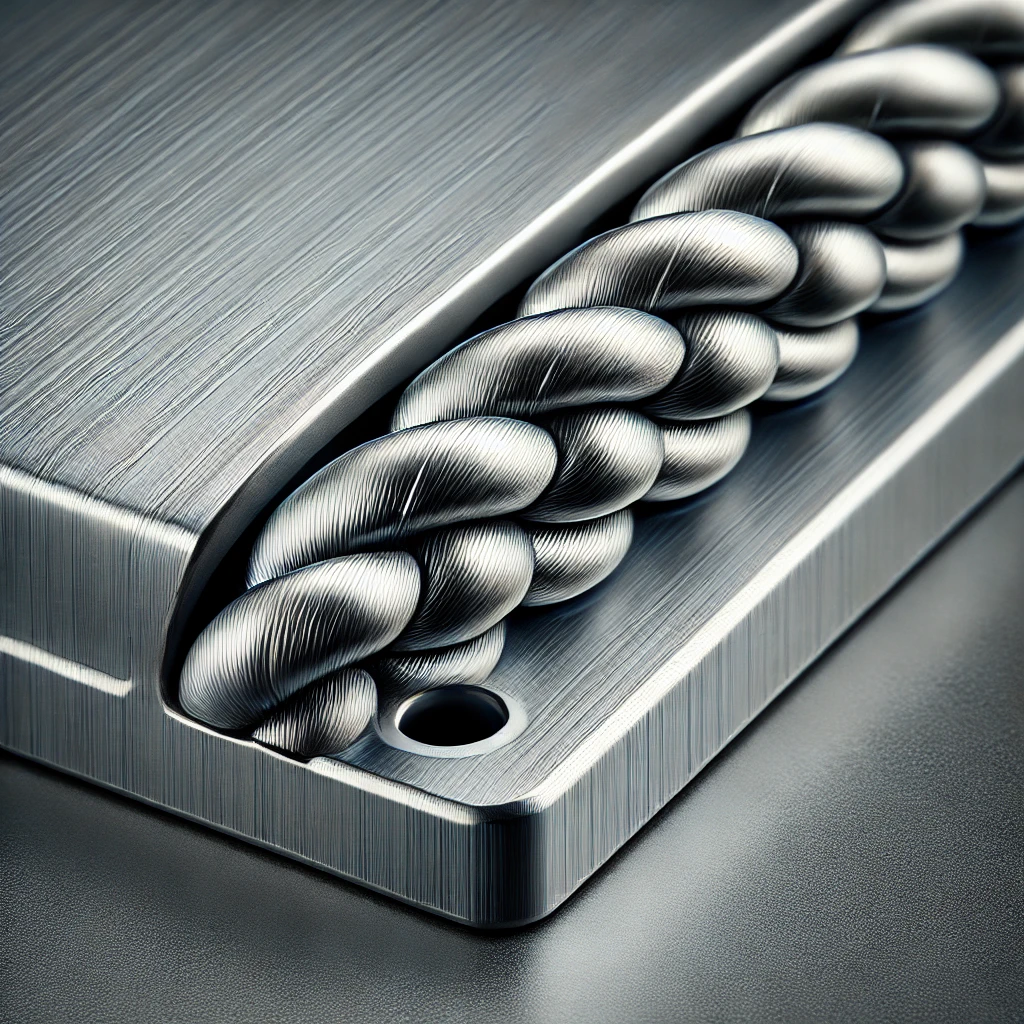
Rolled Hem
A rolled hem is when you fold the edge of the sheet metal over itself into a roll or curl. You use this to make a smooth, rounded edge. You see rolled hems on parts that need to look good, like consumer electronics and decorative items.
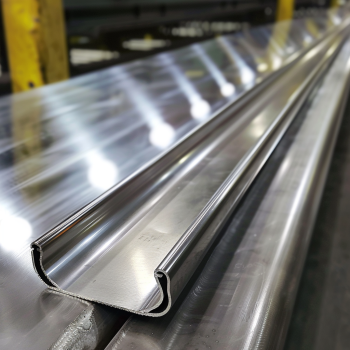
Capped Hem
A capped hem is when you fold the edge of the sheet metal over a cap or another piece of metal. You use this to make the edge stronger and give it a finished look. You see capped hems on enclosures and frames because they make the edge stronger and look nice.

