Your project's been moving smoothly. The design looks perfect, the deadline’s looming, and then it hits—a sudden bottleneck in production. Sounds familiar? Maybe the tolerances were off. Perhaps the material wasn’t feasible, or worse, the assembly doesn't work! The frustrations pile up, deadlines stretch, and costs skyrocket.
Why does this happen? Often, it's because designs don't consider manufacturability early enough, leading to a pile-up of production issues. Ignoring this aspect can easily turn a promising design into a costly headache. You don't want to end up in a situation where design decisions cause delays, extra expenses, and unhappy clients.
That’s where Design for Manufacturability (DFM) comes in. With DFM, we bridge the gap between dreamy design concepts and down-to-earth production realities, ensuring smooth execution from blueprint to fabrication. Let's dive into how DFM can save you time, money, and quite frankly, your sanity.
Design for Manufacturability (DFM) bridges the gap between design and sheet metal fabrication by ensuring that designs are optimized for efficient, cost-effective production right from the start. It aligns design with manufacturing processes, materials, and tolerances, reducing defects, saving time, and improving overall product quality.
Curious to know more? Hang tight; we're about to dive deep into this magical process that could transform the way your projects come to life.
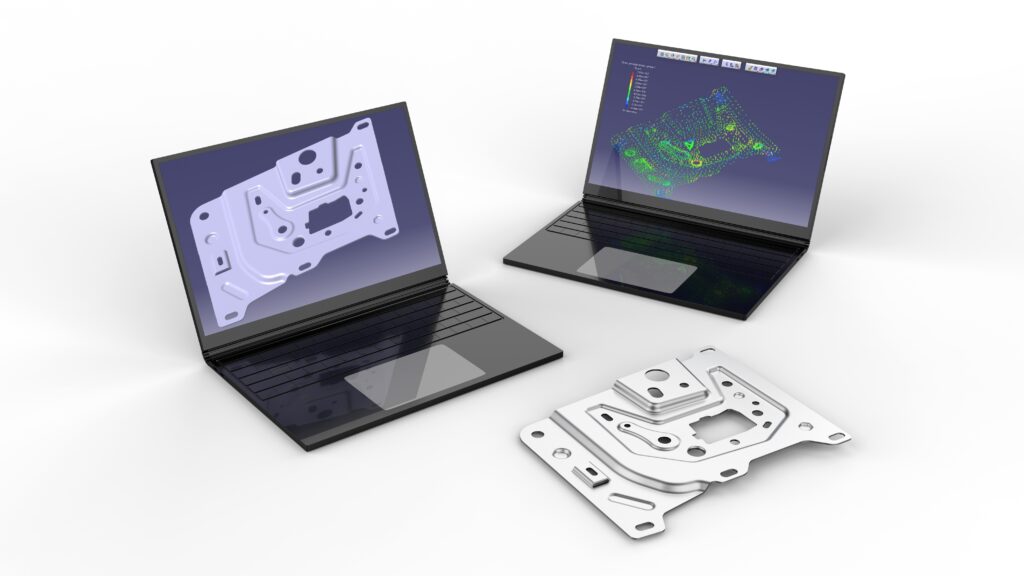
What is Design for Manufacturability (DFM)?
At its core, DFM is the process of creating a product design that is easy to manufacture. It’s not just about how something looks or how it functions. It’s about making sure your design is set up in a way that when you actually go to produce it, everything works the way it’s supposed to work.
Think about it. What good is an awesome design if you can’t produce it without pulling your hair out? DFM is about making sure your ideas not only look great on paper but also work incredibly well in the real world. If that’s the case, why isn’t everybody doing it? I don’t know.
Early Involvement: The Secret to Success?
When do you get your manufacturer involved? Most people get them involved after they finish the design. That’s not the real secret. The real secret is to get them involved early. If you involve us during the design phase, we can help you tweak your project for manufacturability. Whether it’s selecting the right material, adjusting features so they’re easier to make or making sure your tolerances are right where they need to be, early involvement can help you avoid surprises later.
Do you want to catch issues before they hit you or deal with them when the clock is running? You know the answer to that.
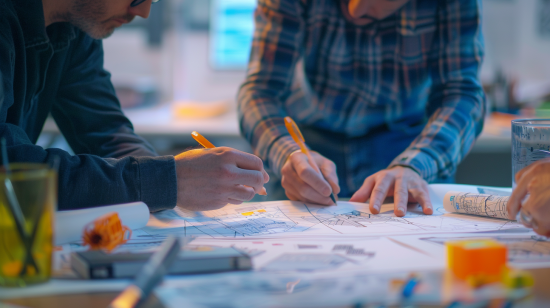
How Does Material Selection Impact the Process?
