Do you need high-quality, durable, and detailed designs on your sheet metal parts? Silk-screening might be the answer you’re looking for. It’s a process used by many industries to create custom graphics and labels on sheet metal parts that are precise, long-lasting, and cost-effective.
Silk-screening is a precise way to add detailed designs and labels to sheet metal parts. It’s great for industrial applications because it’s tough, resists wear and the elements, and is cost-effective for small and large runs, ensuring consistent quality and high precision.
In this post, I’ll explain how the silk-screening process works, the benefits of silk-screening, and why you should consider silk-screening for your sheet metal parts. Understanding this information will help you make an informed decision and make your products look better.
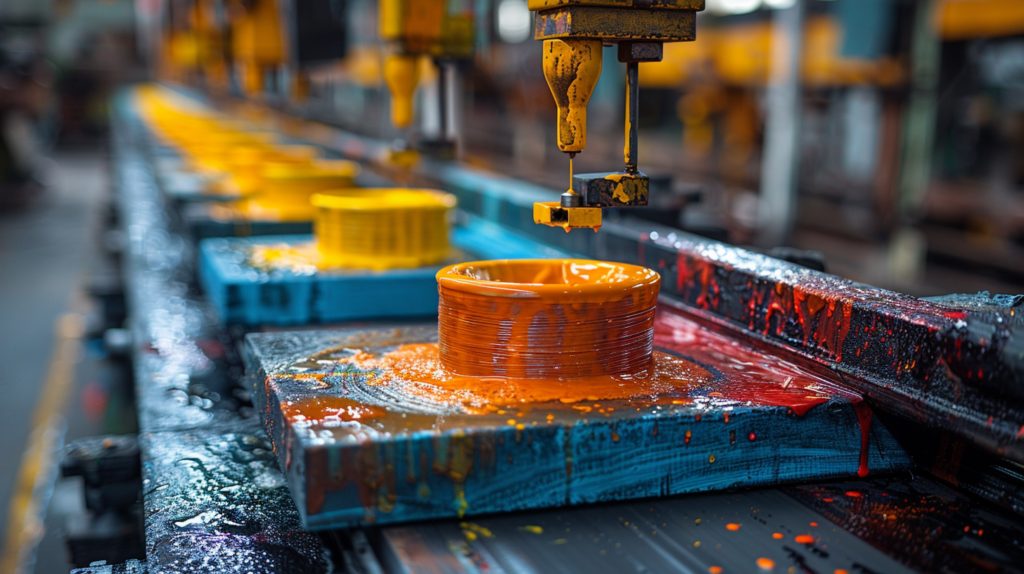
How does Silk-screening work?
Step 1: Prep
The first step in silk-screening is to prep the surface of the sheet metal. This involves cleaning it thoroughly to remove any contaminants that could affect the adhesion of the ink. Next, you create a stencil. This stencil contains the design you want to print on the metal. It’s critical to make sure the stencil is created correctly to match the desired result.
Step 2: Ink
Once the surface is prepped, and the stencil is made, you start applying the ink. You choose the right kind of ink based on the material of the sheet metal and the durability you want the print to have. You place the stencil on top of the metal and apply the ink through the stencil using a squeegee. This step requires accuracy to ensure the ink is evenly distributed and the design is replicated correctly.
Step 3: Cure
After you apply the ink, you need to dry and cure it to make sure it lasts. You can do this in a variety of ways, such as air drying, heat curing, or UV curing, depending on what kind of ink you use. Proper curing ensures the design is resistant to wear, chemicals, and the elements.
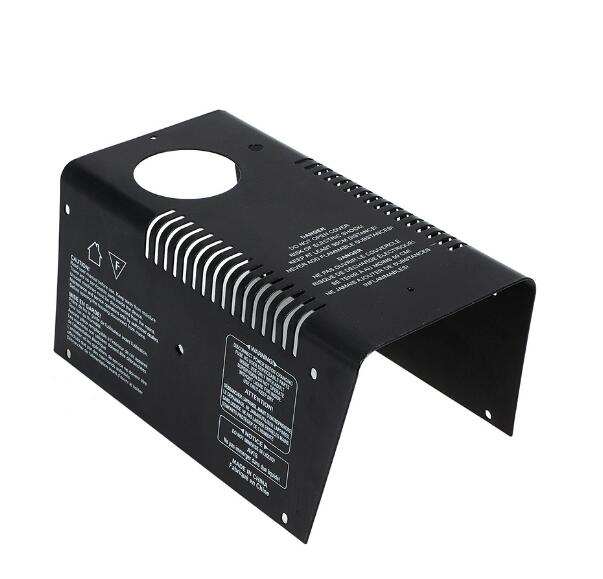
Why Choose Silk-Screening for Sheet Metal Parts?