Double Hem
A double hem is when you fold the edge of the metal over twice. This creates a very strong, durable edge. You see this on parts that need to be super tough, like heavy-duty enclosures and structural components. Double hems make the edge smooth and rounded and super strong.
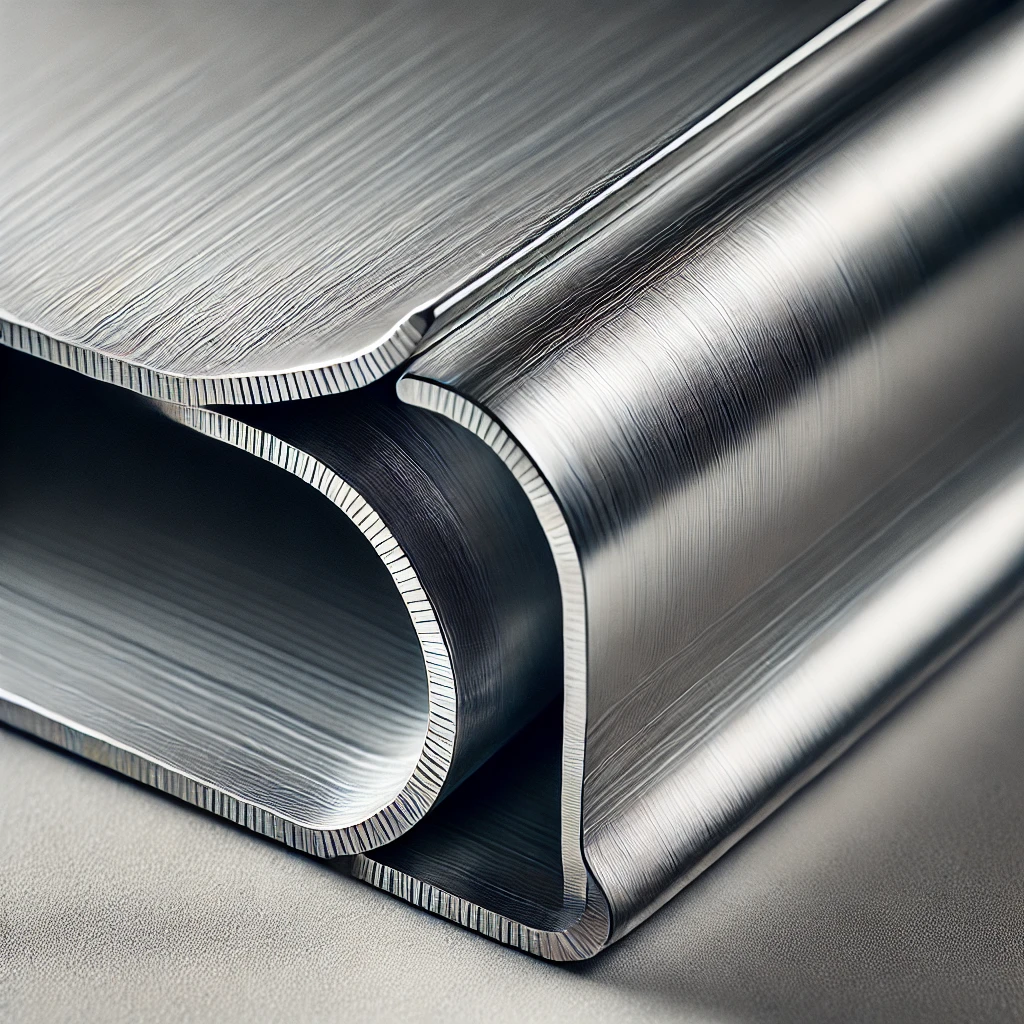
Quarter Hem
A quarter hem is when you fold the edge of the sheet metal over to create a quarter-circle profile. You do this for looks and to make the edge smoother and less likely to get damaged. You see quarter hems on consumer products and decorative panels.
