Are you having trouble finding parts that are tough, accurate, and won’t break the bank for your projects? It’s a real pain in the neck to try to balance quality, customization, and cost. Fabricated sheet metal assemblies are the perfect solution. They help you get all of that stuff done faster than anything else. When you understand how they work, you’ll look like a genius, and your products will come out better than ever.
You need to know about sheet metal assemblies because they are strong, accurate, customizable, fast, and versatile. They are used in every industry from aerospace to automotive to make accurate parts that work every time. They help you build strong stuff, customize your parts, and make them faster.
Do you want to know how sheet metal assemblies can help you with your projects? I’m going to break down everything you need to know about sheet metal assemblies. I’ll show you the types, processes, techniques, and benefits of using sheet metal assemblies in your projects. By the time you’re done reading this, you’ll have everything you need to make your products stronger, more accurate, and more reliable than ever.
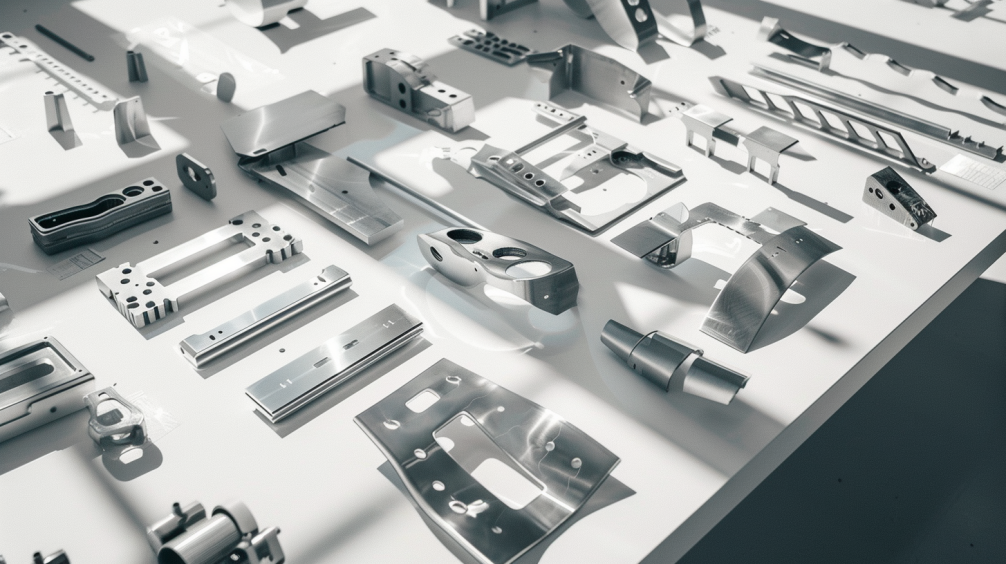
What Types of Sheet Metal Assemblies Are There?
There are several different types of sheet metal assemblies. They range from simple to complex, depending on what you need to do. Here are the primary types:
- Single-piece Assemblies: These are simple structures that don’t require much joining. They are perfect for making brackets, single-piece enclosures, and simple structural supports. This kind of assembly is fast and cheap to make because you don’t have to do much joining.
- Multi-piece Assemblies: These are assemblies that require multiple parts and more complicated joining techniques. These assemblies are used to make things like frames for automobiles, industrial machinery, and housings for electronics. They allow you to create more detailed and robust designs that can be used for more demanding applications.
- Modular Assemblies: These assemblies are designed to be flexible and scalable. They are made up of parts that can be easily replaced or upgraded. These assemblies are used to make things like modular shelving systems, consumer products that can be customized, and industrial equipment.
- Sub-assemblies: These are small assemblies that are put together to make a final product. Examples of sub-assemblies include engine sub-assemblies and electronic control units. You put them together separately, and then you put them into the final product. This makes them easier to handle and easier to put together.
