Designing custom sheet brackets can be a daunting task. There are many things to consider, from material selection to manufacturing processes, to ensure the final product meets your needs. As a leader in the industry, we understand the challenges faced by engineers and product developers. Our goal at Premium is to make the design and manufacturing process as easy as possible for you.
To design custom sheet brackets that work, you need to consider the material strength, the proportions of the flanges, where the holes go, and how easy it is to install. Work with seasoned manufacturers to make sure your design is optimized for both manufacturing and use. When you do this, you will get high-quality, long-lasting brackets that match your needs.
Custom sheet bracket design is more than just making something that works. It’s about making something that fits, lasts, and doesn’t cost too much. At Premium, we use our years of experience and the latest fabrication tools to make brackets that are better than what you’d expect. In this guide, we’re going to cover the important things to know about custom sheet bracket design and how we can help you get the best brackets possible.
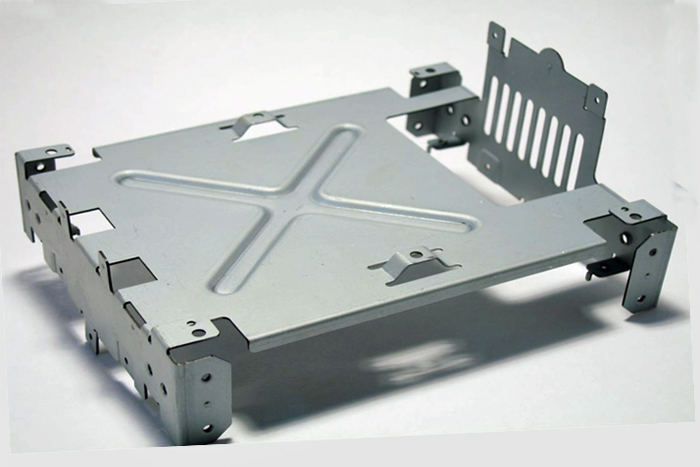
What Are Sheet Metal Brackets?
Sheet metal brackets are the go-between parts that connect, align, or strengthen things. They can hold things together, provide structural support, or align parts inside a box. Depending on the design, a bracket can be mounted with hardware or welded inside a sheet metal part. They are usually functional, but they can be decorative, too.
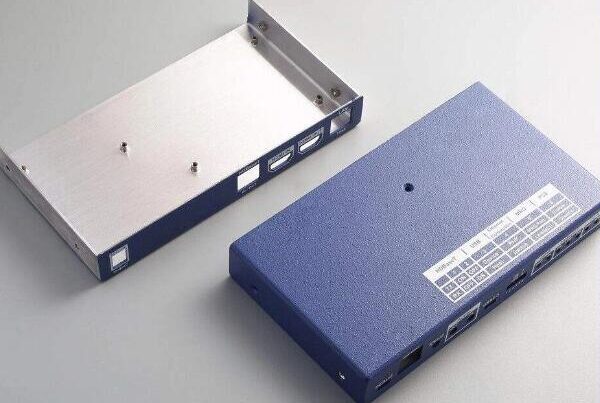
Standard Bracket Materials
Choosing the right material is crucial to making your brackets work and last. At Premium, we make brackets out of various materials, including:
Cost-Effectiveness:
Cold Rolled Steel: Affordable and strong, suitable for most general-purpose applications.
Aluminum: More expensive but offers weight savings and excellent corrosion resistance.
Corrosion Resistance:
Stainless Steel: Best for corrosion resistance, suitable for harsh environments and sanitary applications.
Galvanized Steel: Provides good corrosion resistance at a lower cost, ideal for outdoor and industrial use.
Strength and Durability:
High-Strength Low-Alloy Steel: Offers superior strength and durability, perfect for heavy-duty applications.
Stainless Steel: Maintains strength in various conditions, ideal for critical applications.
Ease of Fabrication:
Mild Steel: Easy to work with, weld, and form, making it versatile for different designs.
Aluminum: Easy to machine and can be anodized for additional protection.
Aesthetic and Functional Requirements:
Brass: Combines functionality with aesthetics, suitable for decorative and electrical applications.
