When it comes to prototyping sheet metal parts, the choice of bending technique is critical. Prototypes need to be precise, cost-effective, and quickly produced. Choose the wrong method, and you’ll be delayed, spend more money, and end up with suboptimal parts. That’s where bump forming, also known as bump bending, comes into play. It may be the perfect solution for quickly making sheet metal parts.
Yes, bump forming is often the best choice for sheet metal prototyping. It’s precise, cost-effective, and faster than hard tooling. Ideal for low-volume runs and prototypes, bump forming allows you to avoid the higher costs and delays of specialized equipment. It’s a versatile and efficient process.
When you’re making a new part, you have lots of decisions to make, and choosing the right metal bending technique is crucial. The right choice will impact cost, lead time, and quality. Bump forming, which is typically done on a press brake, creates a series of bends that approximate a curved surface. This can be especially useful for projects where precision and flexibility are important. It’s also beneficial for small- to medium-run production. In this article, we’ll talk about why bump forming might be the best option for your next sheet metal prototyping project.
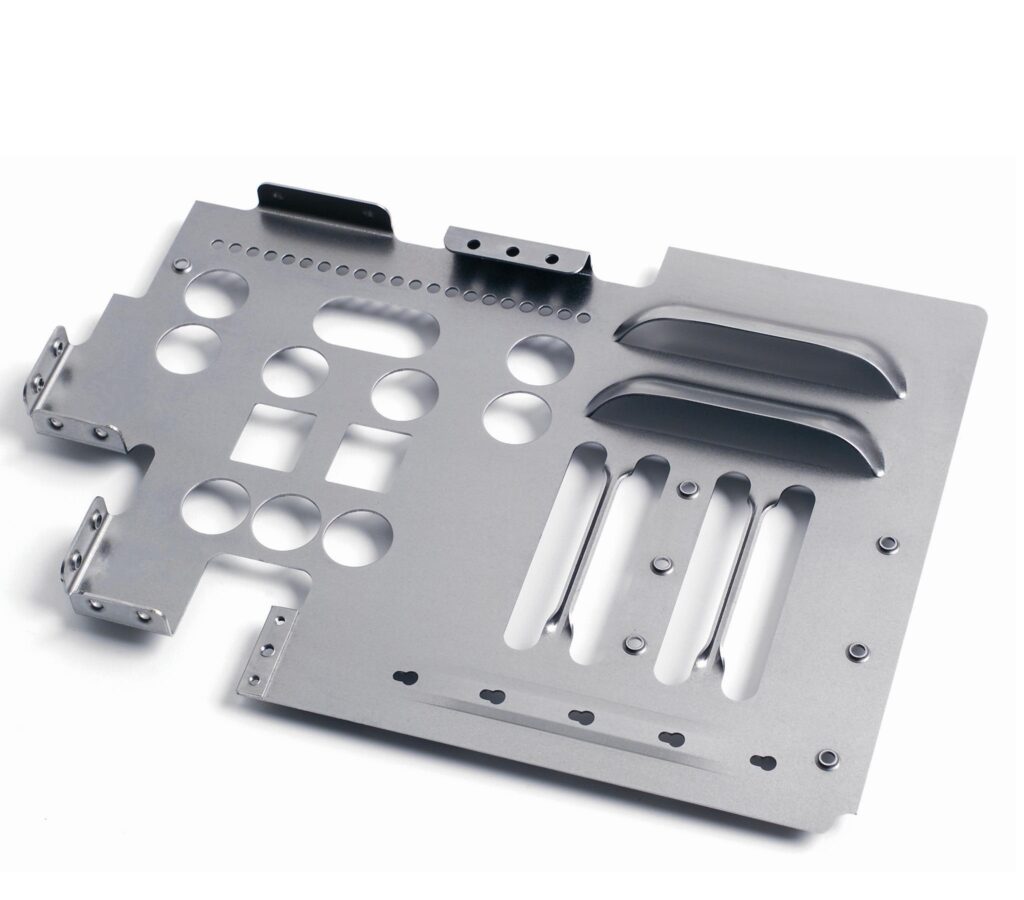
Should You Bump Form or Use Hard Tooling?
When deciding between bump forming and hard tooling, you need to think about what you’re trying to accomplish. Hard tooling is great for production, especially for parts that are cylindrical with large diameters. However, for prototyping or custom, low-volume runs, bump forming is probably the way to go.
