Struggling to find the right solution for your industrial needs? Overwhelmed by the number of different types of brackets and materials available? You’re not alone. Many companies have trouble finding high-quality custom sheet metal brackets that meet their specific needs. Here at Premium Rapid & Mold, we get it, and we’re here to help.
Making custom sheet metal brackets is a methodical process that includes everything from selecting the right material to final finishing. The process includes designing the bracket, cutting, forming, joining, and finishing. With the right approach and expertise, you can make high-quality brackets that perfectly suit your needs.
When you need custom sheet metal brackets, you want to make sure they’re of the highest quality and are durable. Whether you’re in the automotive, aerospace, or electronics industry, the right brackets can make a huge difference. Let’s dive into the step-by-step process of designing and manufacturing custom sheet metal brackets so you can understand what it takes to get the perfect bracket for your needs.
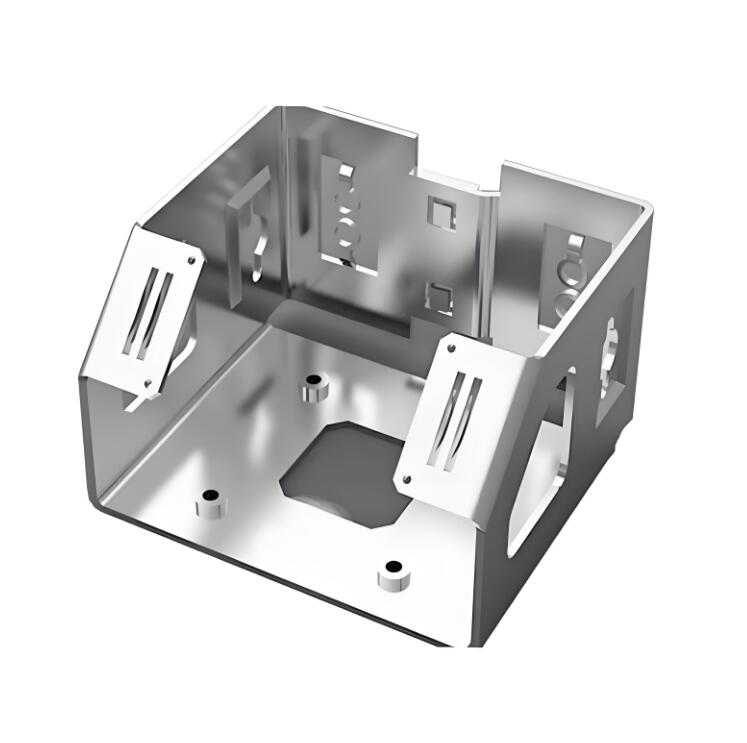
What is a Bracket?
A bracket is that intermediate thing you use to attach one thing to another, like a shelf to a wall. It is the thing that connects and supports two other things. They can be structural, designed to carry loads and support structures, or they can be ornamental and add some visual appeal. Before you get into the nitty-gritty of designing and making a custom bracket, you need to understand the basics of what it is and the different types of brackets that are out there.

Material Selection for Brackets
Choosing the right material is critical for the performance and longevity of your bracket. Common materials include aluminum, stainless steel, mild steel, copper, and brass. Each material has unique properties that make it suitable for different projects.
• Aluminum: This is lightweight and corrosion-resistant, so it’s great for applications in aerospace and marine.
• Stainless Steel: It’s strong and won’t rust, so it’s great for medical and food processing applications.
• Mild Steel: It’s cost-effective and easy to work with, so it’s used in general industrial applications.
• Copper and Brass: These can be used for decorative purposes and are good conductors of electricity.
The material you choose will depend on factors such as strength, corrosion resistance, weight, cost, and the specific needs of your project.
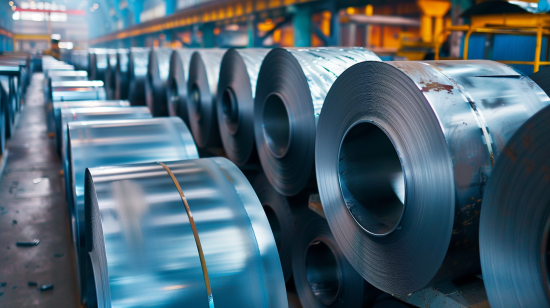
Designing Sheet Metal Brackets
Designing sheet metal brackets starts with CAD software. Here are some key things to consider:
• Angles: L-brackets are typically 90°, but you can go up to 120° or so. Keep in mind that less ductile materials and thicker gauges are harder to bend.