Copper: Offers a unique combination of electrical conductivity and corrosion resistance, used in specialized electrical and thermal management applications.
Each material has its advantages and is chosen based on the needs of the application.
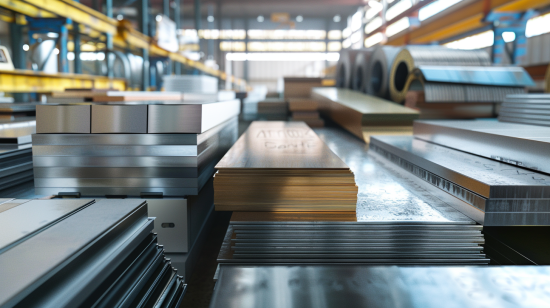
How Premium Fabricates Brackets
Cutting
The process of making brackets starts with cutting. We use laser cutters to accurately size flat pieces of sheet metal. Laser cutting is precise and versatile, allowing us to handle complex designs and tight tolerances.
Forming
Then we bend the cut metal pieces into the right shapes using press brakes. This forming process is critical for getting the right angles and dimensions. With U-channel and hat-channel brackets, keeping the flange proportions correct during this step is crucial to keeping the part from sliding in the press brake.
Punching
For brackets that need mounting holes, we punch the holes in with a punch press. Getting the hole placement right is important. We recommend putting holes a safe distance from bends to make punching easier, which helps keep costs and lead times down.
Welding
Brackets that are meant to reinforce or stiffen metal are often welded in place instead of bolted. Welding gives you a strong, long-lasting connection that can handle high stress and the environment.

Common Bracket Types
At Premium, we make a variety of bracket types, each with its purpose:
L Brackets
L brackets are brackets with one bend to make an L shape, usually at a 90-degree angle. They are versatile and used for many different mounting applications.
Z Brackets
Z brackets have two bends that make parallel flanges going in opposite directions. This design is great for anchoring parts at different levels inside a box or holding up parts that need airflow underneath them.
U-Channel Brackets
U-channel brackets have two bends at angles facing each other to make a U shape. They are usually longer and need more holes for hardware, making them great for mounting two parallel surfaces together.
Hat Channel Brackets
Hat channel brackets look like a top hat and are welded inside parts made of weaker metal to keep them from collapsing inward. They are commonly used inside metal doors and other similar structures.
Gusset Brackets
Gusset brackets, usually triangular, are welded inside metal parts to make them stronger. They are often used in architectural applications, such as bridges, when you need the part to be stronger.
Angle Brackets
Angle brackets are like L brackets but are usually heavier and used for more robust applications. They are great for holding heavy loads and adding structural strength.
Corner Brackets
Corner brackets are made to join two parts together at a 90-degree angle. They are often used in frames and boxes to give extra support at the corners.
Adjustable Brackets
Adjustable brackets let you move the bracket or the item it is holding. These are great for applications where you need to be able to change things around.
Shelf Brackets
Shelf brackets are made specifically to hold up shelves. They come in many shapes and strengths, depending on how much weight they need to hold and what they look like.
T-Brackets
T-brackets look like a “T” and are used to join two pieces of material that come together at a 90-degree angl. They give you support and stability.
Strap Brackets
Strap brackets are long pieces of flat metal with holes for mounting. They are used to strengthen joints and support structures, often found in cabinetry and construction.
Hanging Brackets
Hanging brackets are used to hang things on walls or ceilings. They can be simple hooks or more complex designs to hold up heavy things.
Flat Brackets
Flat brackets are flat pieces of metal with holes for mounting. They are used to join two pieces of material that come together flat, often giving you more support and stability.
