Do you get confused when it comes to all the numbers required for sheet metal bending? You’re not alone. A lot of people in the industry find the math and terminology intimidating. But you need to know this stuff if you want to be precise and efficient. In this post, I’m going to explain the K Factor in sheet metal bending, which is a fundamental concept that can drastically affect how you design and produce parts.
The K Factor in sheet metal bending is the ratio of the neutral axis to the material thickness. It’s a number that you multiply by the thickness of the material to determine how much the material is going to compress and stretch when you bend it. It’s important to know and apply the K Factor because it helps you make good parts, save money, and bend things accurately.
Sheet metal bending is an interesting and complex process. You use a CNC brake or a manual brake to form metal into 3D shapes. It seems simple, but there are a lot of things you need to know when you’re bending metal, including the K Factor. The K Factor tells you how much the metal is going to compress and stretch when you bend it, which affects the length and accuracy of the part you’re making.
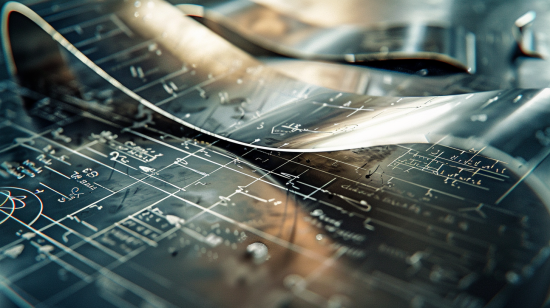
What is K Factor in Sheet Metal Bending?
The K Factor is the ratio of the thickness of the material being formed to the neutral axis. The neutral axis is an imaginary line that goes through the thickness of the material, is halfway through the material, and does not change during the bending process. The K Factor is the relationship between these two factors and tells you how much the material is going to compress on the inside and expand on the outside.
Understanding the K Factor is critical for anyone involved in sheet metal fabrication. It helps you calculate the proper bend allowance so that you can make parts that are the right size. By knowing the K Factor, you can account for the material deformation that occurs during bending and make parts that fit and are the right size.
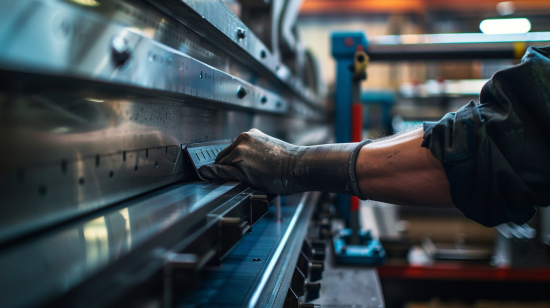
Why is the K Factor Important?
Knowing the K Factor before you bend something is important because it tells you what tooling to use and what angle to put in the brake. But it is more than that. It is critical to know the K Factor so that you can finalize your design. When you bend a part, it gets longer. You have to account for that expansion and compression when you design your part to make sure that your final part is the right size.
For example, if you are working on a project that requires precise measurements and you do not know the K Factor, you could make parts that do not fit or are not the right size. This could result in expensive rework and delays. By using the K Factor in your design process, you can avoid these issues and improve your overall production efficiency.
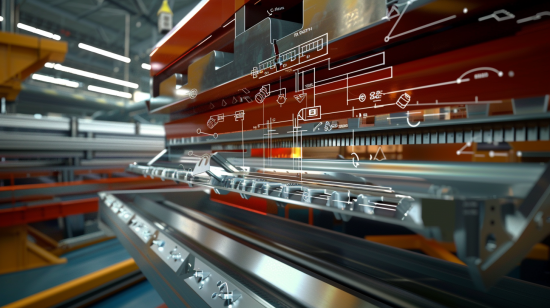
Key Terms Related to K Factor in Bending
To understand the K Factor, you need to know these terms: the apex, setback point, neutral line, and bend radius. These terms are essential to understanding and calculating the K Factor and how it affects bending.
Apex
The apex, or mold point, is the center of the bend. It’s the theoretical point where the tangents of the bend would meet if there was no radius. Knowing the apex helps you determine the exact center of the bend, which is crucial for making accurate measurements and calculations.
You can’t always see or measure the apex in practice, but knowing where it is helps you set up the bending process correctly. It’s an important reference point for calculating other things like setback and bend allowance.
Setback Point
The setback point is the distance from the apex back to where the bend line is. It’s influenced by the angle of the bend and the radius. Knowing the setback point helps you position your bends accurately so that each bend is where it’s supposed to be.