The material can make or break your project. Selecting the right material based on your product’s application and how you’re going to make it is critical. Different materials have different properties that impact how they behave during the fabrication process. That could be bending radius, how they react to heat during a laser cut or how they respond to a surface treatment like powder coating.
Are you sure you have the right material for your design? You should. We know which materials work best for specific applications, and that knowledge can help you avoid headaches during production.
Tolerance Management: Is Precision Always Necessary?
Let’s talk about tolerances for a second. Everybody loves precision, right? However, specifying ultra-tight tolerances where they’re not needed can drive up costs and time. DFM helps you balance this by making sure your tolerances are realistic for manufacturing—tight enough to make sure it works but not so tight that it makes manufacturing unnecessarily complicated and expensive.
You might want to go with the tightest tolerances just to be safe, but do you want to spend the extra money? We know when precision is critical and when it’s not.
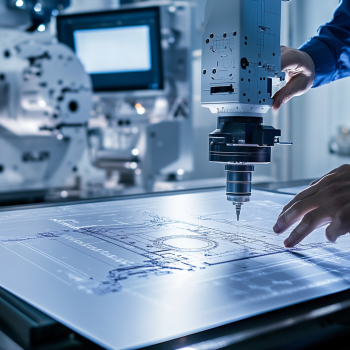
Tooling and Process Compatibility: Are You Designing with Production in Mind?
Not all designs are created equal when it comes to manufacturing processes. Imagine designing a part with intricate details that are almost impossible for the machines you have in-house to produce. That leads to production delays and additional costs for custom tooling. DFM makes sure your design is compatible with the machinery and processes you have available, whether that’s stamping, laser cutting or bending.
Do you want to avoid expensive custom tooling, or do you want to waste money fixing things? I thought so.
Scalability from Prototypes to Mass Production: Is Your Design Ready to Scale?
We all love prototypes. They’re small, manageable, and you feel like you have everything under control. But what happens when you need to scale up? All of a sudden, your perfectly fine prototype doesn’t translate well to mass production. This is where DFM comes into play. By thinking about scalability from the beginning, we can ensure that your designs are not only good for prototypes but can also be efficiently scaled to large production volumes.
Are you ready to make that jump from prototype to mass production without hitting a wall? With DFM, you can.
Surface Finishing Considerations: Can You Get Consistency Across Batches?
Surface finishes can be a challenge. You want your parts to look and feel great, but getting consistent surface treatments across different batches isn’t always easy. DFM takes surface finishing into account right from the design stage, ensuring that powder coating, anodizing or whatever finish you choose is applied uniformly, no matter how many parts you’re making.
How confident are you that you’ll get the same finish across all your parts? DFM handles that, so you don’t have to worry about it.
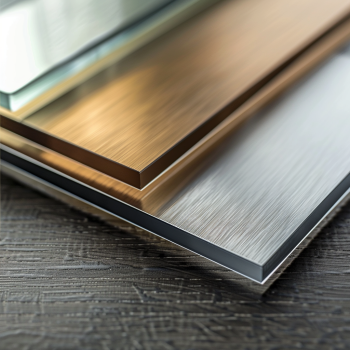
Assembly Interference: Are All Parts Playing Nice Together?
One of the worst surprises you can get during assembly is parts interfering with each other. This can create noise, vibration or even complete failure. DFM ensures that each part in the assembly fits together perfectly by considering clearances and alignments. We don’t just look at the individual pieces; we think about how they work together in the final product.
Have you ever had an assembly fail because of a small oversight? I have. With DFM, you can say goodbye to those nightmares.
Cost and Time Savings: Can DFM Save You Money?
Who doesn’t want to save money? By catching problems early and optimizing designs for manufacturing, DFM helps you save money. That includes reducing waste, avoiding expensive do-overs and getting your product to market faster. DFM not only saves you time, it saves you money.
Would you rather spend a little more up front to save thousands later? That’s what DFM is all about.
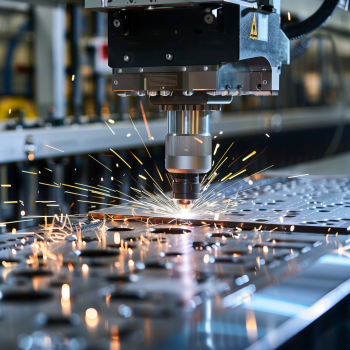
Conclusion: What’s Next?
It’s not just smart to bridge the gap between design and manufacturing. It’s necessary. With DFM, we bring ideas to life in a way that works for both designers and manufacturers, cutting costs, saving time, and producing better-quality products. Why leave your project’s success up to chance when you can have a smooth journey from concept to reality?
Let’s make your designs work—not just on paper, but in production, too.