Do you having trouble finding the right sheet metal for your next project? Using the wrong material can lead to costly production delays, poor product performance, or even project failure. But with so many types of sheet metal to choose from, how do you know which one is right for you? To make an informed decision that aligns with your project’s requirements and budget, you need to understand the characteristics of each material.
There are many types of sheet metal, each with its own unique properties that make them suitable for certain applications. The most common materials include stainless steel, cold-rolled steel, aluminum, copper, and specialized alloys like 7075 aluminum. When selecting sheet metal, you need to consider factors such as formability, weldability, corrosion resistance, strength, weight, and cost to ensure the material meets the needs of your application.
Choosing the right sheet metal isn’t just about knowing what types are available; it’s about understanding the specific properties that make each material unique. For example, while stainless steel might be ideal for environments with high corrosion risk, aluminum might be better for applications where weight reduction is critical. This guide will explain the key factors to consider when choosing sheet metal and explore the properties of the most common materials to help you make a decision that enhances the quality and efficiency of your project.
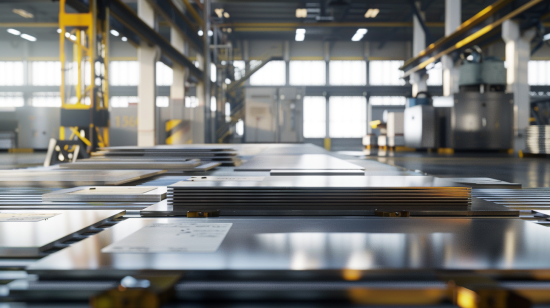
What Factors Should You Consider When Choosing Sheet Metal?
Choosing the right sheet metal starts with understanding the critical factors that influence material selection. These factors include:
- Formability: How easily can the material be shaped into the desired form? This is crucial for complex designs that require bending or stretching without cracking.
- Weldability: Can the material be welded without defects? Some metals weld better than others, and poor weldability can lead to weak joints and potential failure.
- Corrosion Resistance: How well does the material withstand exposure to environmental elements? Corrosion can drastically reduce the lifespan of metal parts, especially in harsh environments like marine or industrial settings.
- Strength: What load can the material bear without deforming? Depending on the application, you may need a material that offers high tensile strength or one that balances strength with flexibility.
- Weight: Does the material’s weight impact the overall design and functionality? In applications like aerospace and automotive, reducing weight is often a priority.
- Cost: How does the material fit within your budget? The cost of sheet metal can vary widely, so it’s essential to balance performance with expense.
- Surface Finish Requirements: The final appearance and texture of the sheet metal may be crucial depending on the application. Surface finish options like brushed, polished, or matte can affect both aesthetics and functionality.
- Example: A polished stainless steel finish is often used in high-end kitchen appliances for its sleek look, while a bead-blasted finish might be preferred for parts requiring a non-reflective surface.
- Resistance to Wear and Tear: Some applications require materials that can withstand abrasion, friction, and general wear over time.
- Example: Abrasion-resistant steel (AR) is often used in mining and construction equipment where durability against wear is essential.
- Impact Resistance: In industries where the material might be subject to impacts or collisions, selecting a metal that can absorb and withstand shocks is crucial.
- Example: High-strength, low-alloy (HSLA) steel is used in automotive frames and bumpers due to its excellent impact resistance.
- Temperature Resistance: Some applications require materials that can withstand extreme temperatures, whether hot or cold, without losing their structural integrity.
- Example: Inconel, a nickel-chromium-based superalloy, is used in jet engines and gas turbines due to its ability to maintain strength at high temperatures.
- Availability and Lead Time: The availability of the material and how quickly it can be sourced may also impact your decision, especially in time-sensitive projects.
- Example: Standard grades of aluminum and steel are widely available and can often be sourced quickly, whereas specialized alloys might have longer lead times.
- Compatibility with Joining Techniques: Consider how the material will be joined with other components, whether through welding, riveting, or adhesive bonding, and how well the material accommodates these methods.
- Example: Certain alloys, like 7075 aluminum, can be more challenging to weld, influencing the choice of joining technique.
- Thermal Expansion: The rate at which a material expands and contracts with temperature changes can be crucial in maintaining tight tolerances in assembled products.
- Example: Aluminum expands at a higher rate than steel, which might affect joint stability in environments with significant temperature fluctuations.
- Regulatory and Compliance Standards: Certain industries require materials that comply with specific standards or regulations, such as those set by the FDA, ASTM, or ISO.
- Example: Medical devices often require materials like 316L stainless steel, which meets stringent biocompatibility standards.
- Recyclability and Sustainability: The environmental impact of material selection is increasingly important, with a focus on recyclability and the life cycle of the material.
- Example: Aluminum is highly recyclable, and using recycled aluminum can significantly reduce the environmental footprint of manufacturing processes, making it a preferred choice in sustainable product design.
- Tolerances and Dimensional Stability: Some materials maintain tighter tolerances and dimensional stability under machining and fabrication processes, which is essential for precision components.
- Example: Cold rolled steel (CRS) is favored for applications requiring precise dimensions and minimal deformation, such as in automotive and industrial machinery components.
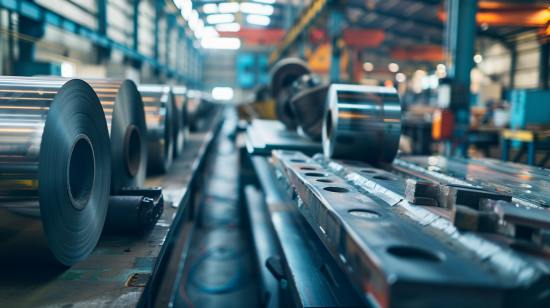
What Are the Most Common Types of Sheet Metal?