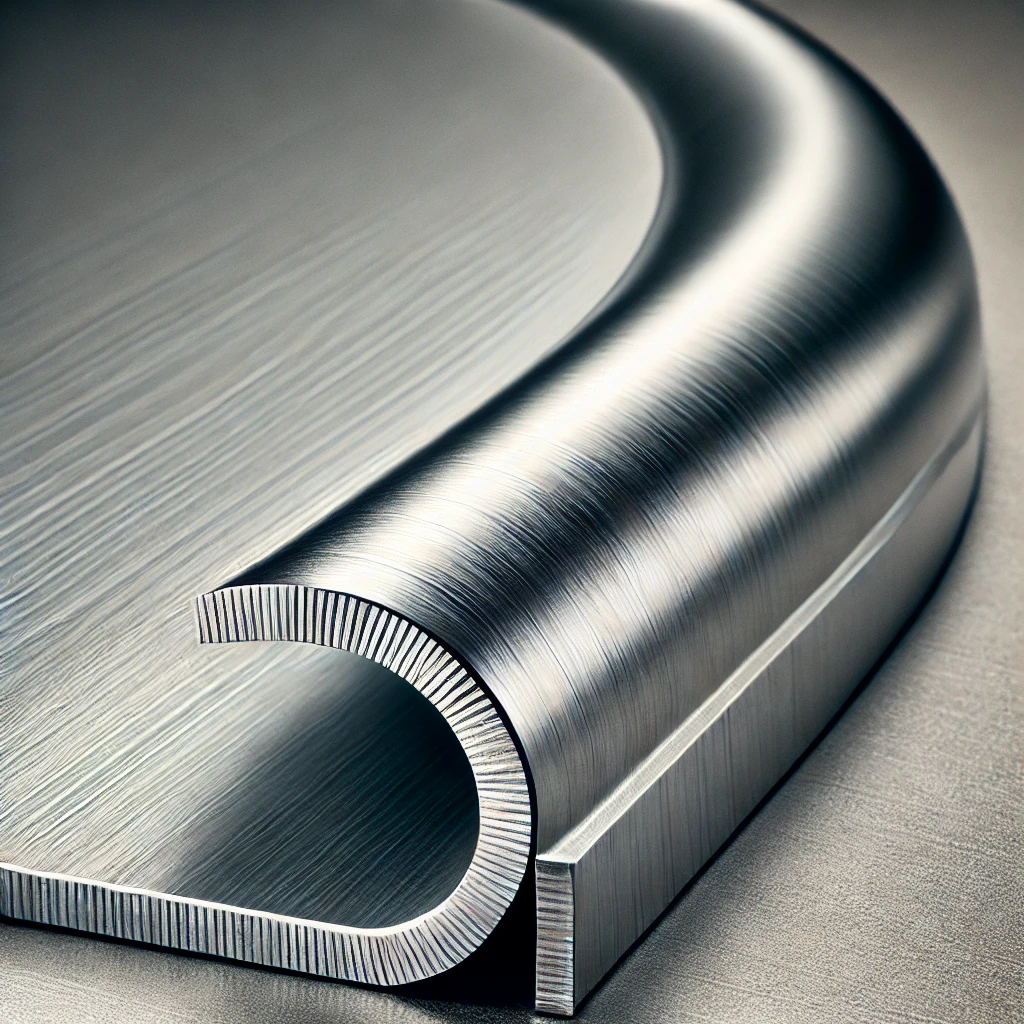
Edge Hem
An edge hem is when you fold the edge of the metal over itself. You do this to make a nice, finished edge and to make the part safer and stronger. You see edge hems on automotive and appliance parts because they make a simple, strong edge.

Step Hem
A step hem is when you create a stepped profile along the edge of the sheet metal. You do this to make the parts interlock or to create a specific design feature. Step hems make the part stronger and help you fit and align the parts better.