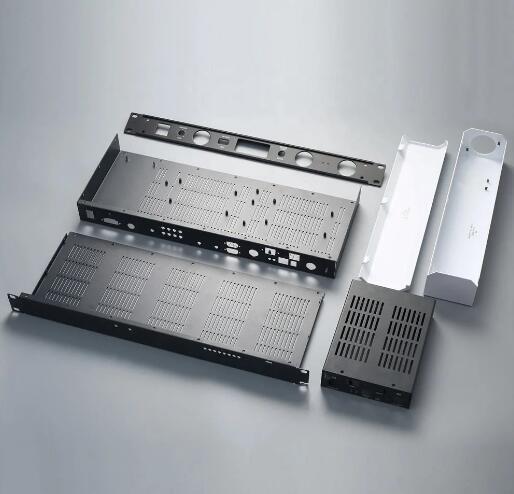
Design Considerations
Material Strength
Always think about how much weight your bracket will need to hold up. Will the material you chose be strong enough to do the job? If you need help picking the right material for your project, our team can help.
Flange Proportions
On U-channel and hat-channel brackets, you have to keep the flanges the right size or the part will slide in the press brake. Make the forming flanges shorter than the base flange to ensure the bracket will press correctly. If you do it the other way, you may need custom tools, which will cost you more money.
Hole Placement
One of the most common questions we get from customers designing brackets is where to put the bracketry holes in relation to bends. Whenever possible, put holes a safe distance from bends to make punching easier, which will help save you money and get your parts faster. If you have questions about your bracket design, talk to our team or, better yet, ask for a design review!
Bracket Geometry
Getting the right shapes to make your bracket strong and light is important. Think about the overall shape of your bracket to make sure it will do what you need it to while being cheap to make.
Thickness and Bend Radius
The thickness of the metal and the bend radius are critical to how strong your bracket will be. Make sure the bend radius is big enough so that you don’t crack the metal or make it weak.

Load Distribution and Multiple Mounting Points
When you design brackets, you must spread the load out so that the bracket doesn’t break. The more places you put your brackets, the more area the load covers, which makes your bracket stronger and more stable. This makes sure your bracket doesn’t break and lasts a long time.
Vibration and Shock Absorption
If your brackets are going to be in a place where things shake or hit them, you can make your brackets better by using things that absorb the shock. Things like flexible mounts or rubber grommets can make your brackets last longer and keep them from breaking. This is important in cars and factories because it makes things last longer and work better.
Thermal Expansion and Material Compatibility
The way the metal in your brackets gets bigger and smaller when it gets hot or cold can mess up your brackets. You have to pick the right metal and make sure it doesn’t get too hot or cold. If you put things in your bracket that let the metal move, it will keep your brackets from breaking when it gets hot or cold.
Weight Considerations and Material Selection
Some things can’t be too heavy, like planes and cars. You have to make your brackets light but strong. You can do this by picking light metals like aluminum or materials that are a mix of different things. If you make your brackets light, they will make your thing work better without using too much fuel.
Aesthetic Considerations and Surface Finish
If you can see your brackets when you’re done, they have to look good. You can make them look good by putting the right stuff on them. This not only makes your brackets look good but also keeps them from rusting. If you make your brackets the same color as everything else, they will look good and make your stuff look nice.
Ease of Manufacturing and Simplified Geometry
When you design your brackets, you need to make them easy to make and not cost too much. You can do this by using parts that are easy to make and don’t take a long time. If you make your brackets easy to make, they will not cost too much and be the same every time.
