Let's face it—welding carbon steel to stainless steel can feel like trying to get cats and dogs to play nice together. You’ve got two very different materials, each with its quirks. The stress of trying to fuse them without ending up with cracks, defects, or corrosion can be overwhelming. But don't worry. I’ve got 30 years of experience in sheet metal fabrication, and I’ve seen it all.
Yes, you can weld carbon steel to stainless steel successfully, but it requires precise control of heat, the right filler material, and meticulous preparation. The key lies in understanding the properties of both metals, using appropriate techniques, and anticipating challenges like cracking, carbon migration, and differing thermal expansion rates. By getting these details right, you can produce strong, reliable welds that hold up in tough industrial applications.
But let’s be real—getting this process right isn't just about slapping some metal together. It's an art form that requires finesse. So, how do you make sure you're welding these metals like a pro and not a mad scientist?

Carbon Steel vs Stainless Steel: What You Need to Know
The big challenge when welding carbon steel to stainless steel is the need to pay attention to the two types of steel. Carbon steel is just iron and carbon, while stainless steel also has chromium in it, which makes it more resistant to corrosion.
Why does this matter when you’re welding? Carbon steel doesn’t expand as much when you heat it up and cool it down. Stainless steel expands more when you heat it up and holds onto the heat longer, so it tends to warp more. When you’re welding the two together, and you don’t pay attention to these differences, you’ll run into problems. I’ve seen plenty of projects that have been ruined because someone didn’t take these differences into account. Don’t let that be you.
The Three Most Common Ways to Weld Carbon Steel to Stainless Steel
When you’re looking to weld carbon steel to stainless steel, three methods are most commonly used: TIG, MIG, and SMAW.
• TIG Welding (Tungsten Inert Gas Welding) is great for precision work. It gives you a clean, strong weld, but it’s slower and takes more skill.
• MIG Welding (Metal Inert Gas Welding) is a faster process and easier to learn, but the welds aren’t as strong.
• SMAW (Shielded Metal Arc Welding) is good for heavy-duty projects, but it can be more prone to defects.
Each of these methods has its pros and cons, depending on the job. The trick is to figure out which one is the right balance of speed, cost, and quality for your project. Want help figuring out which one that is?

Material Preparation Before Welding
I know you’ve heard this a million times, but hear me out. The prep work you do before you weld is the difference between being a professional and being a hack. When you’re welding two different metals together, cleanliness is next to godliness. Dirt, rust, or oil can ruin the weld and make the joint weak.
Before I strike an arc, I make sure both pieces of metal are clean. I use a wire brush or grinder to clean the mill scale off the carbon steel. With the stainless steel, I wipe it down with acetone to make sure it’s clean. And here’s a bonus tip: Don’t use the same tools on both pieces of metal. You don’t want to cross-contaminate.
Choosing the Right Filler Material
Filler material is the secret to a good weld. When you’re welding carbon steel to stainless steel, you can’t just grab any old filler rod off the shelf. The filler material has to bridge the gap between the two metals.
I usually recommend ER309L filler material. This grade of filler is designed for joining stainless steel to carbon steel. It resists the cracking and carbide precipitation that can happen during the welding process. The filler material helps make up for the different thermal expansion rates of the two metals, keeping the weld strong and durable.
If you use the wrong filler material, you’ll end up with a weak weld that’s prone to cracking.