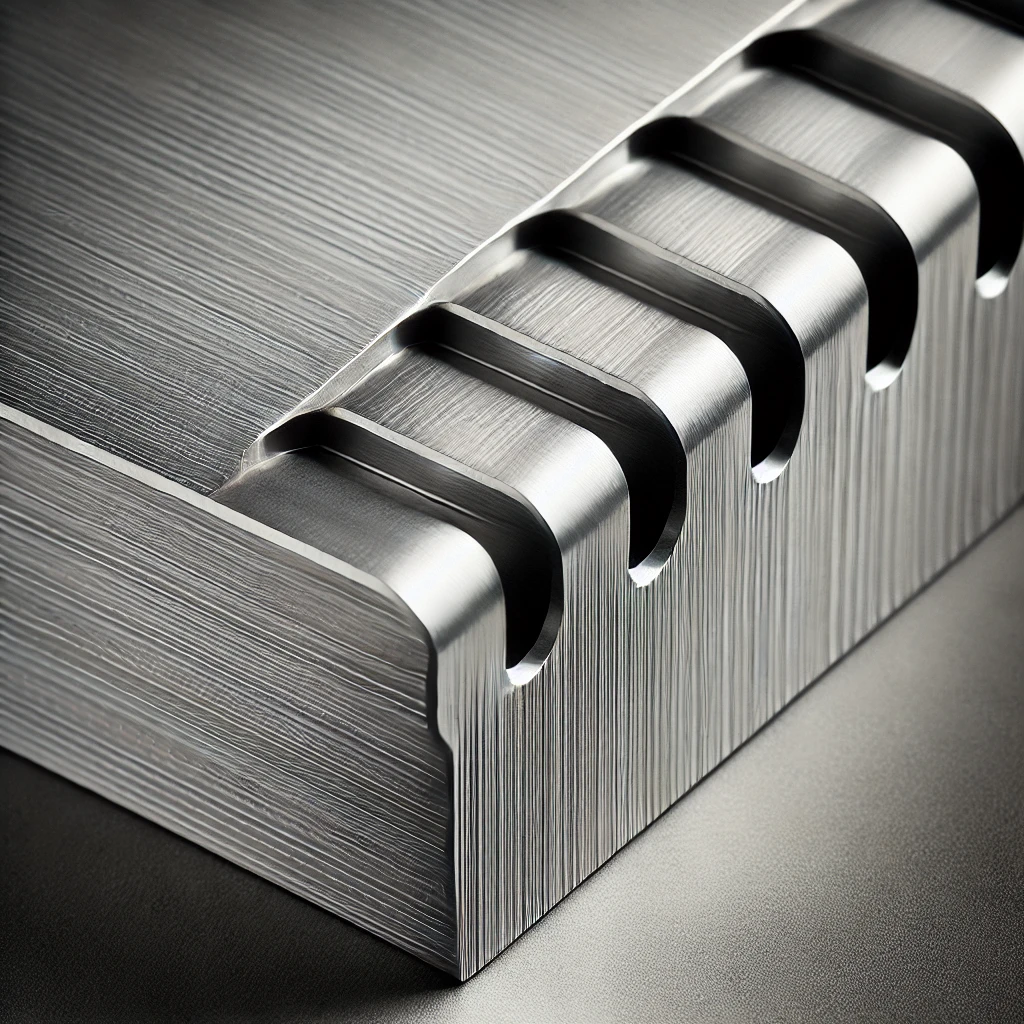
Curling Hem
Curling hems is when you roll the edge of the sheet metal into a curled shape. You do this for looks and to make the edge stronger. You see curling hems on a variety of consumer products and decorative items.
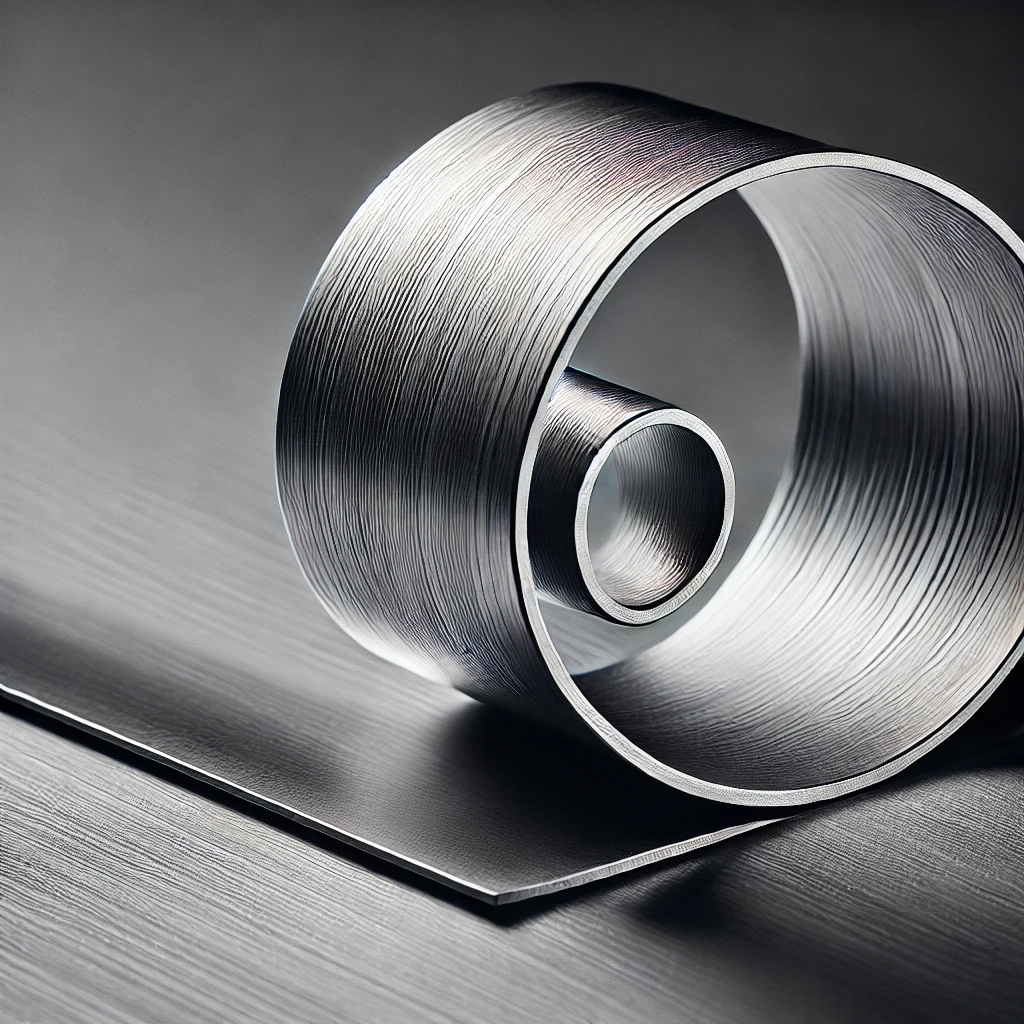
Hem with Sealant
A hem with sealant is when you put a sealant along the folded edge of the sheet metal. You do this to make a