Do you struggle to understand how sheet metal forming works? Are you in the automotive or aerospace industry and need to know how your parts are made? Maybe you’re a supply chain manager and want a reliable manufacturing process. Understanding sheet metal forming can help you make better decisions and improve your product design and manufacturing efficiency.
Sheet metal forming is a manufacturing process that transforms flat metal sheets into parts and components through various techniques like bending, shearing, punching, and hydroforming. This process is critical in many industries because it’s versatile, cost-effective, and produces durable parts.
Stick around as we dive deep into the world of sheet metal forming. We’ll cover the processes, applications, and benefits. By the end, you’ll have a good understanding of why this method is the go-to for many manufacturers. Whether you’re sourcing parts or designing new products, this information will help you make better decisions.
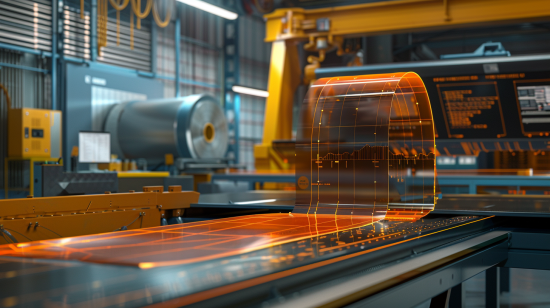
Overview of Sheet Metal Forming
Sheet metal forming is a basic manufacturing process that changes flat metal sheets into different parts and components. This process is used in many different industries because it can make complex shapes with high precision and strength.
Why It’s Important in Many Different Industries
Sheet metal forming is used in many industries. In the automotive industry, it’s used for body panels and engine components. Aerospace uses it to make lightweight, high-strength parts. Consumer electronics, household appliances, and construction also use sheet metal forming because it’s flexible and efficient.
Basic Concept and Objectives
At its core, sheet metal forming changes flat sheets of metal into finished products. The main things you want to do when you form sheet metal are to get the right shape and size and to maintain the strength of the material. Sheet metal forming takes advantage of the fact that most metals are malleable and ductile. That means you can change their shape and still get a part that meets your design and functional requirements.
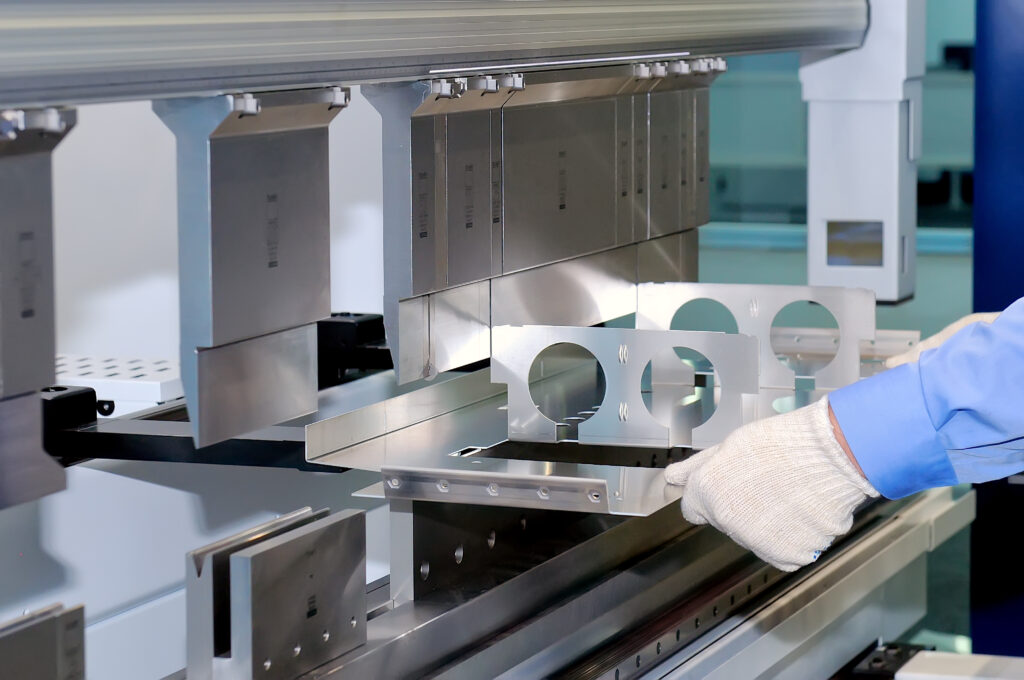
What Is Sheet Metal Forming?
