In today’s fast-paced manufacturing world, creating high-quality custom metal parts quickly and efficiently is essential. Sheet metal fabrication is a versatile and reliable way to do this. Whether you’re in the automotive, aerospace, or consumer electronics industry, understanding sheet metal fabrication can give you an advantage. Let’s take a closer look at this vital process, its benefits, limitations, and how you can use it to your advantage in your projects.
Sheet metal fabrication involves cutting, bending, and assembling metal sheets to make functional parts and structures. It’s valued for its precision, efficiency, and scalability. Whether you need prototypes or mass production, sheet metal fabrication provides solutions for various industries, including automotive, aerospace, and medical equipment.
Why is sheet metal fabrication so important? It comes down to the versatility and precision it offers. By using advanced techniques and materials, manufacturers can quickly and affordably produce complex, durable parts. Let’s explore how sheet metal fabrication works and why it might be the right choice for your next project.
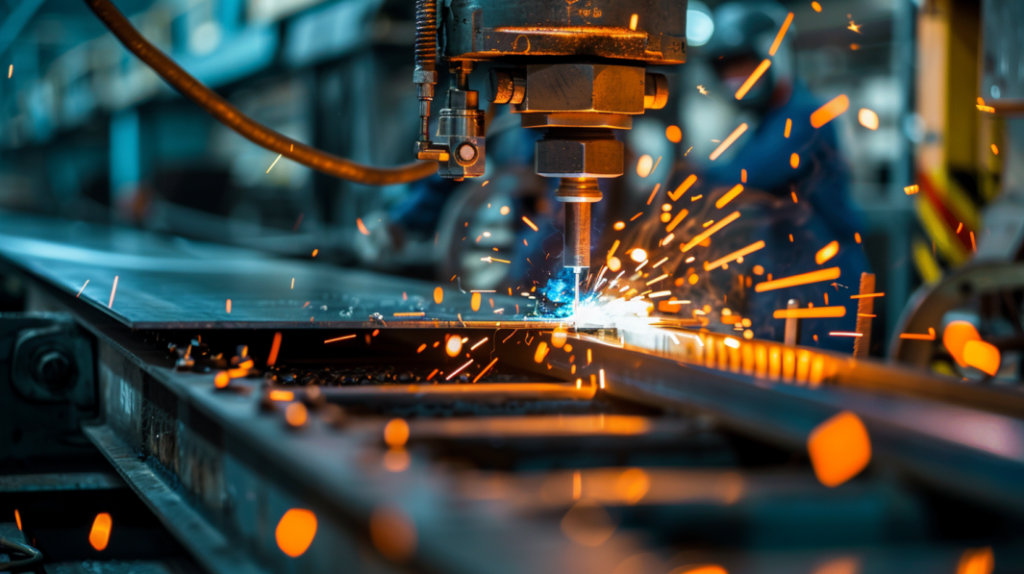
How Does Sheet Metal Fabrication Work?
Sheet metal fabrication begins with a flat sheet of metal and a design blueprint, typically in the form of a DXF or CAD file. This blueprint guides the entire process, providing instructions on how to cut, form, and finish the material to meet specific requirements.
- The Blueprint Stage:The process starts with creating a detailed design using software such as CAD (Computer-Aided Design). This design includes all the necessary specifications and dimensions for the part to be fabricated. Once the design is finalized, it’s converted into a format that fabrication machines can read, such as a DXF file. This file serves as a set of instructions for the machines to follow.
- Cutting the Metal:The first step in shaping the sheet metal is cutting it to the desired size and shape. There are various cutting methods available, each suited to different materials and project requirements. For example, laser cutting is great for achieving high precision and intricate designs, while waterjet cutting is preferred for materials that are sensitive to heat.
- Forming the Metal:After cutting, the next step is forming, which involves bending and shaping the metal into its final shape. Techniques like bending, rolling, and deep drawing are used to achieve the desired shape. The forming process may involve creating simple bends for brackets or more complex shapes like cylindrical tubes.