watertight or airtight seal and to make the part last longer and work better. You see hems with sealant on HVAC systems and outdoor equipment.
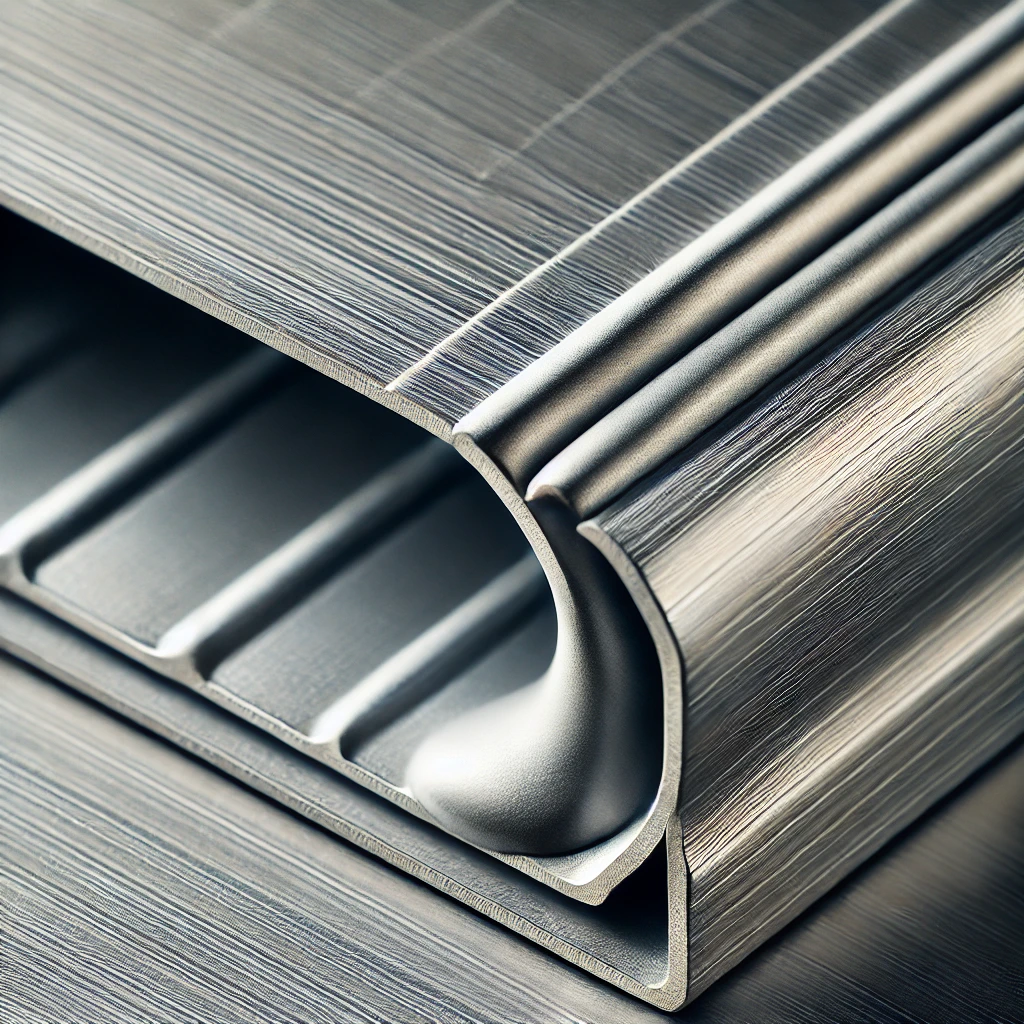
Lock Hem
A lock hem is when you fold the edge of the sheet metal in a way that locks it into place. You do this to make a strong, secure edge that won’t come apart. You see lock hems on structural parts because they need to be super strong and durable.