Definition of Sheet Metal Forming
Sheet metal forming, also known as sheet metal fabrication, refers to the process of manipulating flat metal sheets to make parts and components. This is done through various operations such as bending, punching, shearing, and hydroforming.
Explanation of Sheet Metal Fabrication
Sheet metal fabrication is the overall process that includes forming, cutting, and assembling metal sheets into final products. It involves a series of operations that shape and refine the metal to meet specific requirements. The versatility of sheet metal fabrication makes it suitable for a wide variety of products across many different industries.
Common Applications
- Automotive: Body panels, engine parts, exhaust systems
- Aerospace: Fuselages, wings, structural components
- Consumer Goods: Electronic enclosures, brackets, casings
- Household Appliances: Washing machine drums, refrigerator panels, oven parts
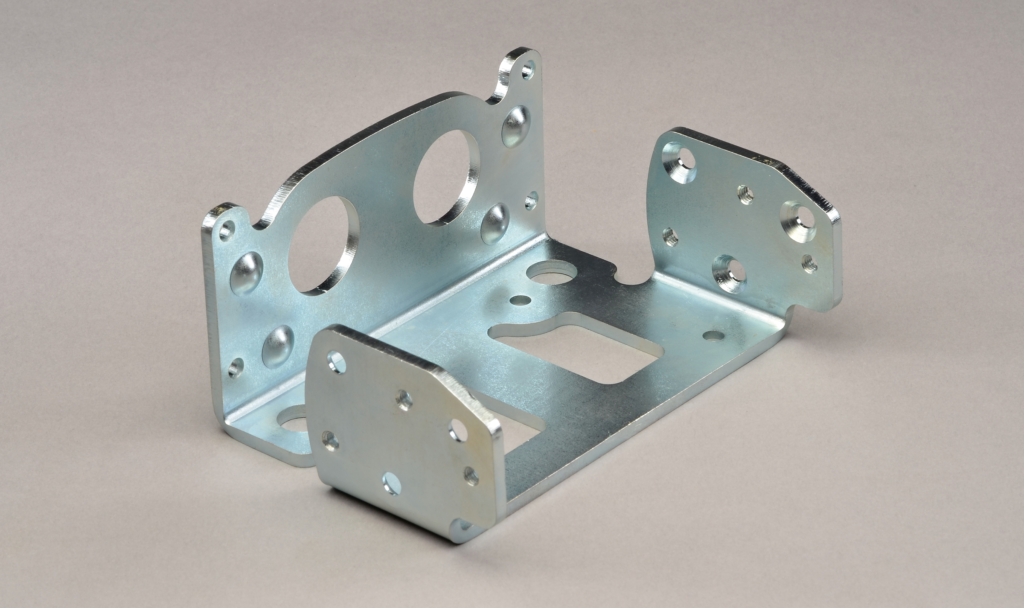
What Is the Purpose of Sheet Metal Forming?
Creation of Parts from Thin Sheet Metal
The main reason sheet metal forming exists is to make parts from thin metal sheets. You need sheet metal forming to make parts that have to be a certain shape and size. The shape and size of the parts are important to the way the product is designed and works.
Versatility of the Process
Sheet metal forming is super versatile. You can make a lot of different shapes, sizes, and types of metal parts with it. You can make simple parts. You can also make super complex parts. That’s why so many manufacturers love using sheet metal forming. It lets them make all sorts of different parts for all kinds of products.