Precision and Detail
Silk-screening is known for its ability to create highly detailed and precise designs. This is critical for applications that require clear and accurate labeling, such as industrial machinery and electronic enclosures. The high precision of silk-screening ensures that even the most intricate designs can be replicated accurately.
Durability
One of the great things about silk-screening is that it’s durable. The inks used in the process are made to withstand tough conditions, including exposure to chemicals and extreme temperatures. This makes silk-screening perfect for industrial applications where longevity and resistance to wear are important. For example, labels on machinery need to be readable even when they’re constantly being touched and exposed to all kinds of substances.
Cost-Effective
Silk-screening is cost-effective for both small and large runs. The initial setup costs are low, and you can scale the process to do different batch sizes without a huge jump in cost. This makes it a great choice for businesses that need to make high-quality printed sheet metal parts efficiently.
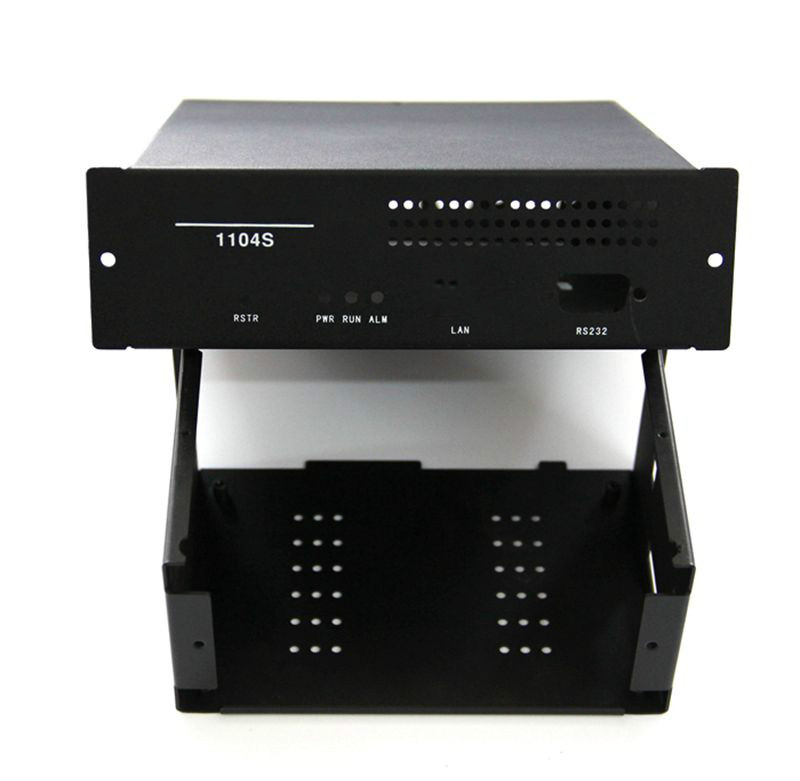
Applications of Silk-Screening on Sheet Metal
Industrial Applications
Silk-screening is commonly used in industry to label and brand machines and equipment. It provides a durable way to mark safety instructions and operating instructions so they remain visible and readable as long as the equipment is in use.
Consumer Electronics
Silk-screening is also used extensively in the consumer electronics industry. It allows you to create decorative elements and branding on the outsides of electronics, as well as user interfaces and control panels. The precision of silk-screening ensures that these components meet the high aesthetic standards required for consumer products.
Automotive Industry
In the automotive sector, silk-screening is used to put custom graphics and labels on various parts. This can enhance the look of the parts and provide practical benefits, such as clear labels for controls and indicators. The durability of silk-screening ensures that these graphics stay put in the demanding environment of the automobile.