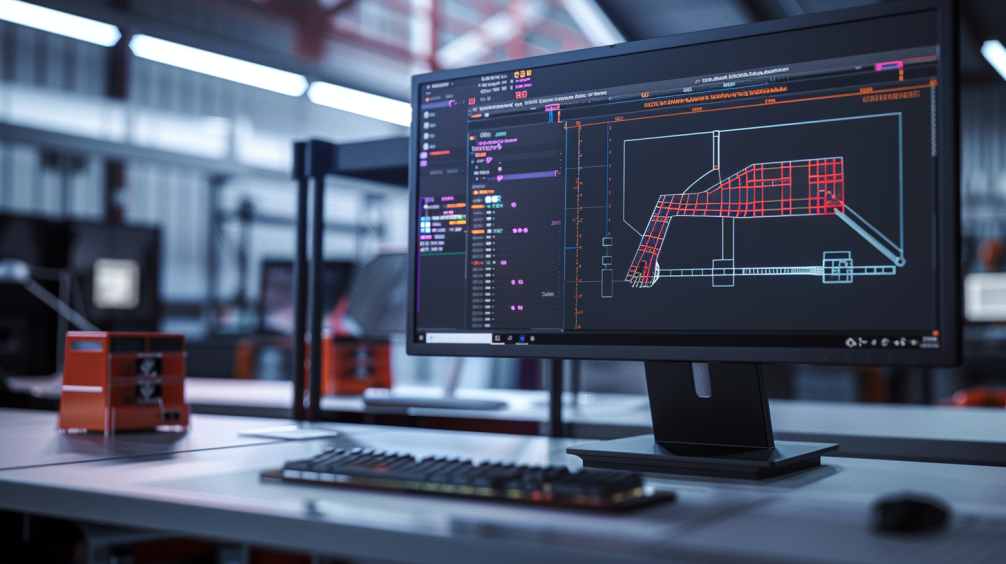
Future Modifications and Modular Design
If you want to change your brackets after you finish them, you have to make them so you can. By doing this, you can change your brackets or make them better without starting over. This is good for things that change a lot because you don’t have to start over every time.
Electrical Conductivity and Insulation
If your brackets need to move electricity, you have to put the wires in the right place. This means you have to use the right metal or put things in your brackets to keep the electricity from going where it’s not supposed to. If you need to keep electricity out of your brackets, you have to use things that stop it from getting in.
Fluid Dynamics and Corrosion Resistance
If your brackets are around water, you have to make sure the water doesn’t mess them up. You can do this by picking the right metal or putting things on your brackets to keep the water from making them break. This is important in boats and factories because it makes your brackets last longer.
Fastening and Joining with Self-Locking Features
When you put your brackets together, you have to make sure they stay together. You can do this by using special things to keep them from falling apart. If you use these things, your brackets will stay together and not break.
Ergonomics and User-Friendly Design
When you make your brackets, you have to make sure they are easy to use. You can do this by making sure they don’t hurt people or are easy to use. If you do this, people will like your brackets and use them more.
Tolerance Management and Dimensional Stability
When you make your brackets, you have to make sure they are the right size and fit together right. You can do this by making sure the parts are the right size and don’t change when you make them. If you do this, your brackets will be good and work right.
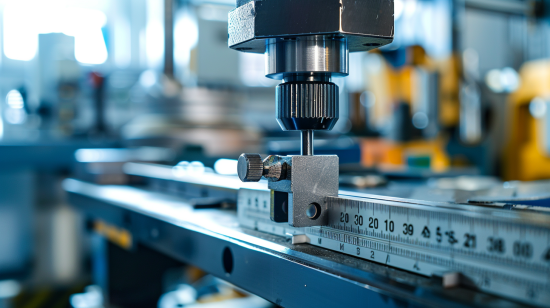
Integration with Other Components
Modularity
Make brackets that are easy to put together with other parts. This modular approach will help you put things together and keep them up easier.
Compatibility
Make sure your brackets work with the other stuff you have. This will help you put things together right and make sure your design works.
Safety and Reliability
Safety Factors
Put in some extra safety into your design to make sure your bracket can handle loads and stress you didn’t see coming.
Reliability Testing
Test your brackets to make sure they will last a long time and do what you need them to. This testing will help you find places where things could break and make your design better.
Design for Ease of Installation
Mounting Ease
Design brackets to be easy to put in and take out. This will not only help you put things together, but it will also make it easier to keep things up and change them when needed.
Accessibility
Make sure you can get to your brackets easily to keep them up and change them when you need to, especially if you have to keep them up all the time.
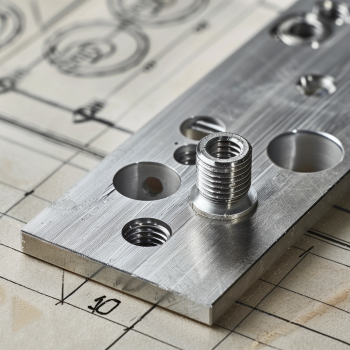
Surface Treatment
To make your brackets last longer and look better, think about these surface treatments:
Powder Coating
Powder coating makes your brackets look good and protects them from rust. You can get it in different colors to make your brackets look cool.