- Joining Parts Together:Often, the fabrication process requires assembling multiple parts to create the final product. Various methods can be used to join these parts, such as welding for strong, permanent joints, or riveting and fastening for components that may require disassembly in the future.
- Finishing Touches:The last step in sheet metal fabrication is finishing, which enhances the appearance and durability of the part. Common finishing techniques include powder coating for a tough, decorative finish, and anodizing to improve corrosion resistance. The choice of finishing method depends on the part’s intended use and the desired aesthetic and protective properties.
By following these steps, sheet metal fabrication transforms raw metal sheets into precise, functional parts ready for use in a variety of applications. Understanding these processes enables you to design more efficient, cost-effective parts, ensuring high-quality results for your projects.
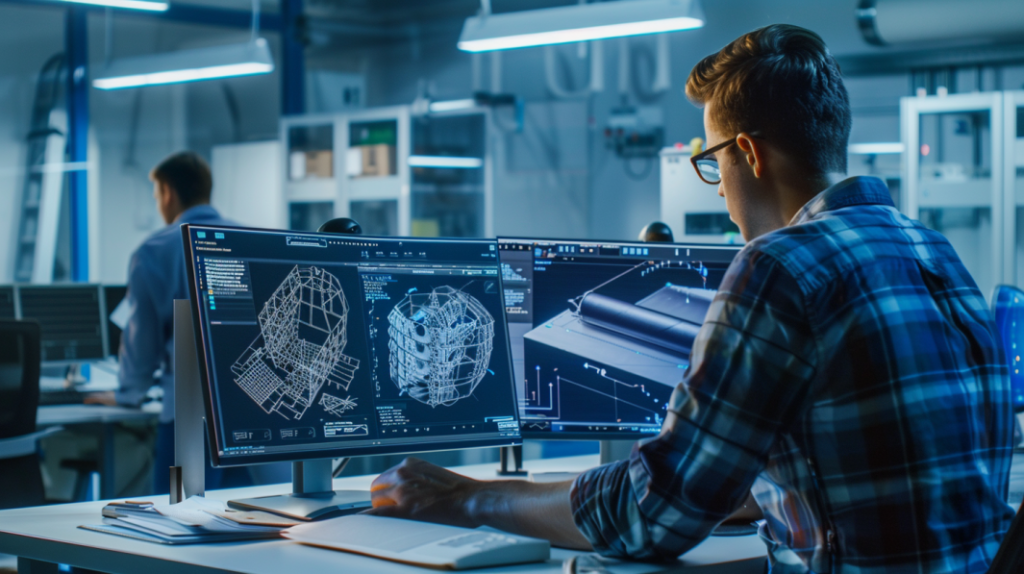
What is Precision Sheet Metal Fabrication?
Precision sheet metal fabrication takes standard processes to the next level, focusing on achieving extremely tight tolerances and high-quality finishes. This is essential for industries where precision is critical, such as aerospace and medical devices. Techniques like CNC machining and laser cutting are commonly used to ensure every part meets exact specifications. For instance, CNC machining can achieve tolerances within ±0.005 inches, ensuring components fit perfectly in complex assemblies.
Benefits and Limitations of Sheet Metal Fabrication
- Benefits
- Versatility: Suitable for a wide range of applications from automotive to household appliances. This flexibility allows manufacturers to create everything from small brackets to large enclosures.
- Cost-Effective: Efficient for both small and large batch production. The ability to scale production helps keep costs low.
- Durability: Produces strong and lightweight parts, ideal for high-stress environments.
- Scalability: Easily scaled from prototype to mass production, allowing for quick adaptation to market demands.
- Limitations
- Material Constraints: Not all metals are suitable for all types of fabrication processes. For example, certain metals may be too brittle for bending or too hard for easy cutting.
- Design Complexity: Highly complex designs can be challenging and costly to produce. Intricate shapes may require advanced machinery and longer production times, increasing costs.