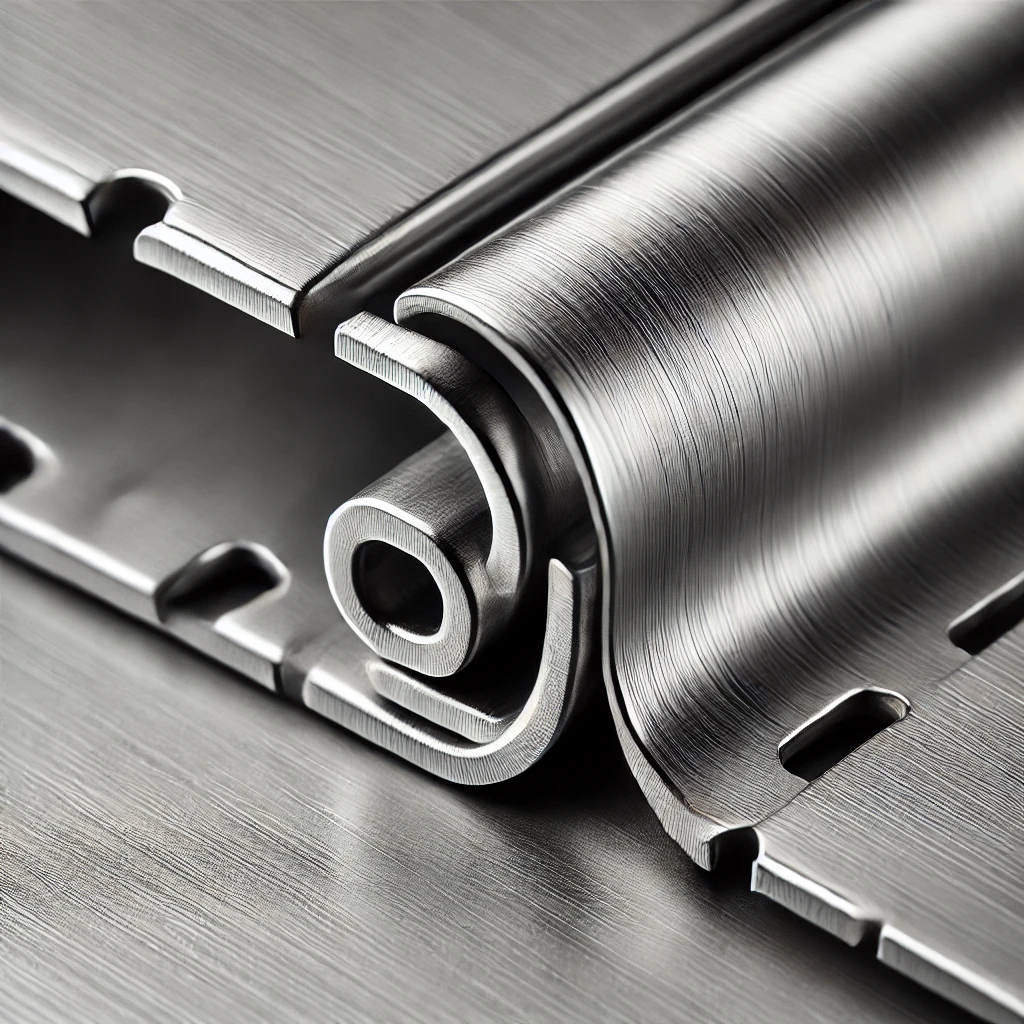
Hemming Equipment and Tools
Common Hemming Machines
Hemming machines can be manual presses or automated robotic systems. You choose your equipment based on how many parts you need to make, how accurate you need to be, and how hard the parts are to make. You use press machines, rollers, and robot arms to hem parts. Each machine has different advantages depending on the parts you’re making.