Plating
Plating your brackets with zinc or nickel makes them last longer and keeps them from rusting.
Anodizing
Anodizing is good for aluminum parts. It makes them wear better and last longer.
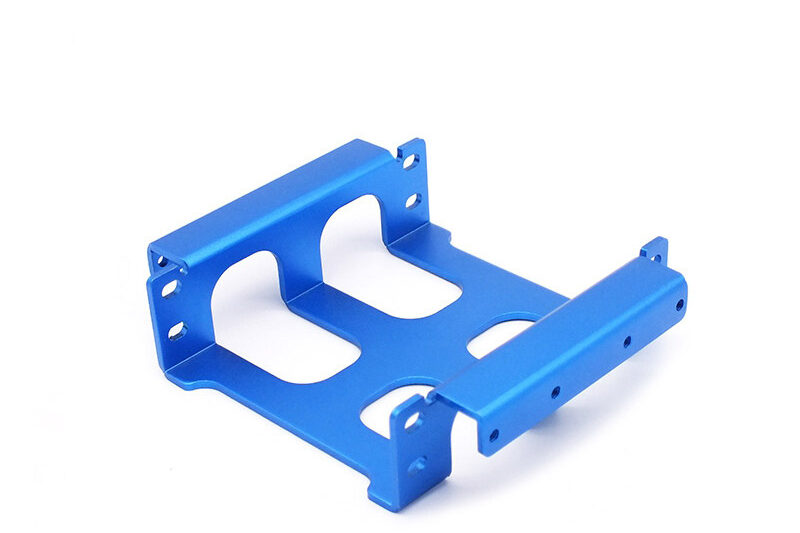
Design Optimization
DFM (Design for Manufacturing)
When you design something so that it’s easy to make and doesn’t cost too much, that’s what we call Design for Manufacturing (DFM). Work with your suppliers when you design your brackets to find problems and make it easier to make your brackets.
Prototyping and Testing
Build a prototype first to make sure your design works before you make a bunch of them. Test your brackets over and over to make sure they will work right and last a long time.
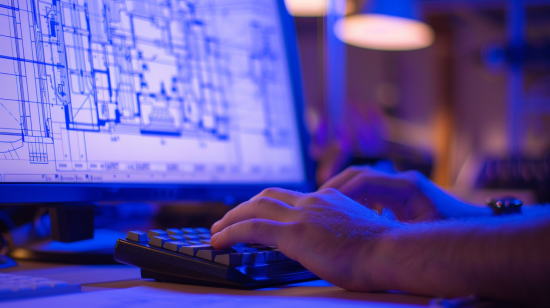
Common Challenges and Solutions
Consistency in Surface Treatment
Getting brackets to look the same can be hard, especially when you make a lot of them. To help, you can use the same application tools and check everything to make sure it’s right.
Assembly Interference
Sometimes, your brackets won’t go together right because the holes aren’t in the right place. To fix this, think about how the parts fit together and make sure the holes are not too big or too small.
Packaging for Transportation
You have to pack your brackets right to keep them from getting messed up during shipping. Think about how you can keep your brackets safe, label your boxes, and pack them so you can fit more in a box and pay less to ship them.