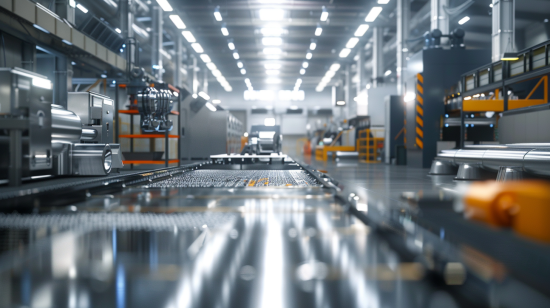
Common Sheet Metal Applications
Sheet metal fabrication is used in numerous industries. Here are some common applications:
- Automotive Parts: Body panels, engine components, brackets, and chassis.
- Aerospace Components: Fuselage parts, wing sections, and brackets that require high strength-to-weight ratios.
- Medical Equipment: Housings, brackets, surgical instruments, and components for medical devices that require precision and reliability.
- Consumer Electronics: Enclosures, brackets, and frames for devices such as computers, smartphones, and home appliances.
- Industrial Machinery: Frames, panels, and structural components that require durability and precision.
- Household Appliances: Metal parts for refrigerators, ovens, and washing machines.
- Power Distribution Equipment: Enclosures and panels for electrical systems and power distribution units.
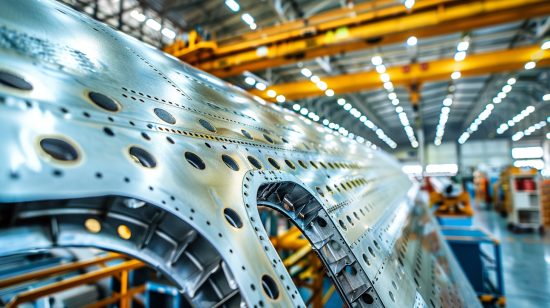
Types of Sheet Metal Fabrication
Cutting Sheet Metal
Cutting is the first step in fabrication. It can be done without shear or with shear.
Cutting Types – Without Shear
Laser Cutting: Offers high precision and minimal waste. Laser cutting is suitable for both thin and thick materials and can produce intricate designs.
Waterjet Cutting: Uses high-pressure water to cut materials. This method is ideal for cutting materials that are sensitive to high temperatures.
Plasma Cutting: Effective for thicker metals. Plasma cutting uses a high-temperature plasma arc to cut through metals quickly and efficiently.
Cutting – With Shear
Shearing: Cuts straight lines in metal sheets. Shearing is fast and efficient for cutting straight edges.
Blanking and Punching: Cuts out shapes from metal sheets using a punch and die. This method is effective for producing multiple parts quickly.
Sawing: Uses a saw blade to cut through metal. Sawing is suitable for cutting bars, tubes, and other long shapes.
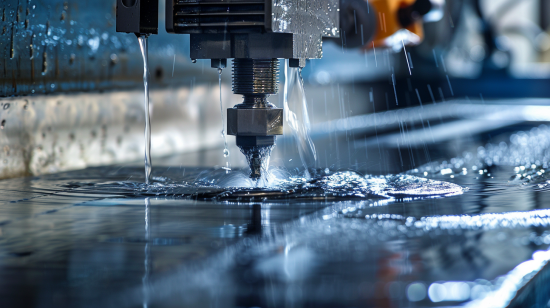
Forming Sheet Metal
Forming involves shaping metal by bending and stretching:
- Bending: Uses press brakes to create precise angles and shapes. Press brakes can handle various metals and thicknesses.
- Hemming: Folds the edge of the sheet metal back on itself to create a smooth edge. This is often used to reinforce edges and remove sharpness.
- Curling: Forms a coiled edge to add strength and eliminate sharp edges. Curling is used in applications like door hinges and protective edges.
- Rolling: Uses rollers to form cylindrical shapes. Rolling is suitable for making tubes and curved parts.
- Roll Forming: Continuous bending process for long pieces. Roll forming is ideal for producing long, continuous shapes with consistent cross-sections.
- Metal Spinning: Rotates the metal and forms it into a desired shape using a roller. Metal spinning is used for creating symmetrical parts like cones and cylinders.
- Deep Drawing: Stretches the metal into a deep, hollow shape. Deep drawing is used for making parts like cans, containers, and automotive components.