The Benefits of Bump Forming
- No Upfront Cost: Unlike hard tooling, which can cost thousands of dollars, bump forming doesn’t require expensive plate rolls. This makes it a cost-effective option, especially for small projects where money is tight. Not having to spend this money upfront can be a big deal, especially for startups or companies on a shoestring budget.
- Quick Turnaround: We can bump form in-house at Premium, so you don’t have to wait for custom tooling to be made and shipped. This means your project can move faster without the delays associated with waiting for specialized equipment. Quick turnaround is crucial in prototyping, where the ability to make changes quickly can lead to faster product development and time-to-market.
- Precision: Especially for smaller diameters where the exact bend is critical. While the process can be slower than plate rolling, it gives you better precision for prototypes and small runs. The ability to get the exact bend you want without the need for special tooling makes bump forming a flexible and adaptable way to make complex shapes and designs.
- Design Flexibility: Bump forming allows for more design flexibility than hard tooling. You can make complex, custom shapes without the constraints of fixed molds or dies. This flexibility is especially useful during the prototyping phase when you’re making a lot of design changes.
- Less Waste: Because bump forming doesn’t require you to make specialized tooling for every project, it reduces material waste. This is great for companies that are trying to be environmentally responsible and reduce their carbon footprint.
- Less Risk: With bump forming, you can try things out without spending a lot of money on retooling. This reduces the risk of the prototyping phase and allows you to experiment and be more innovative.
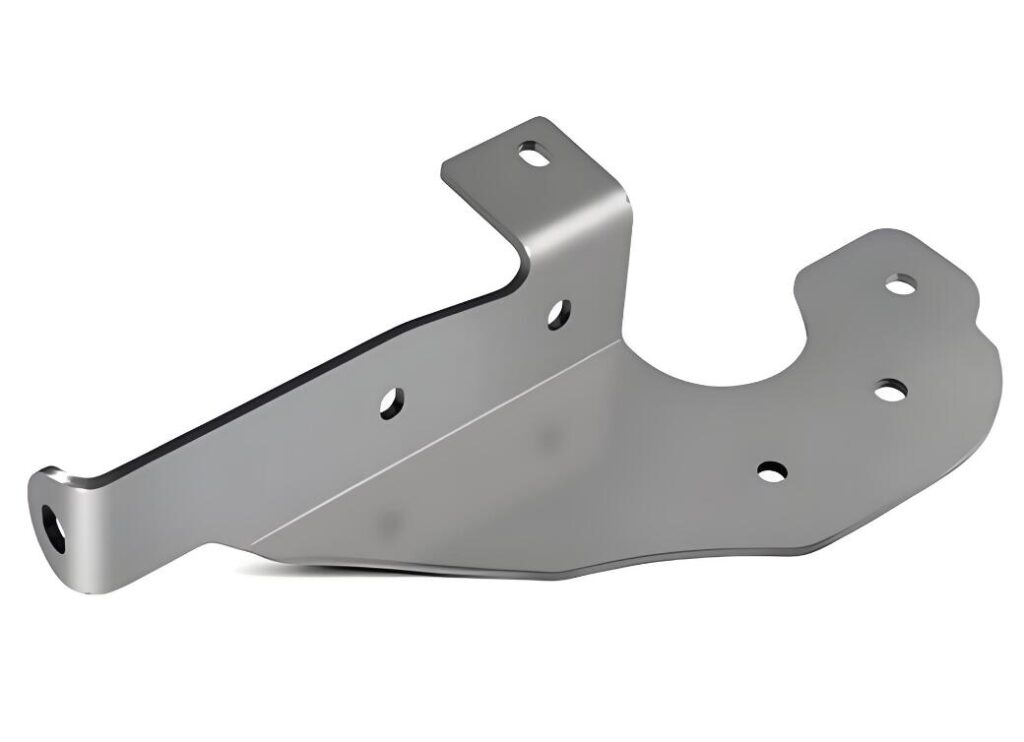
Downsides to Bump Forming
- Experience Required: It takes 5-10 years to get good at bump forming. You need to know how the material behaves, what the machine settings should be, and how to bend the material to get the results you need. It’s a steep learning curve, and finding people who are good at it can be tough.
- Engineering Time: It takes time to make samples to figure out the bend deductions. You may have to go through several iterations to get the right angles and radii for a new design. This process can be time-consuming and can push out project timelines, especially for complex shapes or new materials.