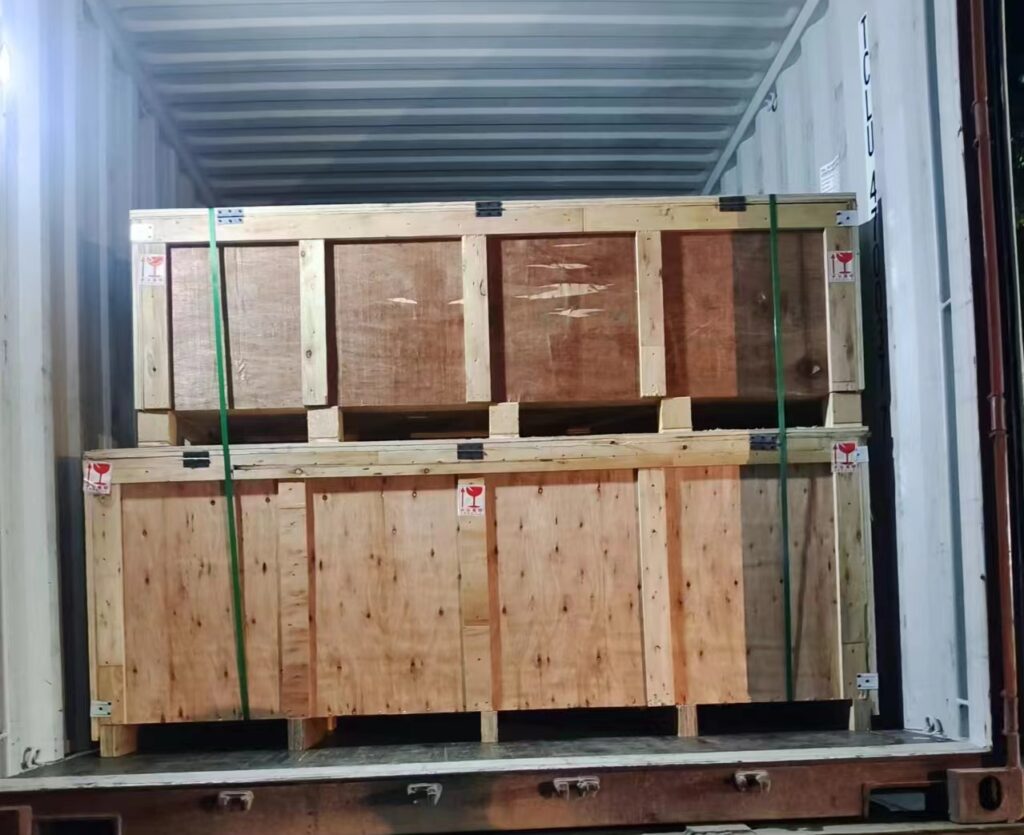
Premium's Expertise
Experienced Team
We have been doing this for over 8 years and have made a lot of brackets. Our team knows how to design and make high-quality sheet brackets.
One-Stop Service
We can help you from the start of your project to the end. We make it easy for you to get what you need, and you don’t have to talk to a bunch of different people.
Customer Collaboration
We work with you to make your design better and easier to make. We make sure that what we make is what you wanted and does what you need it to do.
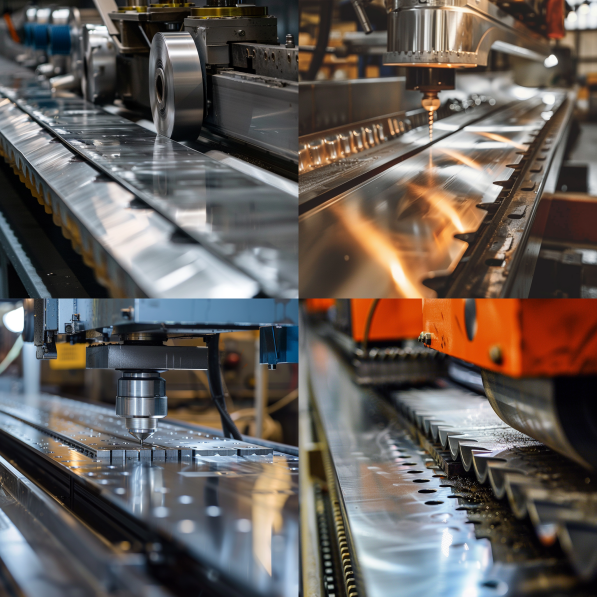
Conclusion
Designing brackets that work is all about picking the right material, making them right, and getting them to look good. When you work with a team like Premium, you know you’re going to get brackets that work great and look good. We know what materials to use, how to bend the metal, and how to coat the brackets to make them last a long time. Whether you just need help getting started or need us to make a bunch of brackets for you, Premium is here to help you get what you need.