• Bend Preparation: U-brackets and Z-brackets require more preparation to avoid interfering with the brake’s clamping bar. Keep parallel sections short to make it easier to bend.
• Holes for Fasteners: Determine the size and location of holes for screws and other fasteners. If you can’t use nuts, you may need threaded holes.
• Welded Sections: Decide if you need welded sections, and remember that they will add cost.
• Machined Elements: Adding complex features through CNC machining adds cost, but it allows for more design flexibility.
Designing for manufacturability ensures the final product meets both your requirements and is feasible to produce.
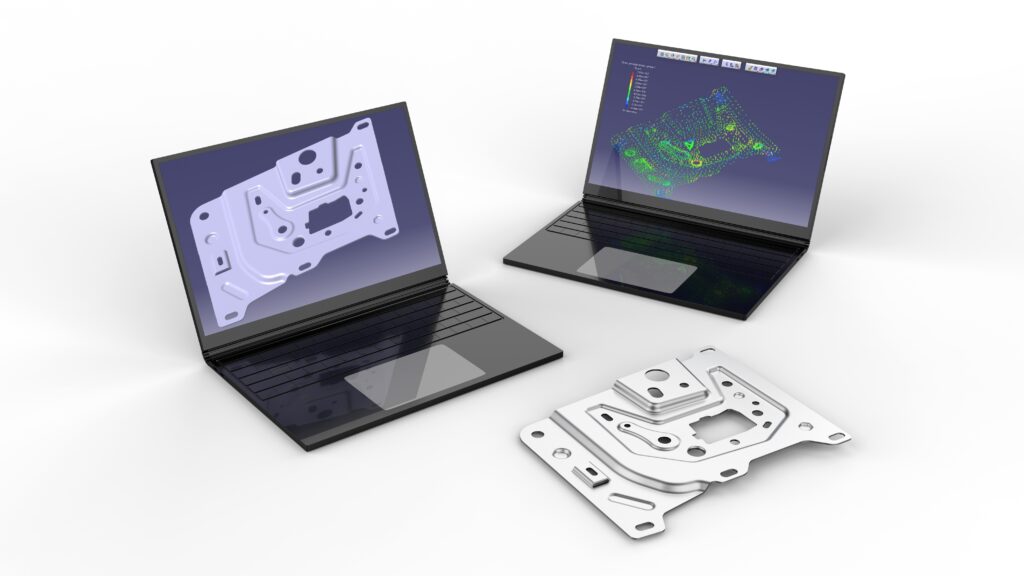
How Brackets Are Made
Sheet metal fabrication is the most efficient way to make brackets. The process includes:
Cutting
You need to cut the sheet metal to size. This can be done with laser cutting or plasma cutting. These methods give you clean edges and accurate dimensions.
• Laser Cutting: A focused beam of light melts, burns, or vaporizes the material. It’s great for intricate designs and gives you high precision with minimal waste. You can get tolerances as tight as ±0.005 inches, so it’s perfect for detailed work.
• Plasma Cutting: An electrically conductive gas cuts through the material. It’s good for thicker materials and can cut through materials up to 1.5 inches thick. Plasma cutting is faster than laser cutting, but it typically is slightly less precise, with tolerances around ±0.02 inches.
Bending
You bend the sheet metal to the angle you want, up to 120°. This is critical for forming the basic shape of the bracket.
• Brake Press: A mechanical or hydraulic press used to bend sheet metal to precise angles. The operator puts the sheet metal in the press, and the machine applies force to make the bend.
• Considerations in Bending: Material thickness, bend radius, and grain direction all affect the quality and precision of the bend. Thicker materials require more force to bend and may not get as tight a radius as thinner materials. The grain direction of the metal can affect the strength and appearance of the bend. Bends perpendicular to the grain are less likely to crack.
Punching
You need holes for screws and fasteners, so you use a punching machine to make them. This ensures you can easily attach the bracket to other parts.
• Punching Machine: A machine that uses a punch and die set to make holes in the sheet metal. The punch presses the metal into the die, cutting out the shape you want.
• Punch Types: There are different types of punches, including round, square, and custom shapes. The size and location of the holes are critical to the bracket’s function and must be very precise.