- Scrap and Templates: You have to have templates to check your accuracy, which takes time. You’ll also have a higher initial scrap rate to get the angles right. The trial and error in setting up the part can lead to more material waste and more cost, making it less efficient for very high-precision requirements unless you have a lot of experience.
- Size Limits: Bump forming works best for parts less than 24 inches wide. Once you get bigger than that, it’s harder to maintain a consistent angle and get the same results, which makes it less effective for really big projects.
- Slower: Although bump forming is precise, it’s slower than something like plate rolling, which may not work for projects that have really tight deadlines.
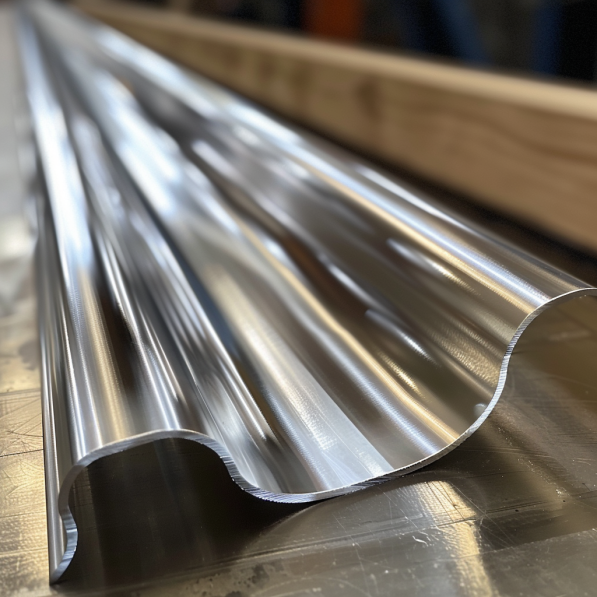
Bump Forming vs. Hard Tooling: Which is Better?
The choice between bump forming and hard tooling depends on what you’re trying to produce.
Hard Tooling
• Large Production Runs: Hard tooling is a must for mass production, especially for parts that are cylindrical with large diameters. It’s the best way to ensure quality over a lot of parts, making it perfect for high-volume manufacturing.
• High Upfront Costs: Hard tooling involves a significant cost upfront to create the dies and molds. This can be a barrier for smaller projects or businesses with limited budgets, but for long production runs, it’s worth it because the cost per part goes down a lot over time.
• Consistent: Once your tooling is set up, you get the same results every time, which is important for mass production. This consistency helps keep your quality up and reduces the risk of defects.
• Durable: Hard tooling is made with tough materials that can stand up to a lot of wear and tear. It’s durable enough to be used over and over again without losing quality.
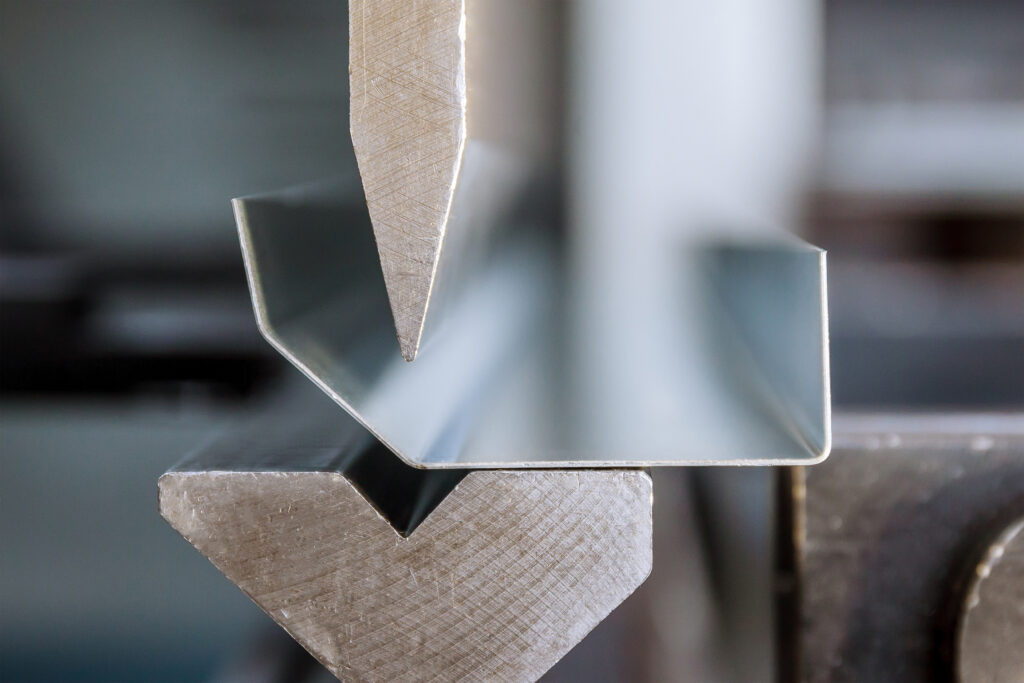
Bump Forming
• Prototyping and Low-Volume Runs: Bump forming is great for prototypes and low-volume runs. It’s more flexible and cost-effective for custom or smaller projects. You can make changes and try new things without spending a ton of money, which is great for the prototyping phase.