How to Avoid Hot Cracking
Let’s talk about hot cracking, one of the worst things that can happen when you’re welding. Hot cracking is caused by the different rates at which carbon steel and stainless steel expand and contract when they’re heated and cooled. The result is cracks that can completely ruin your weld.
How do you avoid hot cracking? It’s simple: control your heat. Weld slowly, and let the material cool off slowly. If you use too much heat, you’ll create weak spots where the weld will crack as it cools.
The Use of Buffer Layers
This is one of the most overlooked aspects of welding different materials, but it’s also one of the most important. When you’re welding thicker sections, buffer layers can help relieve stress between the two materials. In this case, I use a stainless steel buffer layer between the carbon steel and the stainless steel. It helps bridge the gap in expansion and reduces the likelihood of cracking.
Buffer layers are especially important when you’re doing multi-pass welds, where you’re building up the weld material. By using buffer layers, you can help alleviate the differences in thermal expansion and allow the metals to play nice together.
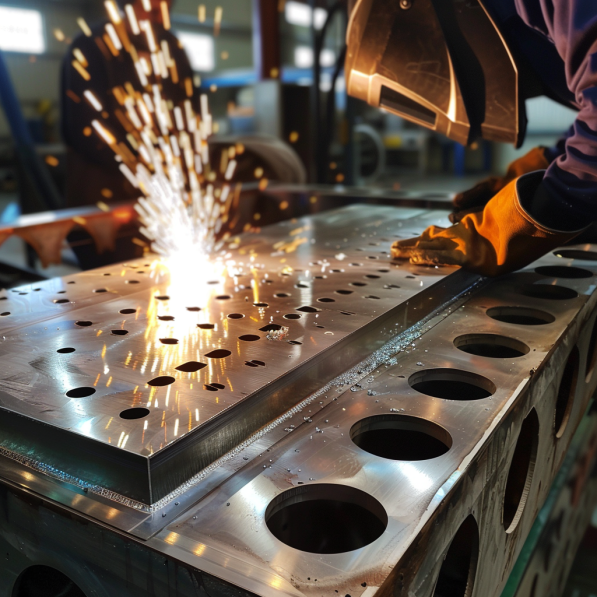
Environmental Considerations for Welding
Welding isn’t just about the metals; it’s also about the environment. I’ve worked in all kinds of environments, from controlled indoor shops to the great outdoors. Trust me, where you are makes a difference.
Humidity, for example, can lead to moisture getting trapped in your weld, causing porosity or even rust over time. Cleanliness is another factor; dust and dirt can contaminate your welds. And don’t forget about the purity of your shielding gas; a little impurity can ruin a perfectly good weld.
The Use of Clad Metals for Welding
If you’re thinking that welding carbon steel to stainless steel sounds like a pain in the ass, you’re right. One way around that pain is to use clad metals. These metals are pre-manufactured with a carbon steel core and a stainless steel surface, and they make the welding process a whole lot easier.
Clad metals help reduce the thermal stress because the materials are already bonded together at the molecular level. It’s less of a battle between the two metals and more of a happy relationship.
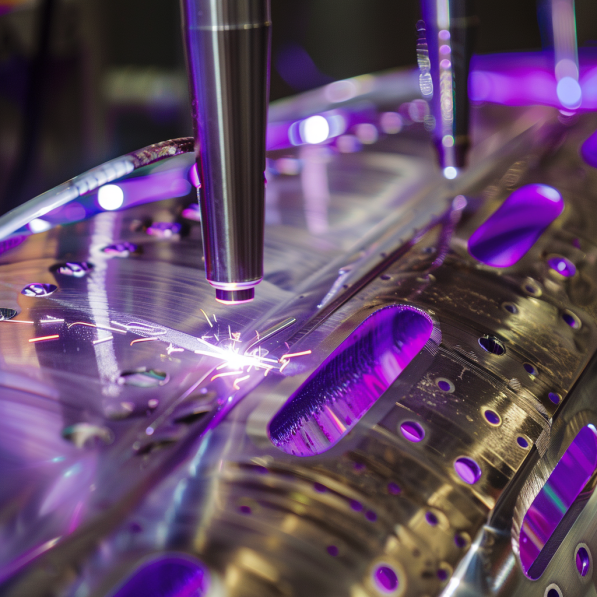
Standards and Certifications
Don’t overlook the importance of using proper standards and certifications when you’re welding carbon steel to stainless steel. I always make sure I’m following AWS D1.1 standards. This ensures the welds meet the specifications of the industry, which is especially important in areas like construction, aerospace, or food processing.
Welder certifications are also key. If you’re doing complex or high-risk welds, you need to be certified in dissimilar metal welding. You don’t want to find out the hard way that you weren’t certified to do a particular job.
The Impact of Carbon Migration
One of the lesser-known challenges of welding dissimilar metals is carbon migration. This happens when carbon from the carbon steel moves into the stainless steel during welding. This process creates carbide precipitation, which weakens the weld and can lead to corrosion and cracking over time.
To avoid carbon migration, I recommend using high-alloy filler material or a short arc welding technique. These methods help reduce the migration and keep the weld strong.
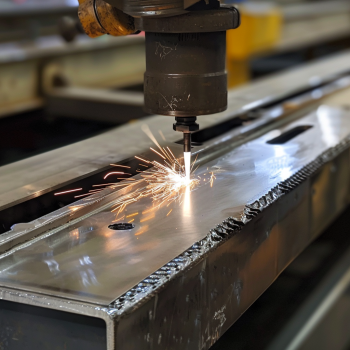
In Conclusion
So, can you weld carbon steel to stainless steel without any problems? Yes, you can, but you have to do it carefully, skillfully, and with the right tools. From choosing the right filler material to using buffer layers, welding two different metals is both a science and an art. Master it, and you’ll have welds that will last you a lifetime.