Advantages
• Strength: The parts you make with sheet metal forming are strong. They’re great for lots of different things.
• Malleability: You can bend and shape metal without breaking it. That’s how you make cool shapes.
• Cost: Sheet metal forming is cheaper than other ways of making metal parts. It’s especially good for making a lot of parts at one time.
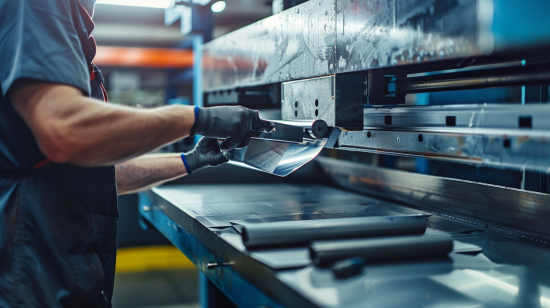
How Does Sheet Metal Forming Work?
Processes for Turning Flat Sheets into Parts
Sheet metal forming uses several processes to shape flat sheets into parts:
• Bending: Making angles and curves
• Shearing: Cutting along straight lines
• Punching: Making holes and shapes
• Hydroforming: Using high-pressure fluid to make complex shapes
Setting Up Tools for the Design
The tools and machines used in sheet metal forming are set up based on what the design calls for. That includes selecting the right dies, punches, and forming tools to make the shapes and sizes you need. Setting up the tools correctly is important to ensure that the part comes out right every time.
What Happens After Forming the Part?
After you’ve done the main forming process, you do a few other things to make the part better:
• Deburring: Getting rid of sharp edges and burrs
• Surface treatments: Adding coatings or finishes for protection and looks
• Welding: Joining multiple parts together to make complicated assemblies
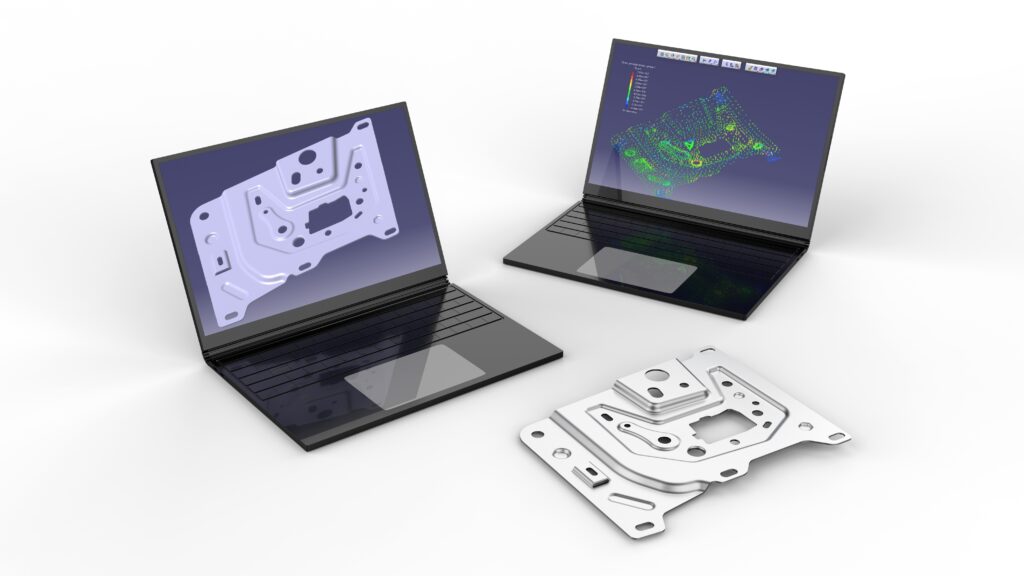
Suitable Metal Thickness for Sheet Metal Forming
General Guideline: 0.6 mm to 6.35 mm
Typically, sheet metal forming is good for metal thicknesses between 0.6 mm and 6.35 mm. This range covers a whole bunch of applications, from thin, lightweight parts to thicker, stronger pieces.