Choosing the Right Equipment
You have to pick the right hemming equipment if you want to make good parts. You need to think about the kind of metal you’re using, how thick it is, how many parts you need to make, and how hard the parts are to make. People use robot hemming when they need to be accurate and make a lot of parts. People use manual presses when they’re making a few parts and they’re easy to make.
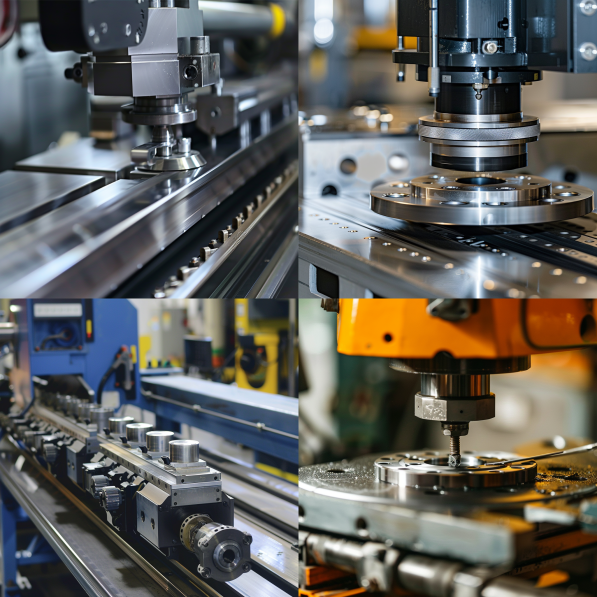
Quality Control in Hemming
Importance of Quality Control
You need to check your hemming to make sure your edges are smooth, strong, and don’t have any problems. You need to do this to make sure your parts look good and work right. You have to check your parts all the time to make sure you don’t have any problems.
Methods for Ensuring Quality
You check your parts by looking at them, measuring them, and pulling on them to make sure they’re strong. You can use a laser and a camera to check your parts. This helps you make sure your parts are good and you don’t waste time and money making bad parts.
Common Issues and Solutions
Sometimes your hems don’t look right, or you get wrinkles or cracks in them. You can fix these problems by changing the way you make your part, using the right tools, and making sure you’re using the right material. You also need to keep your hemming machines working right so you don’t have problems.
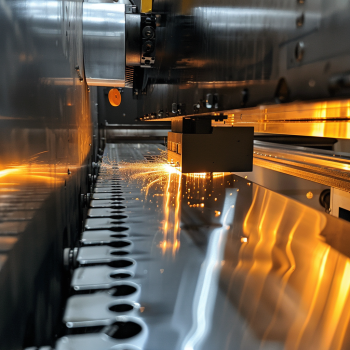
Innovations in Hemming Technology
Recent Advancements
The latest advancements in hemming technology are better robots and better software. These let you be more accurate, faster, and work with more complicated shapes. For example, the newest robot hemming systems can do more than one hem in one setup. This lets you make parts faster and cheaper.
Impact on Efficiency and Precision
The new hemming technology makes you more efficient and accurate when you’re making parts. The robots do the work, so you don’t make mistakes, and you get the same good parts every time you make them. This is important in the automotive and aerospace industries when you need to be accurate and your parts have to work right.
Future Trends
In the future, hemming technology will use more artificial intelligence and machine learning to control the process and tell you when your machines need to be fixed. They will also use sensors and computers to make sure you’re doing your hems the right way. These new things will help you make better parts faster and cheaper than you can today.