Welding
To add strength, you might weld gussets or other features onto the bracket. This gives the bracket more structural integrity.
• MIG Welding: Metal Inert Gas (MIG) welding uses a continuous wire feed as the electrode and an inert gas to shield the weld pool. It’s fast and good for welding thin to thick materials.
• TIG Welding: Tungsten Inert Gas (TIG) welding uses a non-consumable tungsten electrode and an inert gas shield. It gives you high-quality, precise welds and is great for critical applications and thin materials.

CNC Machining
You can add complex features and unusual designs through CNC machining. This allows you to precisely customize the part to your needs.
• CNC Milling: A computer-controlled process that uses rotating cutters to remove material and create complex shapes. CNC milling can give you tight tolerances and intricate designs.
• CNC Turning: A process where the material rotates while a cutting tool shapes it. It’s great for making cylindrical parts and detailed features.
Common Types of Brackets
Understanding the different types of brackets helps you choose the right bracket for your application:
L-Bracket
The most common bracket type, L-brackets have an L-shaped profile with a bend along one axis. They are used to mount horizontal objects to vertical surfaces. They are versatile and easy to make. L-brackets are used in shelving, furniture, and various fixtures.
U-Bracket
U-brackets have a U-shaped profile with bends along two axes. They are used to clamp objects or mount parallel surfaces. U-brackets are good for securing things like pipes or keeping components together in a parallel arrangement. They provide strong support in multiple directions.
Z-Bracket
Z-brackets have a Z-shaped profile with bends on opposite sides. They are used to mount offset parallel surfaces. Z-brackets are good for connecting two surfaces that are not aligned with each other. They provide a strong connection and can handle the offset.
Gusset Bracket
Gusset brackets are L-brackets with an additional triangular support for added strength. They are used in applications where you need to support heavy loads. The gusset provides more rigidity and distributes stress, making them good for structural applications.
Corner Bracket
Corner brackets support the corners of structures. They are used in furniture and shelving. They provide stability to joints and help maintain the integrity of the structure. Corner brackets are important for making sure that the connected pieces stay at the right angle and do not move under load.
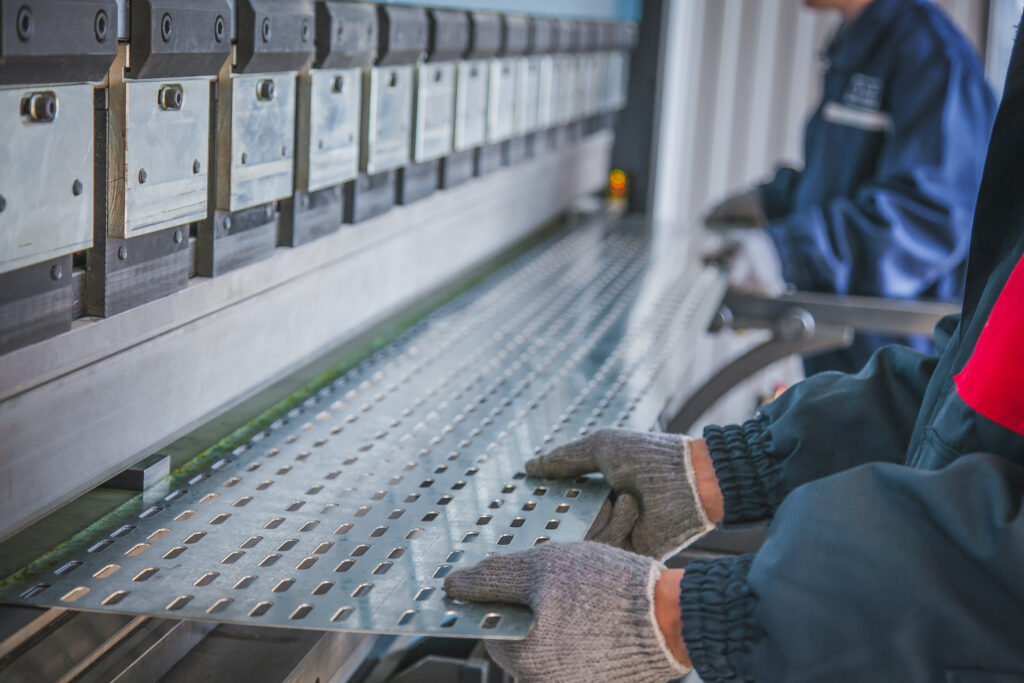
Angle Bracket
Angle brackets are like L-brackets, but they can have different angles besides 90°. This flexibility makes them good for a wide range of applications where you need specific angles. Angle brackets are used in construction, carpentry, and metalworking.