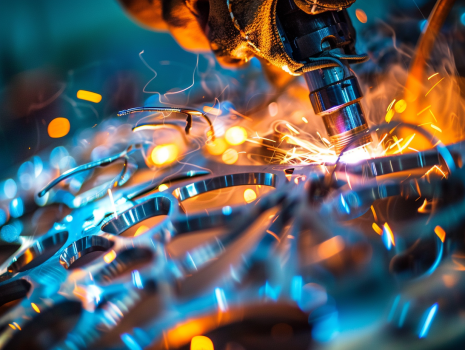
How Are Sheet Metal Assemblies Joined?
There are a few ways you can join sheet metal together. Here are some of the most common ways you can do it:
- Welding:
- MIG Welding: This is the fastest and strongest welding method. It’s great for thicker material and high-volume production.
- TIG Welding: This is the most precise welding method. It’s great for thin sheets of metal and detailed work, like making aerospace parts.
- Spot Welding: This is a very efficient way to join thin sheets of metal. You see it a lot in automotive bodies and appliances.
- Mechanical Fastening: This includes things like riveting, bolting, and screwing.
- Riveting: Riveting is a way to create a permanent mechanical joint. You see it a lot in aircraft and construction.
- Bolting: Bolting is a way to create a removable joint. This is great for when you need to take things apart to fix them or adjust them in machinery.
- Screwing: Screwing is a way to create a quick and adjustable connection. You see it a lot in electronic enclosures and consumer products.
- Adhesive Bonding: Adhesive bonding is when you use industrial adhesives to create a strong, clean joint.
- Types of Adhesives: You can use epoxy, acrylic, or cyanoacrylate adhesives depending on what you’re doing.
- Applications: This is great for joining automotive panels, electronic enclosures, and anything that you can’t weld or fasten together.
- Clinch Joining: This is when you mechanically interlock sheet metal together without any additional fasteners.
- Types: Clinching and Tog-L-Loc.
- Applications: This is used in automotive body panels, HVAC units, and anything where you need a clean, efficient joint.
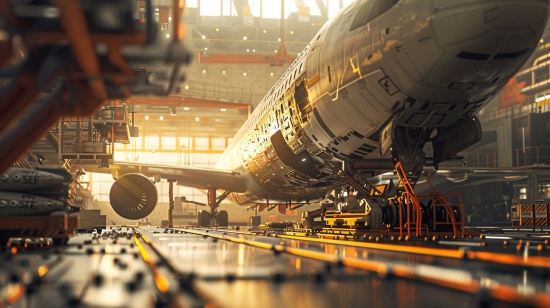
What Techniques Are Used in Sheet Metal Assembly?
There are several techniques you can use to help you put sheet metal together quickly and accurately. Here are some of the most common techniques:
• Tacking: Tacking is when you temporarily hold parts together before you finish the joint.
Methods: Spot welding and temporary fasteners.
Applications: This is used to hold parts together when you’re starting to assemble complicated things like car frames.
• Jig and Fixture Usage: Jigs and fixtures are used to make sure the parts are in the right place when you’re assembling them.
Types: Custom jigs and adjustable fixtures.
Benefits: This makes sure your parts are in the right place every time. You can make the same assembly over and over again.
Applications: This is used to make sure things are put together correctly in things like airplanes and medical devices.
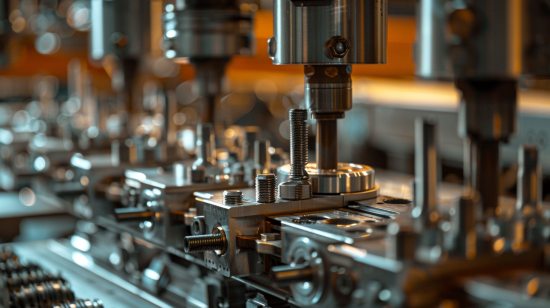
• Robotic Assembly: Robots are used to put your assemblies together with accuracy and speed.
Types: Robots are used to weld things together and to fasten them together.