Material Considerations in Hemming
Different Metal Behaviors
Different metals act differently when you hem them. For example, aluminum can crack more easily than steel because it’s not as stretchy. You need to know how your metal works to pick the right way to hem it and make good parts.
Choosing the Right Material
The kind of metal you use affects how you hem it. You have to think about how stretchy it is, how thick it is, and what you’re using it for. For example, if you use high-strength steel, you need better equipment and have to be more careful to make sure you don’t mess up your parts.
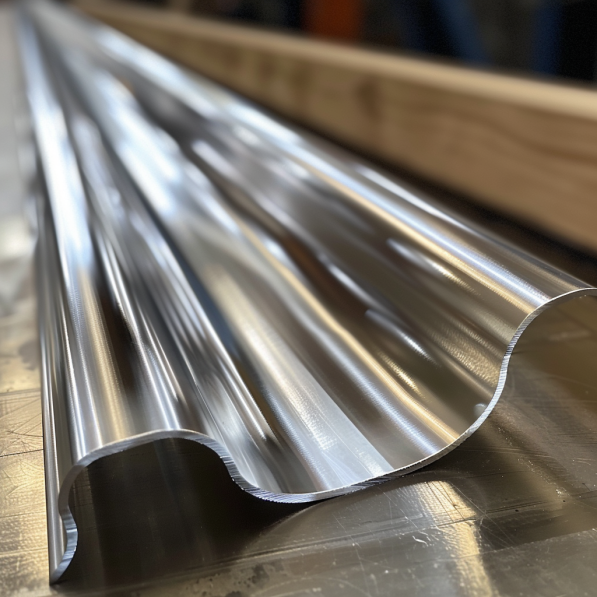
Hemming Tolerances
Importance of Tolerances
Tolerances are how close you need to make your parts. This is important in industries like aerospace, where you need to make your parts perfect. You have to make sure your parts fit together right and work right.
Achieving Tight Tolerances
You need to control how you hem your parts, use good tools, and check your parts all the time to make sure you make your parts right. You can use good equipment and robots to make your parts right every time you make them.
Tooling and Die Design
Role of Tooling
The tools you use to hem parts are important. If you design your tools right, you can make your parts last longer, make fewer bad parts, and make your machines last longer.
Custom Tooling
You can design your tools to work with your parts. This is good when you need to make parts that are different shapes or have different materials. This helps you make better parts and make them faster.
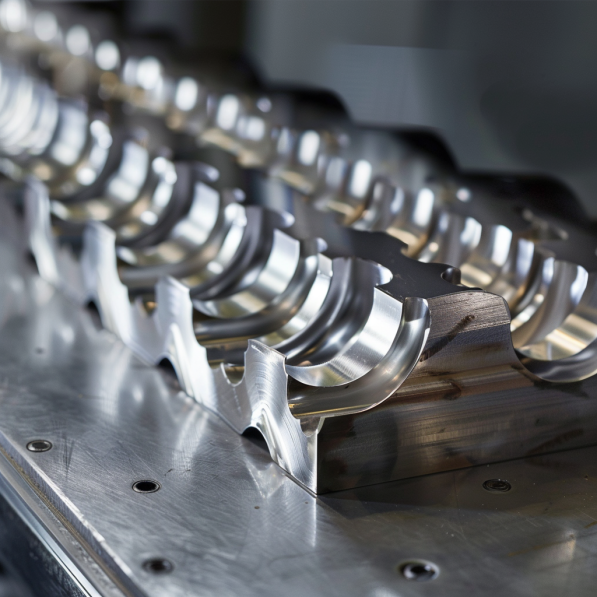
Lubrication in Hemming
Reducing Friction
Lubrication is important when you hem parts. It helps your parts move better and not stick. When you use the right lubrication, you make better hems and fewer bad parts.
Choosing the Right Lubricant
The kind of lubrication you use and how you put it on your metal affect how your parts look. You need to use the right lubrication that works with your metal and your hemming machines to make your parts look good.
Conclusion
Sheet metal hemming is an important part of making metal parts. It makes the edges safe, strong, and look good. When you know the different ways to hem parts, you can pick the way that works best for what you need. Whether you use conventional, roll, table, press, or robot hemming, you can make your parts better. You can also make your parts faster and cheaper when you know the newest ways to hem parts. At Premium Rapid & Mold, we use the newest ways to hem parts to make you good metal parts that you need.