Shelf Bracket
Shelf brackets are made specifically for supporting shelves. They are generally L-shaped and have some decorative elements to make the shelving look nice. Shelf brackets can be plain and functional or fancy and decorative, so they fit the style of the room.
Cantilever Bracket
Cantilever brackets support a load at one end while being fixed at the other. They are commonly used in construction and architectural applications where you need to support something that sticks out. Cantilever brackets need to be strong enough to hold the load without help from the other end.
Hinged Bracket
Hinged brackets allow movement. They are used when the bracket needs to move or swing. Hinged brackets are good for gates, doors, and things that fold. They provide flexibility while still supporting and stabilizing.
Mounting Bracket
Mounting brackets are used to mount devices, such as cameras, sensors, or small machines, to surfaces. They are made to hold equipment securely and stably. Mounting brackets come in different shapes and sizes based on the requirements of the device they are supporting.
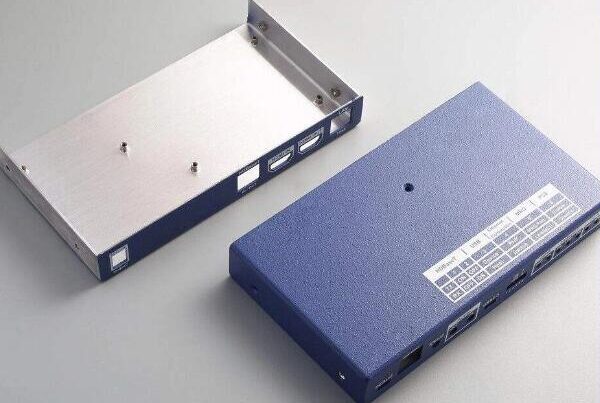
Finishing Options
Finishing improves how the bracket looks and how well it will last. Common ways to finish brackets include:
Powder Coating
Powder coating is a durable, colorful, and protective finish. It’s good for things outside and things that get a lot of wear. The powder is put on with an electric charge and then baked on to make a hard finish. It’s tougher than regular paint.
Anodizing
Anodizing makes metal more resistant to corrosion and lets you add color. It’s commonly used on aluminum brackets. Anodizing is an electrolytic passivation process that makes the natural oxide layer on the metal’s surface thicker. This makes the metal more durable and look better.
Plating
Plating adds a layer of metal to the bracket to protect it and make it look nice. You can do things like zinc, nickel, or chrome plating. Each one has different benefits. Zinc is good for resisting corrosion, nickel looks shiny and wears well, and chrome looks shiny and is decorative.
Bead Blasting
Bead blasting gives you a smooth, matte finish. It’s used for looks and to get the bracket ready for finishing. Bead blasting is when you blast the surface with tiny glass beads at high pressure. This gives you a smooth finish that doesn’t reflect light.
Brushing
Brushing gives you a satin finish by polishing with a grit brush. It’s used for looks and to make the metal look textured. Brushing also gets rid of any imperfections on the surface.
Black Oxide
Black oxide makes the metal more resistant to corrosion and makes it less reflective. It’s good for industrial applications. Black oxide is a chemical treatment that changes the surface of the metal into a layer of black oxide. This gives the metal some protection.
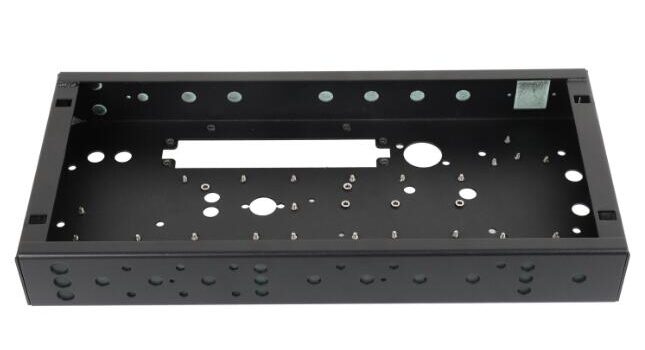
Quality Control
Quality control makes sure the brackets meet the right specifications and standards. This includes:
• Dimensional Checks: You check to make sure all the dimensions are right and fit within the tolerances. This means you measure the brackets at different points in the process to make sure they meet what you want.