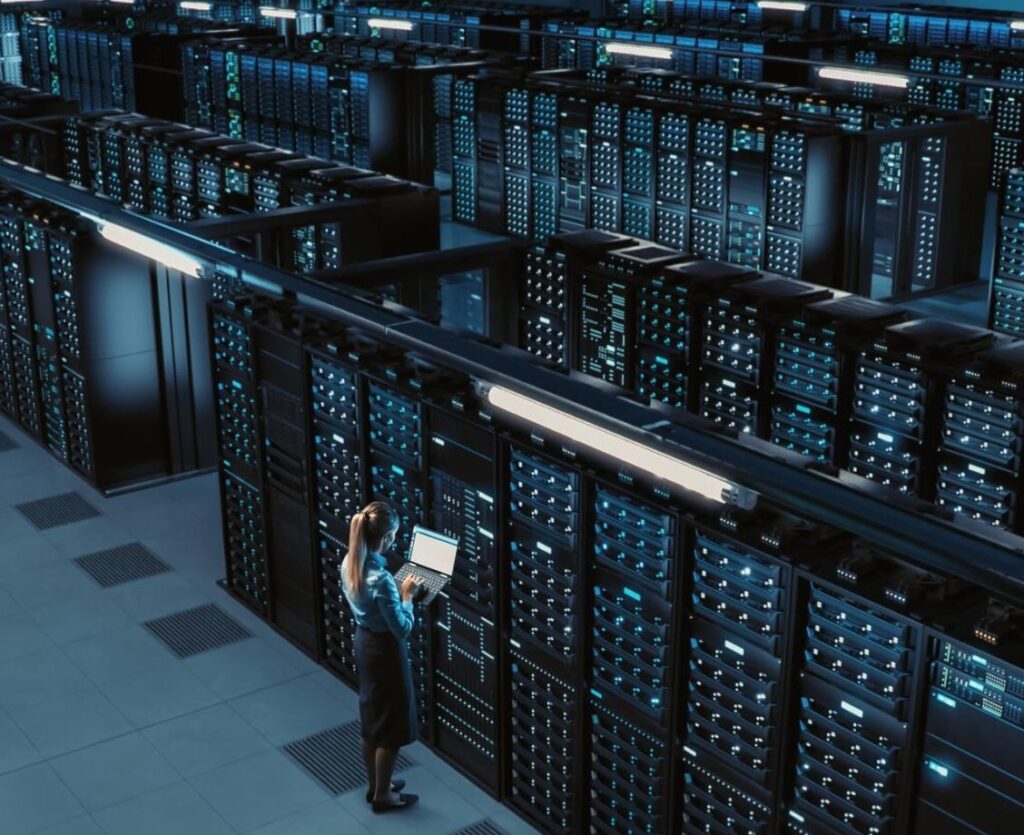
Specialized Techniques in Silk-Screening
Multi-Color Printing
Silk-screening isn’t limited to single-color designs. You can use multi-color printing techniques to create complex, vibrant graphics. This involves putting multiple layers of ink on the part, each a different color, in a precise order. You use alignment methods to make sure the colors line up perfectly, which results in a sharp, cohesive design.
Textured and Matte Finishes
You can use specialized inks and techniques to create textured or matte finishes on sheet metal parts. These finishes don’t just look good; they also have practical uses, such as reducing glare or making it easier to hold onto the part. Applications where these finishes are preferred include control panels and handles.
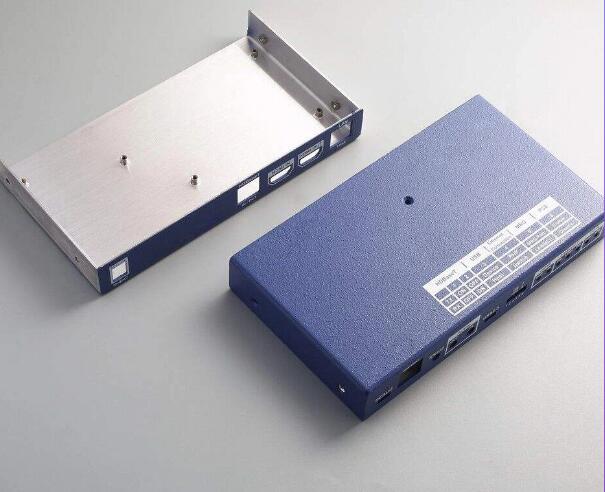
Quality Control in Silk-Screening
Maintaining Consistency
To produce high-quality parts, you have to maintain consistency in silk-screening. Techniques such as using automated ink application and controlled curing processes help ensure every part meets the standards you set. You check and inspect parts throughout the process to catch and correct any problems.