Benefits: Robots put things together the same way every time. They’re fast, and they don’t take breaks.
Applications: Robots are used to mass-produce car parts, electronics, and industrial equipment.
• Manual Assembly: People put parts together when they’re building one-of-a-kind things or when they’re building something that’s complicated.
Benefits: You can make changes to your assembly quickly. You can pay attention to the details, and you can build complicated things in small quantities.
Applications: This is used to build prototypes, custom projects, and things that aren’t made in large quantities.
• Press-Fit Assembly: This is when you press parts together without using anything to hold them together.
Benefits: This gives you a strong joint without using adhesive or welding.
Applications: This is used to put things like bearings, bushings, and things that have to be put together very carefully.
• Crimping: This is when you deform one or both parts to hold them together.
Applications: This is used to put together electrical connectors, hose fittings, and anything that needs to be put together and taken apart easily.

What Are the Real Advantages of Sheet Metal Assemblies?
Sheet metal assemblies have several key benefits that make them the best choice in many industries:
- Strength and Durability: Sheet metal assemblies create strong structures that last a long time. For example, parts made out of stainless steel for airplanes can last for over 20 years in the harshest conditions and still work perfectly.
- Precision and Accuracy: Sheet metal assemblies make parts that are accurate and precise. This is essential in industries like medical devices where the parts have to be perfect. With CNC machining, you can make parts that are accurate to within ±0.005 inches. That means the parts you make will fit and work perfectly.
- Customization: Sheet metal assemblies can be customized to meet your exact needs. This can reduce the cost of your project by up to 30% by making the design better. Custom sheet metal assemblies can be made to work in a way that meets your exact needs.
- Efficiency: Sheet metal assemblies make things faster and cheaper. You can use automated assembly lines that make parts 50% faster. This means you can make parts faster and get them to your customers faster.
- Versatility: Sheet metal assemblies can be used in lots of different industries and applications. Over 80% of all consumer electronics use sheet metal assemblies because they work well and last a long time. This shows you how many different ways you can use sheet metal assemblies.

How Is Quality Controlled in Sheet Metal Assemblies?
It’s important to make sure that the sheet metal assemblies you make are good quality. Here are some of the things you can do to make sure they are the best they can be:
• Inspection Techniques: There are different ways you can check parts to make sure they’re good. You can look at them, measure them, and test them without hurting them. These are all ways to make sure the parts you make are good.
• Compliance with Standards: When you make assemblies, you have to make sure that they meet certain standards like ISO or other industry standards. This makes sure they’re safe, work right, and can be used where they need to be used.
• In-process Monitoring: You can check parts as you make them to make sure that they’re good. You can make changes as you go to make sure you don’t make bad parts. This helps you make sure that everything you make is good.
• Post-assembly Testing: After you make an assembly, you can test it to make sure it works right. This is the final check to make sure that your assembly is good and that it works right.
By doing all of these things, you can make sure that the sheet metal assemblies you make are the best they can be and that they work right every time.
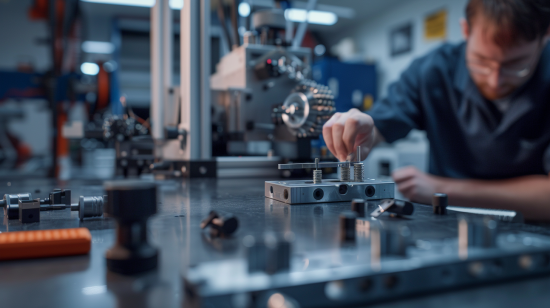
Conclusion
Sheet metal assemblies are critical for making strong, accurate, and customized parts for your projects. They help you build strong structures, make custom parts, and get things done faster. At Premium Rapid & Mold, we specialize in making sheet metal parts for your projects. We’ll help you make your projects better and get the parts you need to work the way you want them to. Contact us today to talk about your project or get a quote. We can’t wait to help you with your manufacturing needs.