Setback points are important because you want your bends to be where you want them to be. If the setback isn’t right, you’ll have parts that don’t fit together, and you’ll have trouble assembling them. This leads to additional costs and problems
Neutral Line
The neutral line goes through the center of the part and is halfway through the thickness of the material. During bending, the material on the neutral line neither compresses nor expands. Knowing where the neutral line is helps you predict what the material is going to do during bending and make sure that your results are consistent.
The position of the neutral line can move around depending on the material and how you’re bending it. It’s important to know where the neutral line is so you can correctly calculate the K Factor and make sure that the part bends the way you want it to without any surprises.
Bend Radius
The bend radius is the inside of the part where the compression happens. It’s important to know about the bend radius because it affects how much compression and expansion you get. A smaller bend radius results in more compression and expansion, which you need to consider when you’re designing parts.
Choosing the right bend radius is important because you need to maintain the structural integrity of the part. If the radius is too small, you can get cracking or other defects. If the radius is too large, you may not get the bend you want.
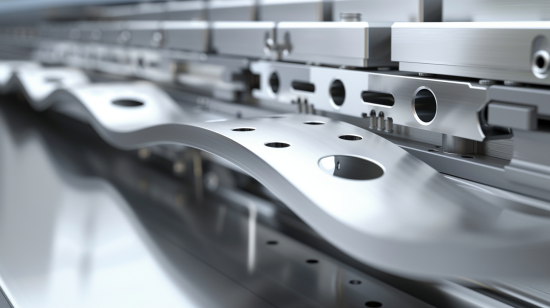
Calculating the K Factor
The K Factor is a critical ratio used in calculating the Bend Allowance (amount of stretch). The formula below shows this relationship between the centerline thickness (t) in the middle of the bend and starting material thickness (MT).
K=(t/MT)
T = Centerline thickness in bend
MT = Material Thickness