Variance Depending on Metal Type, Manufacturer, and Part Complexity
The right thickness for sheet metal forming can depend on the type of metal, the capabilities of the manufacturer, and how hard the parts are to make. For example, softer metals like aluminum can handle a little more thickness variance, while harder metals like stainless steel might need you to be right on the money with the thickness.

Equipment Used in Sheet Metal Forming
Punches and Dies
• For Cutting and Making Holes with Specific Shapes Punches and dies are important tools in sheet metal forming. They’re used to cut and make holes in the metal. You can make specific shapes and holes in the metal with punches and dies. This allows you to make patterns that are accurate and consistent.
Bending Machines
• For Bending Metal Bending machines, like press brakes, are used to bend sheet metal. These machines press the sheet metal, bending it along a straight line to make the shape you want.
Rollers
• For Making Sheet Metal into Cones and Cylinders Rollers are used to make sheet metal into cones and cylinders. This process is used to make pipes, tubes, and other round shapes.
Shearing Tools
• For Cutting Straight Lines Shearing tools are used to cut sheet metal along straight lines. This process involves applying force to the metal to make it break along the cut line. Shearing is used to trim edges and cut sheet metal into smaller pieces.
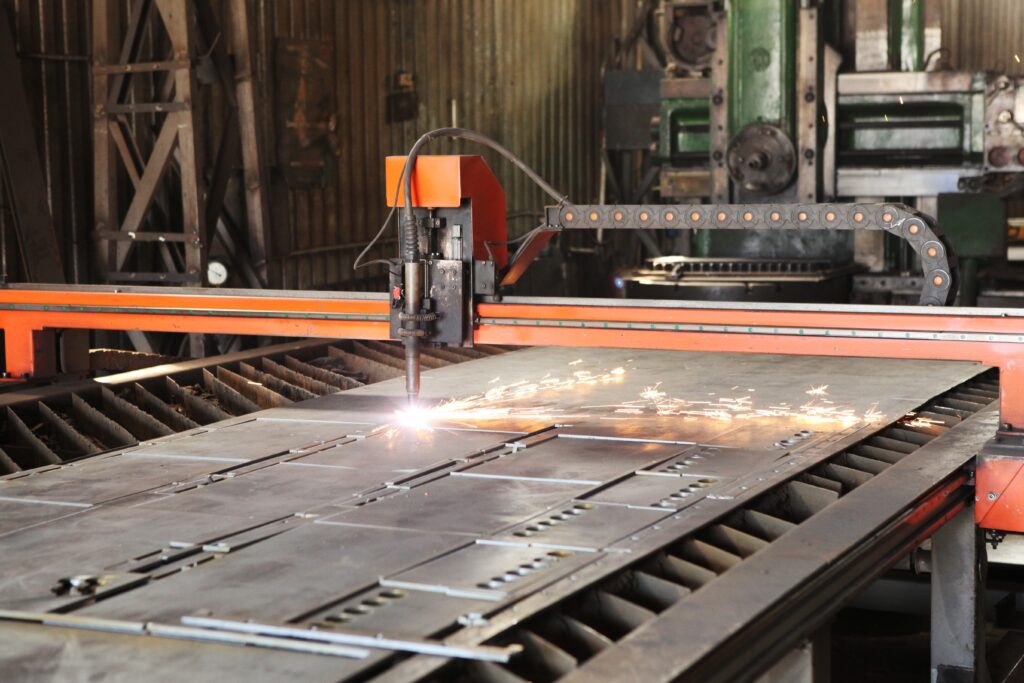
Applications
Automotive
- Automotive
- Sheet metal forming is critical in the automotive industry. It’s used to make car bodies, engine parts, and exhaust systems. The process creates parts that have to be super precise and strong, which is necessary for car parts. For example, sheet metal forming is used to stamp and form car panels. These components are strong and look good.