• Surface Finish Inspection: You check to make sure the finish looks good and protects the bracket. This check makes sure the brackets look the way you want and the finish protects them.
• Batch Inspections: You check on a regular basis to make sure all the brackets in a batch are the same. This helps you find any mistakes or problems in the process and makes sure the quality is the same.
• Quality Audits: You do a thorough check of everything you do to make sure you don’t have any problems. You look at the whole process to make sure you do everything the right way and that the brackets are the best they can be.

Cost Considerations
Cost is a big deal when you make custom brackets. Here’s what you need to think about:
• Material Costs: Different materials cost different amounts of money. You have to balance how well the material works with how much you want to spend. Sometimes, better materials are more expensive, but they work better and last longer.
• Production Volume: The more brackets you make, the less it costs to make each one. This is because you can make a bunch of brackets at one time and it costs less to do it. The more brackets you order, the less each one will cost.
• Complexity: The more complicated the bracket is, the more it will cost. If you have a simple bracket, it will cost less to make.
• Finishing: Different finishes cost different amounts of money. Powder coating and anodizing cost more than brushing or bead blasting. The finish you pick can make a big difference in the cost.
• Labor and Time: The more custom and detailed the work, the more it will cost. The fancier the design, the more time and money it will take to make it right.
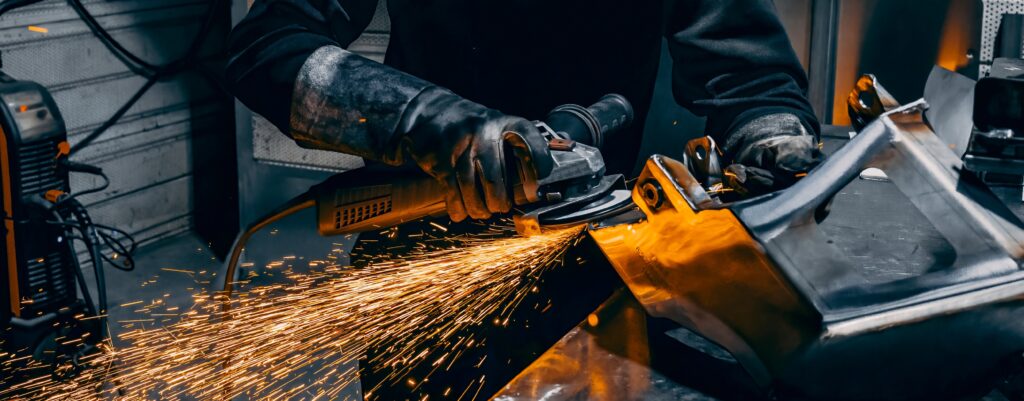
Applications and Uses of Brackets
Brackets are used in many different ways across different industries:
Architectural
Used to connect walls to things like parapets or eaves and hold up architectural stuff. Architectural brackets are often both functional and pretty. They hold up stuff while making the building look cool.
Industrial
Holding up shelves, countertops, and things in machines. Industrial brackets have to be strong and last a long time because they have to hold up heavy stuff and be in places that are tough on them.
Consumer Products
Holding up TVs, putting together furniture, and making things in your house. In consumer products, brackets have to look good and work right.
Automotive and Aerospace
Holding stuff in cars and airplanes and making sure everything stays where it’s supposed to. Brackets in these industries have to be safe and work right.
Electronics
Holding devices and stuff inside them. Electronic brackets have to be perfect and work right so the stuff inside the device works right.
Construction
Supporting buildings, holding up beams, and putting stuff together. Construction brackets have to be tough and hold up a lot of weight and be in places that are hard on them.