• Flexible: Bump forming allows you to make changes and try new things quickly, which is important when you’re developing something new. You can try different things and see what works without the delays of hard tooling.
• Cost-Effective: For smaller runs, you can save a lot of money by not having to make special tooling. You can make high-quality parts without spending a lot of money upfront.
• Adaptable: Bump forming works with many different materials and designs, making it a great choice for a lot of different projects.
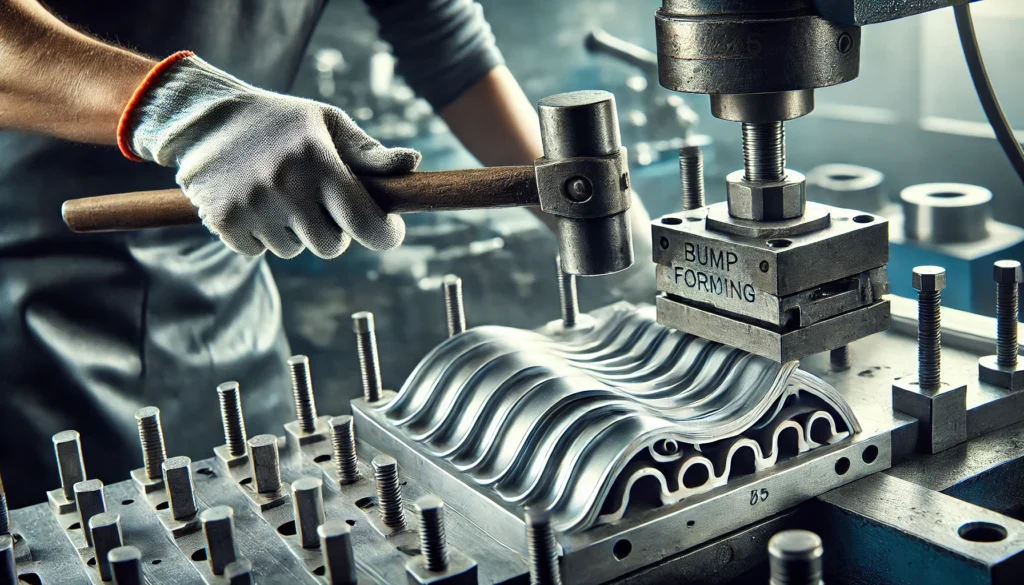
Where Can You Use Bump Forming?
Bump forming is versatile and can be used in a variety of industries and applications, including:
Automotive Body Panels
• Exact Curves: Bump forming is great for creating the exact curves and shapes needed in automotive body panels. This method allows for the creation of complex geometries that are important in modern car designs.
• Prototyping Savings: Car manufacturers can use bump forming to make prototype panels quickly and cheaply, so they can test them thoroughly and get them right before they start making a lot of them.
Aerospace Parts
• Complex Shapes: The aerospace industry needs parts with complex shapes and tight tolerances. Bump forming gives you the precision you need to meet these tough requirements.
• Material Flexibility: Aerospace parts can be made from a lot of different materials, including aluminum and titanium. Bump forming works well with these materials, making it a good choice for aerospace parts.
Custom Electronics Enclosures
• Unique Designs: Electronics often need special enclosures to hold all the sensitive parts. Bump forming lets you make exact, unique enclosures that meet the design and performance specifications you need.
• Prototyping Speed: Electronic companies can use bump forming to get their parts faster so they can get to market sooner.
Medical Device Housings
• Precision and Cleanliness: Medical devices need precise, clean housings. Bump forming can make the complex shapes needed for many medical devices, making sure they meet the high standards for precision and cleanliness.
Architectural Elements
• Custom Metalwork: Bump forming is used to make custom architectural elements like decorative panels and structural supports. This method lets you make intricate designs that make buildings look good.