This ratio is important because it helps you calculate the bend allowance, which is the amount of material you need to make the bend. The bend allowance is critical because it ensures that your final part dimensions are correct. By calculating the K Factor and bend allowance, you can adjust your design to account for material deformation and make sure that you get the results you want.
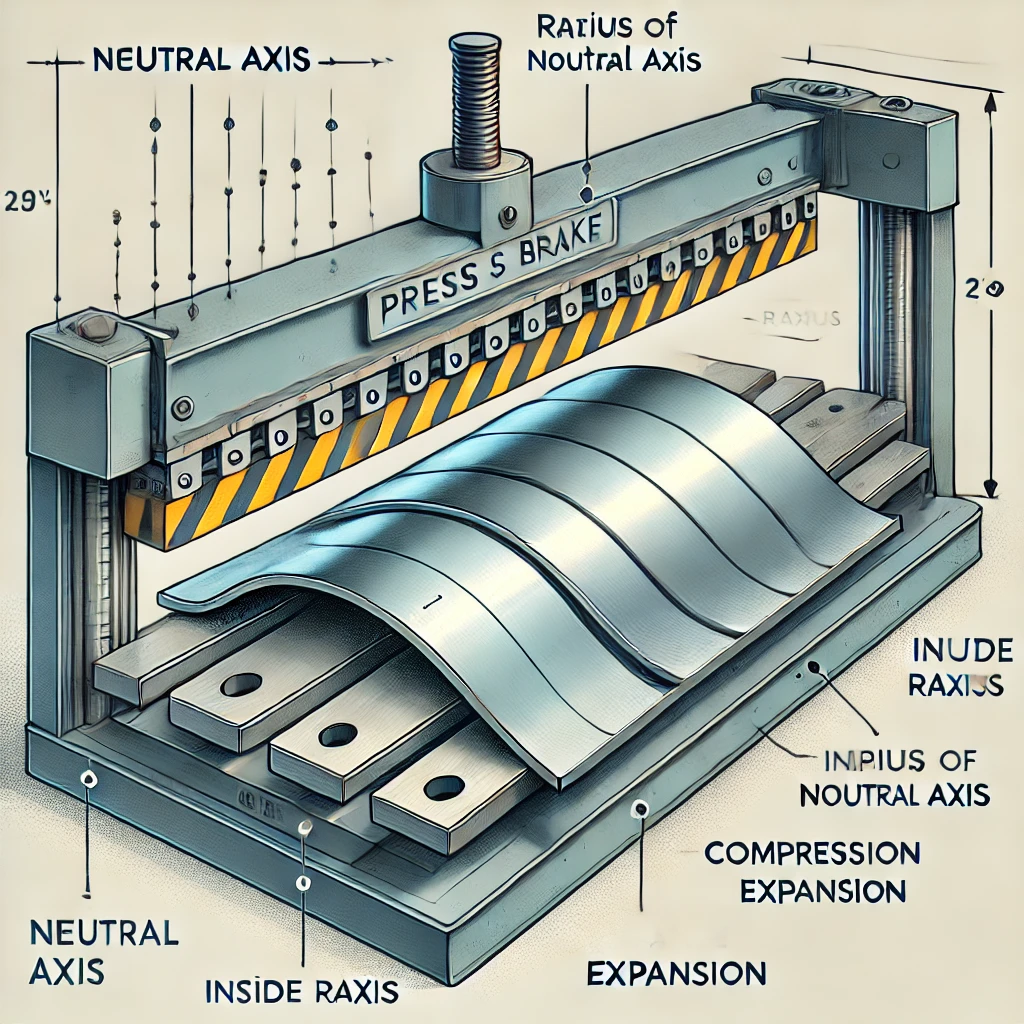
K Factor vs. Y Factor
While the K Factor is the most commonly used, the Y Factor is another way of calculating the internal stresses in the material when you bend it. The Y Factor gives you a more accurate calculation, but it’s more complicated and is typically only used for very specialized bends.
In most cases, the K Factor is good enough for regular bending. It strikes a balance between accuracy and simplicity, which is why most people use it. However, for special bends and special materials, you might need the Y Factor to get the accuracy you need.
Material Properties and Their Impact on K-Factor
Different materials have different properties that affect the K Factor. For example, aluminum is more ductile than steel, so it behaves differently when you bend it. You need to know how materials behave when you bend them so that you can calculate the K Factor correctly and get the results you want when you bend parts.
For example, aluminum is more ductile, which means it deforms more before it breaks. This affects the position of the neutral axis and, in turn, the K Factor. Steel, on the other hand, is not as ductile but has a higher tensile strength, which affects how it bends differently.
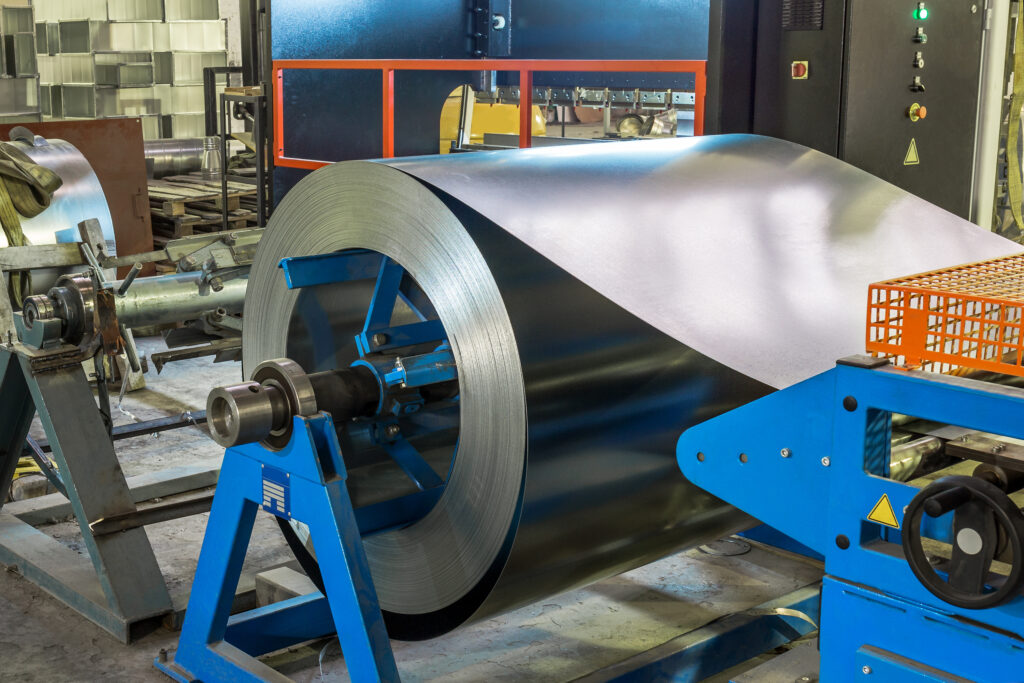
Advanced Bending Techniques
Advanced bending techniques like air bending, bottom bending, and coining affect the K Factor differently. Each technique offers different levels of accuracy and control over material deformation, which affects the final dimensions and quality of the part you bend. Knowing which technique to use based on your K Factor can have a big impact on your bending.