- Aerospace
- In the aerospace industry, parts need to be lightweight and strong. Sheet metal forming does this by making parts that meet strict safety and performance requirements. Aluminum fuselages and wing structures are examples of parts made with sheet metal forming. They’re strong and light, which is great for flying.
- Electronics
- Sheet metal forming is used a lot in the electronics industry to make cases, chassis, and brackets. These parts protect sensitive electronics and help manage heat. For example, sheet metal forming is used to make the cases for smartphones and computers. These cases are tough, look good, and help the electronics stay cool.
- Construction
- The construction industry uses sheet metal forming a ton. It’s used to make building structures, roofing, and HVAC systems. The parts are strong and can handle all kinds of weather. For example, sheet metal forming is used to make metal roofing and structural beams. These parts last and can handle the weather.
- Consumer Products
- From appliances to furniture to lights, sheet metal forming is used a lot in consumer goods. The process helps make parts that look good and work well. Stainless steel kitchen appliances are a great example. They look good, are super tough, and work great.
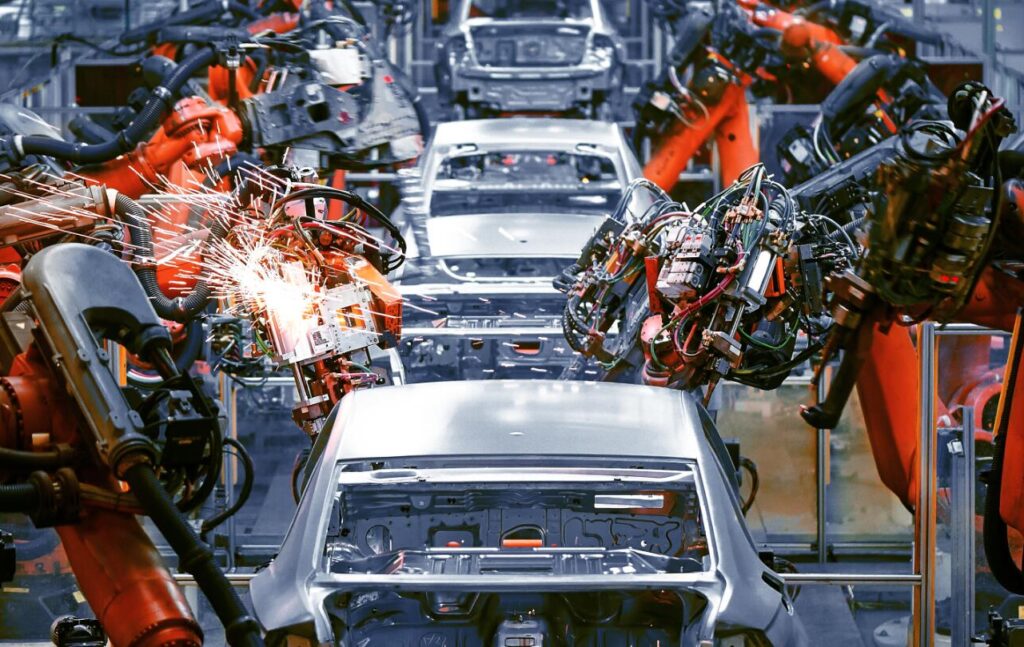
Materials Used in Sheet Metal Forming
Aluminum
- Properties: Lightweight, corrosion-resistant
- Applications: Commonly used in the aerospace and automotive industries due to its excellent strength-to-weight ratio.
- Example: Aluminum panels for aircraft
Stainless Steel
- Properties: High strength, corrosion-resistant
- Applications: Widely used in medical devices and kitchen appliances for its durability and resistance to rust.
- Example: Stainless steel surgical instruments
Mild Steel
- Properties: Cost-effective, good machinability
- Applications: Frequently used in construction and machinery for its strength and ease of fabrication.
- Example: Structural beams and frames
Copper
- Properties: Excellent electrical conductivity
- Applications: Used in electrical and plumbing applications due to its superior conductivity and ease of forming.