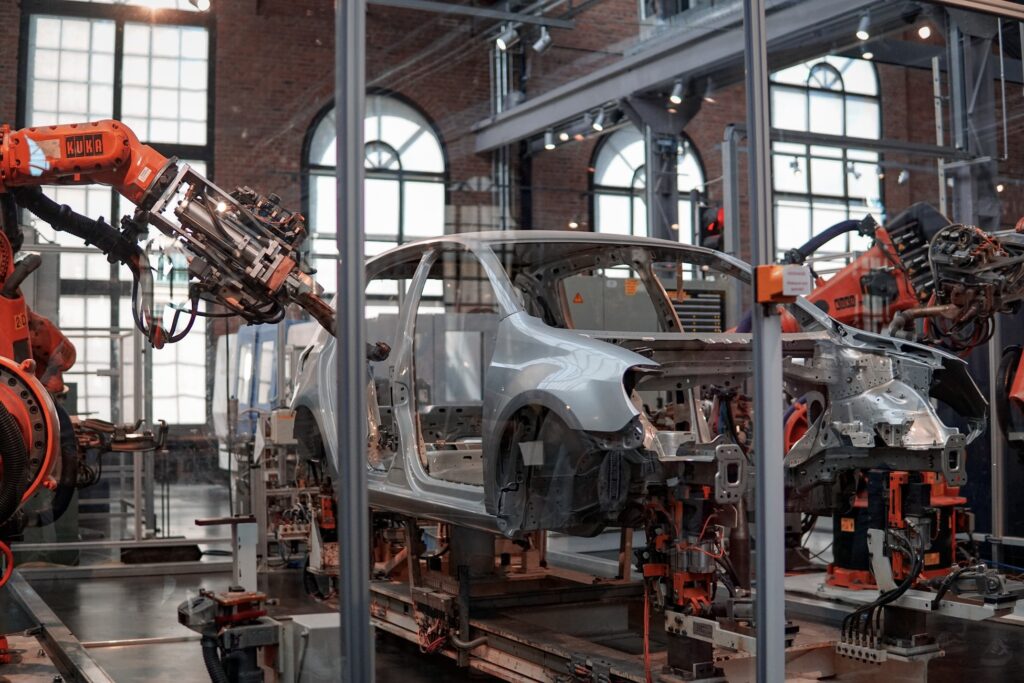
Quality Control in Bump Forming
To maintain high quality in bump forming, you should:
• Use CNC Machinery: This lets you control each bend exactly.
• Check Parts Often: You need to keep checking your parts to make sure they’re right.
• Follow the Rules: You need to follow the rules for each job.
• Use Simulation Software: This software helps you plan and make exact bends, so you don’t mess up and get the right results every time.

Challenges and Solutions
Even though bump forming can be hard, there are ways to make it easier:
- Springback: You can adjust the way you bend the metal to make up for springback.
- Big Parts: The software can help you make exact bends in big parts.
- Skilled People: You need to hire good people who know what they’re doing.
- Tool Wear: You need to check your tools and make sure they’re good all the time.
- Temperature: You need to keep the metal at the right temperature so it bends right every time.
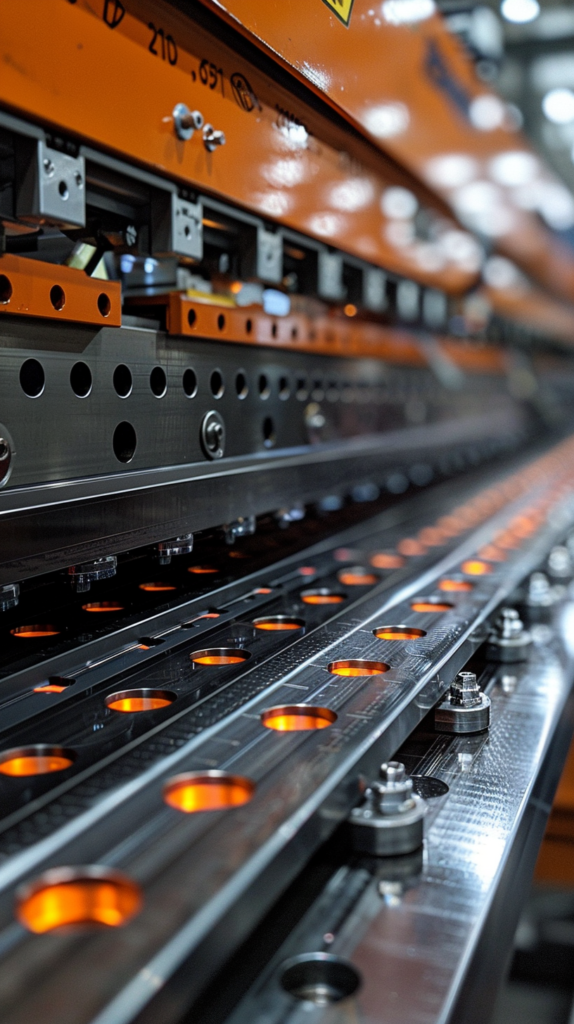
Sheet Metal Bump Forming FAQ
What is bump forming, and how does it differ from hard tooling?