Air Bending
Air bending is when you bend the metal without completely hitting it into the die. It allows you to be flexible and requires less force, but the K Factor can change depending on the material and the angle of the bend
Bottom Bending
Bottom bending, or bottoming, is when you press the metal all the way into the die. This method gives you more control and better accuracy. It results in a more consistent K Factor, but it requires more force and better tooling.
Coining
Coining is when you press the material all the way into the die with a lot of force, causing the material to deform. This method gives you the most accurate and consistent K Factor, but it’s more expensive because of the force and tooling required.

Software Integration for K-Factor Calculation
Modern CAD/CAM software often includes built-in ways to calculate the K Factor, which lets you make adjustments and see the results in real time. This integration makes it easy to make sure that your designs are set up to handle the K Factor from the beginning. By knowing what your software can do, you can make your work faster and more accurate.
Software like SolidWorks, AutoCAD, and others have tools that let you simulate bends and calculate the K Factor automatically. This instant feedback lets you make changes on the fly to make sure that your final part matches your requirements. This reduces the need for trial and error in the shop.
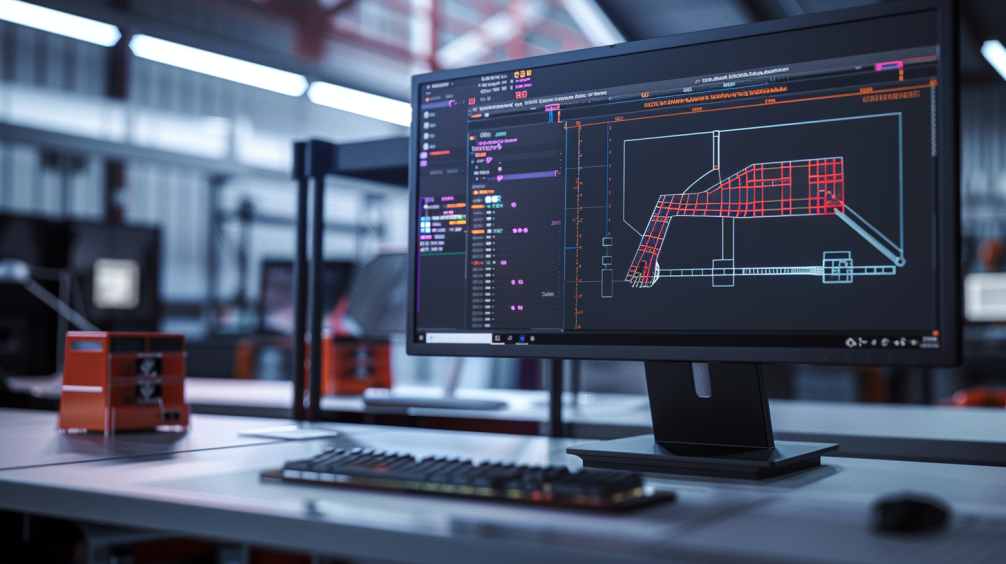
Practical Applications of K Factor
Knowing and using the K Factor can make a big difference in how well you bend sheet metal. Here are some ways to use it:
Design Optimization
If you use the K Factor in your designs, you can make your parts better so they fit and work well. That way, you won’t have to adjust or remake as many parts, saving you time and money.
Tooling Selection
The K Factor helps you pick the right tools and the right angle in the brake so you can make the bends correctly. This helps you make better parts and makes it less likely that you’ll make mistakes.
Production Efficiency
When you use the K Factor, you can do the math more accurately. This helps you set up your jobs faster and get better at making the parts. This makes you better at your job and helps you get more done.

Conclusion
Understanding the K Factor in sheet metal bending is critical to making parts that are right and work well. This ratio tells you how much the material is going to compress and expand when you bend it so you can make parts that are the right size.
When you use the K Factor in your designs and use tools like bending calculators, you make your job easier and make fewer mistakes. This saves you money and makes your parts better.
If you want to be good at making parts and have happy customers, you need to know the K Factor. Whether you design parts, make them, or use them, knowing the K Factor will make you better at bending metal and make your projects more successful.