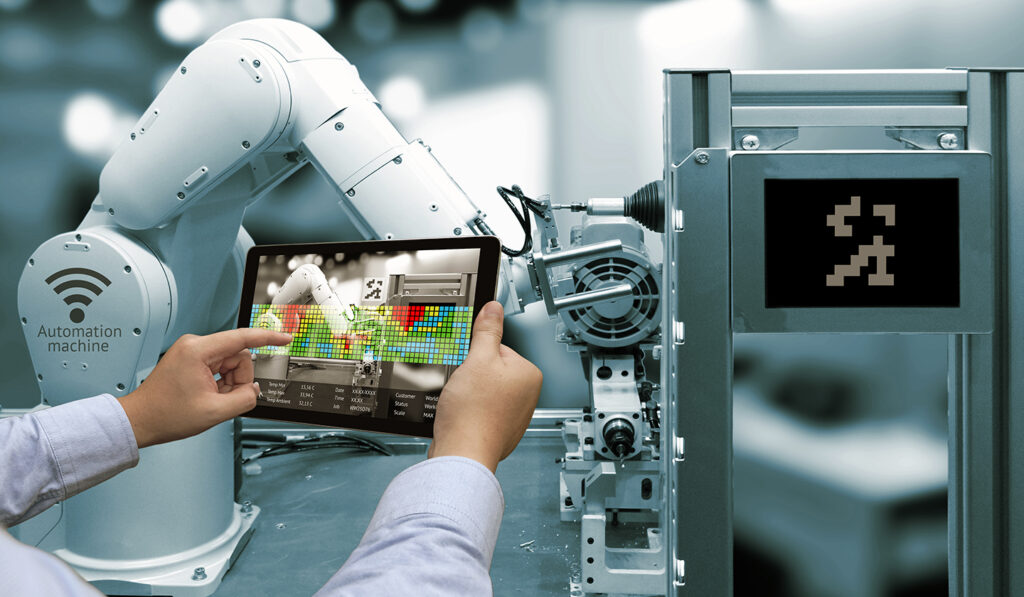
Custom Sheet Metal Brackets From Premium Rapid & Mold
At Premium Rapid & Mold, we are experts at making custom sheet metal brackets. Our team of skilled sheet metal fabricators, laser operators, and programmers ensures we produce the best quality and most precise parts. The top companies in the world trust us to make their custom sheet metal brackets because they know that speed and price don’t matter if the parts aren’t right.
Get a quote today and find out why these companies keep coming back to Premium for their sheet metal parts.
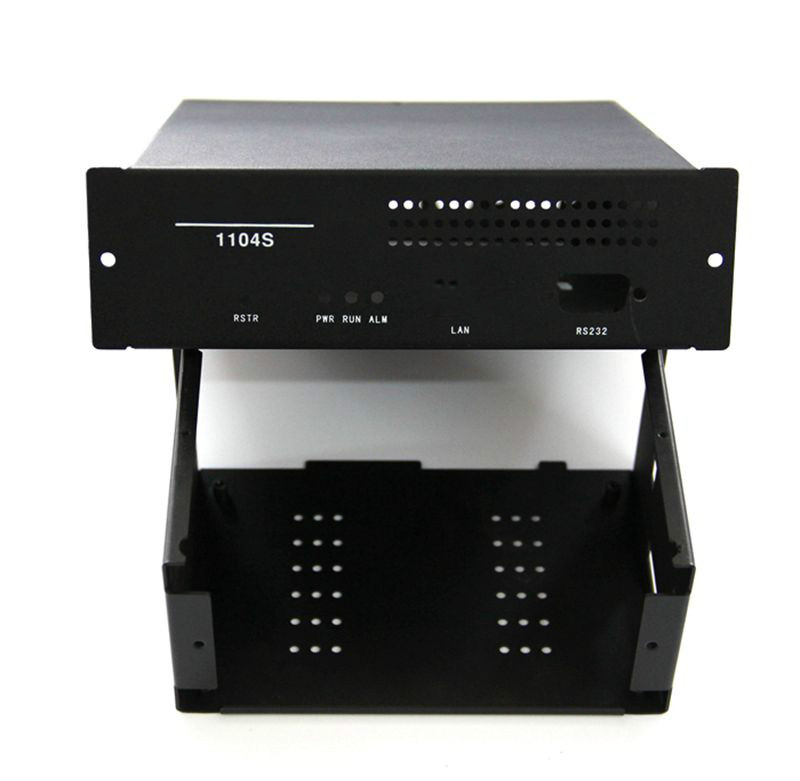
Conclusion
Custom sheet metal brackets are used in many industries and serve a variety of functions while looking awesome. By understanding the design, making, finishing, and quality control processes, you can make sure you get the brackets you need. If you need custom sheet metal brackets made, you should work with an experienced maker like Premium. You’ll get great results that will make your products and processes better. Call us today for all your custom sheet metal needs.