Bump forming uses a series of bends to create cylindrical shapes in sheet metal. It’s cost-effective and efficient for low-volume orders or prototypes. Hard tooling, on the other hand, is required for mass-producing large diameter parts.
What are the benefits of bump forming for sheet metal fabrication?
Bump forming offers no upfront cost, faster turnaround times, and precision for smaller diameters. It’s also more efficient for lower volume orders and helps keep costs down while providing flexibility.
What are the negatives of bump forming in sheet metal fabrication?
Bump forming requires years of experience, engineering time, templates, and extra scrap parts to get the angles right. It’s also the most difficult operation you can perform on a press brake.
Can bump forming be used on large sheet metal parts?
Bump forming is good for parts less than 24 inches wide. But as the length of the bend increases, maintaining a straight, consistent angle is more difficult, making it less useful for large parts.
When is bump forming the best solution for rapid sheet metal fabrication?
Bump forming is great for rapid sheet metal fabrication when you’re doing prototypes or low-volume orders. It’s also perfect when you need precision and want to keep costs low, especially for parts with smaller diameters.
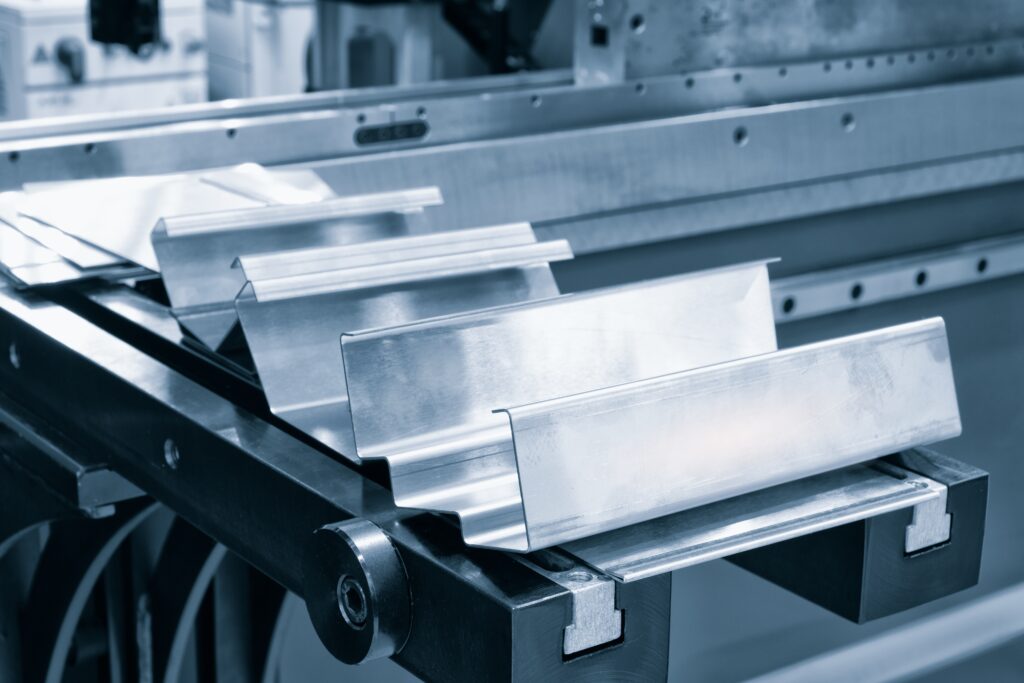
Conclusion
Bump forming is a great way to make sheet metal parts quickly. It’s cheap, accurate, and works well with low-volume orders. While it takes a good operator and some planning, the benefits of bump forming often outweigh the problems, making it the best choice for many applications. By knowing the pros and cons of bump forming and hard tooling, you can make the right choice for your project.