1. Stainless Steel
Stainless steel is renowned for its corrosion resistance, making it ideal for applications where exposure to moisture or chemicals is common. The two main categories of stainless steel used in sheet metal fabrication are:
- 300 Series (Standard Stainless Steel)
- 304: The most widely used grade, 304 offers a good balance of corrosion resistance, formability, and weldability. It is commonly used in kitchen equipment, industrial machinery, and automotive components.
- 316: Known for its superior corrosion resistance, particularly in chloride environments, 316 is often used in marine applications, chemical processing, and medical devices.
- 400 Series (Magnetic Stainless Steel)
- 410: This grade offers less corrosion resistance but is heat treatable, making it suitable for applications requiring high strength and moderate corrosion resistance, such as fasteners and cutlery.
- 430: A cost-effective alternative to other stainless steels, 430 is used in less demanding applications where corrosion resistance is not the primary concern, such as appliance surfaces.
- Spring-Like Stainless Steel
- 301, 17-4, 1095, 1075: These grades are known for their work-hardening properties, making them suitable for applications like springs and other flexible components that require high strength and elasticity.
2. Cold Rolled Steel (CRS)
Cold rolled steel is produced by rolling steel at room temperature, which increases its strength and gives it a smooth finish. CRS is known for its tight tolerances and is available in grades such as 1008 and 1018. It is often used in precision parts where surface quality is important, such as in the automotive industry.
3. Pre-Plated Steel
Pre-plated steel includes:
- Hot-Dip Galvanized Steel: Steel that has been coated in zinc to provide a corrosion-resistant finish. It is widely used in construction and automotive industries.
- Galvannealed Steel: A combination of galvanized and annealed steel, offering enhanced corrosion resistance and ease of painting, making it ideal for exterior applications and automotive body panels.
4. Aluminum
Aluminum is valued for its lightweight properties and resistance to corrosion. The most common grades used in sheet metal fabrication are:
- 1100: This grade is known for its excellent corrosion resistance, ductility, and weldability, making it ideal for chemical and food processing industries.
- 3003: Stronger than 1100, 3003 offers good formability and corrosion resistance, making it suitable for HVAC components, roofing, and siding.
- 5052: A marine-grade aluminum, 5052 provides higher strength and excellent corrosion resistance, commonly used in marine, automotive, and fuel tank applications.
- 6061: A structural alloy with high strength, 6061 is used in applications requiring durability and load-bearing capacity, such as aircraft structures and automotive parts.
- 7075: Known for its extremely high strength, comparable to many steels, 7075 is used in aerospace and high-stress applications. It offers excellent fatigue resistance but is less corrosion-resistant and more difficult to weld.
5. Copper/Brass
Copper and brass are often chosen for their electrical conductivity and aesthetic appeal. Common grades include:
- C110, C101 Copper: These grades are widely used in electrical applications due to their excellent conductivity. They are also selected for architectural elements for their visual appeal.
- Cartridge Brass: Used in situations requiring a combination of strength and corrosion resistance, cartridge brass is often found in decorative applications and precision instruments.
6. Bronze
- Bronze 220: Bronze is known for its strength and wear resistance. It is commonly used in applications requiring durability, such as bushings, bearings, and marine hardware.
7. Titanium
Titanium is prized for its high strength-to-weight ratio and excellent corrosion resistance, especially in extreme environments.
- Grade 2: Pure titanium, used in applications requiring high corrosion resistance and moderate strength, such as chemical processing equipment and medical implants.
- Grade 5 (Ti 6Al-4V): The most commonly used titanium alloy, offering high strength and lightweight properties. It is ideal for aerospace components, medical devices, and high-performance automotive parts.
8. Nickel Alloys
- Inconel 625: A nickel-chromium-molybdenum alloy known for its high strength and resistance to extreme temperatures. It is commonly used in aerospace, chemical processing, and marine industries.
9. Zinc-Coated Steel (Galvanized Steel)
Zinc-coated steel is widely used for its excellent corrosion resistance and is commonly found in construction and automotive applications. The zinc coating protects the steel from rusting, making it ideal for outdoor use.
10. Magnesium
- AZ31: Magnesium is the lightest structural metal, offering excellent machinability and strength. AZ31 is commonly used in applications where reducing weight is critical, such as in automotive and aerospace industries.
11. Beryllium Copper
- C17200: Known for its high strength and conductivity, beryllium copper is used in precision instruments, aerospace components, and electrical connectors.
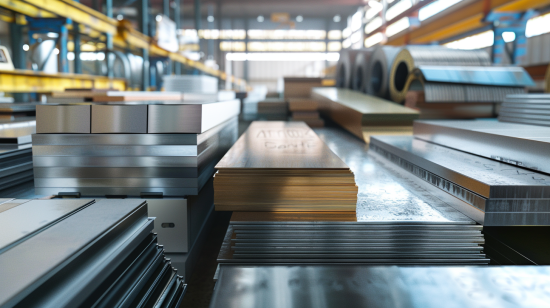
Conclusion
Selecting the right sheet metal is about more than just picking a material off a list. By thinking about factors like formability, weldability, corrosion resistance, and specialized requirements like thermal conductivity and recyclability, you can make sure your material choice matches up perfectly with your project’s needs. Whether you’re working in aerospace, automotive, or construction, understanding these properties and how they work together will help you choose a material that makes your final product better, stronger, and more cost-effective.