- Example: Copper wiring and plumbing pipes
Galvanized Steel
- Properties: High durability, corrosion resistance, low cost
- Applications: Commonly used in roofing, air conditioning, refrigeration, and industrial machinery for its protective zinc coating.
- Example: Roofing sheets
Brass
- Properties: Good corrosion resistance, excellent workability
- Applications: Often used in decorative applications, plumbing fixtures, and electrical components.
- Example: Brass fittings and hardware
Titanium
- Properties: High strength-to-weight ratio, excellent corrosion resistance
- Applications: Used in aerospace, medical implants, and high-performance automotive parts due to its strength and lightweight properties.
- Example: Aircraft components and medical implants
Nickel Alloys
- Properties: High-temperature resistance, excellent corrosion resistance
- Applications: Commonly used in aerospace, chemical processing, and marine applications where durability in harsh environments is essential.
- Example: Turbine blades and chemical processing equipment
Carbon Steel
- Properties: High strength, cost-effective
- Applications: Used in construction, automotive, and heavy machinery for its durability and ease of fabrication.
- Example: Automotive body parts and construction girders
Zinc
- Properties: Corrosion resistance, easy to form
- Applications: Used for galvanizing steel and making die-cast components.
- Example: Galvanized steel coatings and small die-cast parts
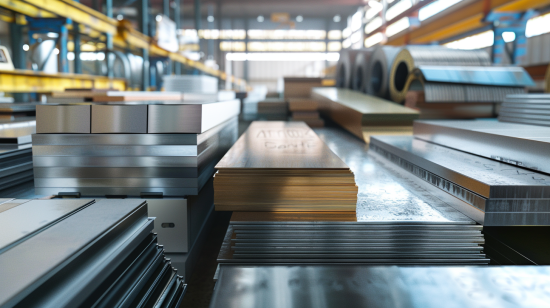
Benefits
Versatility in Design
Sheet metal forming lets you make all kinds of shapes and parts. You can make simple parts, and you can make super complex parts. This gives you the flexibility to make whatever you need.
High Strength and Durability
Parts made with sheet metal forming are strong and can handle a lot. That’s why people make car parts and airplane parts with this process. The parts last a long time and work well.
Cost-Effectiveness
Sheet metal forming is a great way to make a lot of parts. It’s cheaper to make a lot of parts at one time, which is why people use this process to make a lot of parts.
Customization
You can make whatever you want with sheet metal forming. You can pick the material you want and the design you want. That’s why people make custom parts with this process.
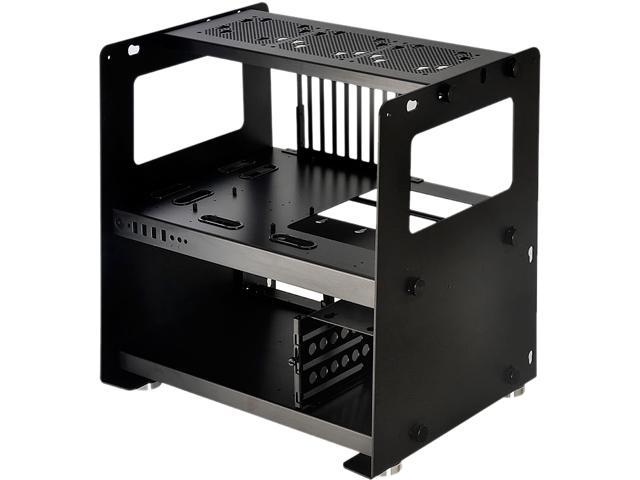
Conclusion
Sheet metal forming is a versatile, cost-effective, and widely used manufacturing process. It creates durable parts for various industries, including automotive, aerospace, construction, medical equipment, and household appliances. Understanding the processes, materials, and applications of sheet metal forming can help you make informed decisions and improve your product design and manufacturing efficiency.