Common Problems and Solutions
You can solve common problems in silk-screening, like smudging or misalignment, by properly setting up and maintaining your equipment. If you make sure your stencil is in the right place and you put the ink on the part evenly, you can avoid these problems. Regularly cleaning and calibrating your silk-screening equipment also helps maintain quality.
Advanced Quality Control
Advanced quality control practices, such as using automated systems to inspect quality and implementing statistical process control (SPC), can further improve the consistency and quality of silk-screened parts. These practices let you monitor and adjust how you’re producing parts in real time, which reduces the chance of defects and ensures every part meets your specifications.
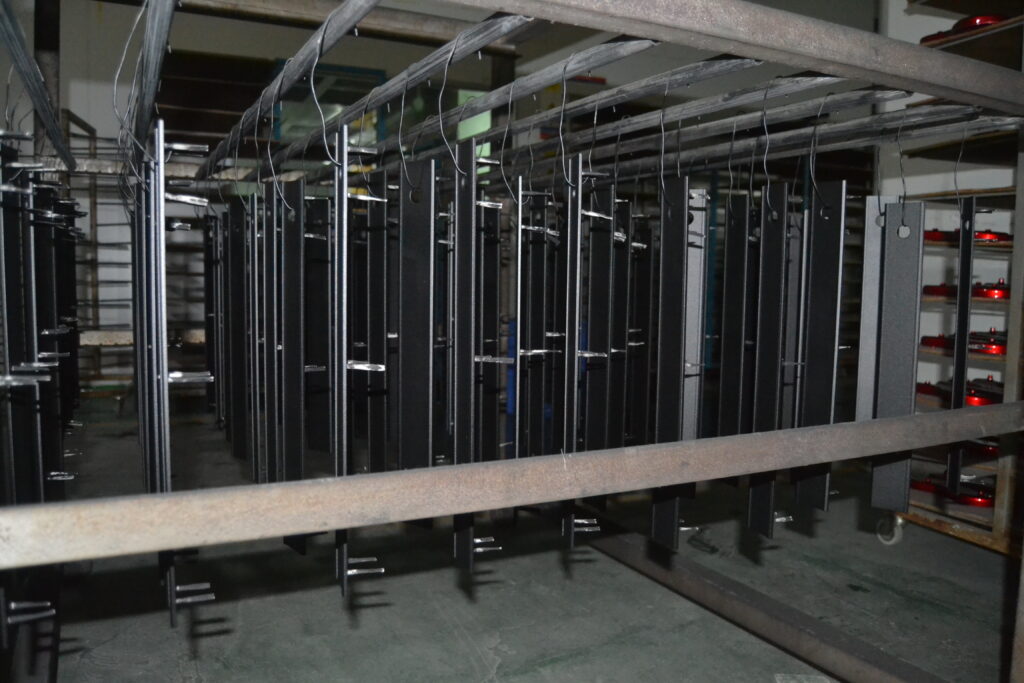
Combining Silk-Screening with Other Surface Treatments
Powder Coating
You can use silk-screening with powder coating to make sheet metal parts look good and last a long time. After you put on a durable powder coat, you can use silk-screening to add detailed graphics and labels. This combination is handy for outdoor applications where you need parts to look good and stand up to the weather.
Painting
Using silk-screening with painting can make sheet metal parts look great and be durable. Painting gives you a smooth, even base coat, and silk-screening adds the detailed designs and labels. This combination is especially useful in consumer electronics and automotive applications where looks and branding are important.
Conclusion
Silk-screening is a great way to put detailed designs on sheet metal parts that are precise, durable, and cost-effective. Whether you need detailed designs for industrial equipment, consumer electronics, or car parts, silk-screening is a great way to get the job done quickly and efficiently. By understanding how silk-screening works, what its benefits are, and where to use it, you can make the right decisions to make your products look better. Embrace silk-screening to get better results and make more of the parts you need.