Stamping Sheet Metal
Stamping is ideal for high-volume production:
- Progressive Stamping: Multiple operations in a single press. This method is efficient and reduces production time for complex parts.
- Transfer Stamping: Moves parts between stations for different operations. Transfer stamping allows for more flexibility and can handle larger parts.
Holemaking and Threading
Creating holes and threads for assembly:
- Punching: Quickly makes holes in metal. Punching is fast and efficient, suitable for creating holes of various sizes.
- Drilling and Tapping: Adds threads for screws and bolts. This method is used when precise threaded holes are needed for assembly.
- Hardware Insertion: Inserts fasteners like nuts and bolts. This process ensures that fasteners are securely attached and aligned.
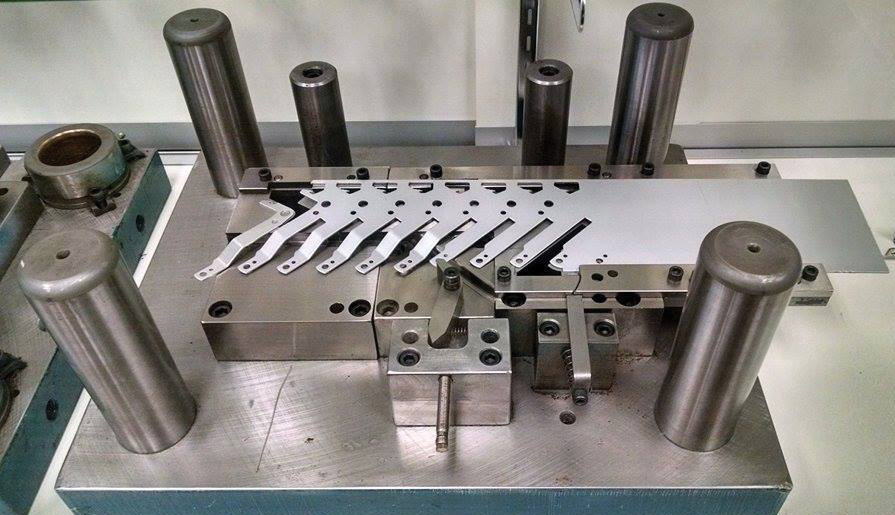
Design for Sheet Metal Fabrication
Effective design is essential for manufacturability. Key considerations include:
- Uniform Thickness: Ensures consistent strength and ease of production. Designs should maintain uniform thickness to avoid complications during fabrication.
- Bend Radius: Influences design and cost; standardize where possible. Using a consistent bend radius helps reduce tooling changes and costs.
- 4T Rule: Keep features at least four times the material thickness away from bends to avoid deformation. This rule helps maintain the integrity of the part during bending.
- Optimization Tips: Simplify designs to reduce production steps and costs. Avoid unnecessary complexities that can increase manufacturing time and expenses.
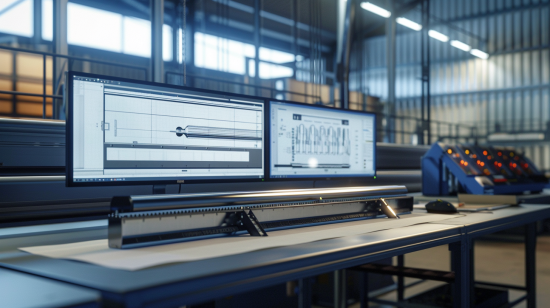
Sheet Metal Materials
Common materials used in fabrication include:
- Aluminum: Lightweight and corrosion-resistant. Aluminum is ideal for applications requiring strength and low weight, such as aerospace components.
- Stainless Steel: Strong and durable. Stainless steel is used in environments where corrosion resistance and durability are critical.
- Copper: Excellent conductivity. Copper is commonly used in electrical components due to its high electrical conductivity.
- Brass: Good for decorative parts and electrical applications. Brass offers a combination of strength and workability.
- Titanium: High strength-to-weight ratio and corrosion resistance. Used in aerospace and medical applications.
- Galvanized Steel: Coated for rust resistance. This material is used in applications where exposure to the elements is a concern.
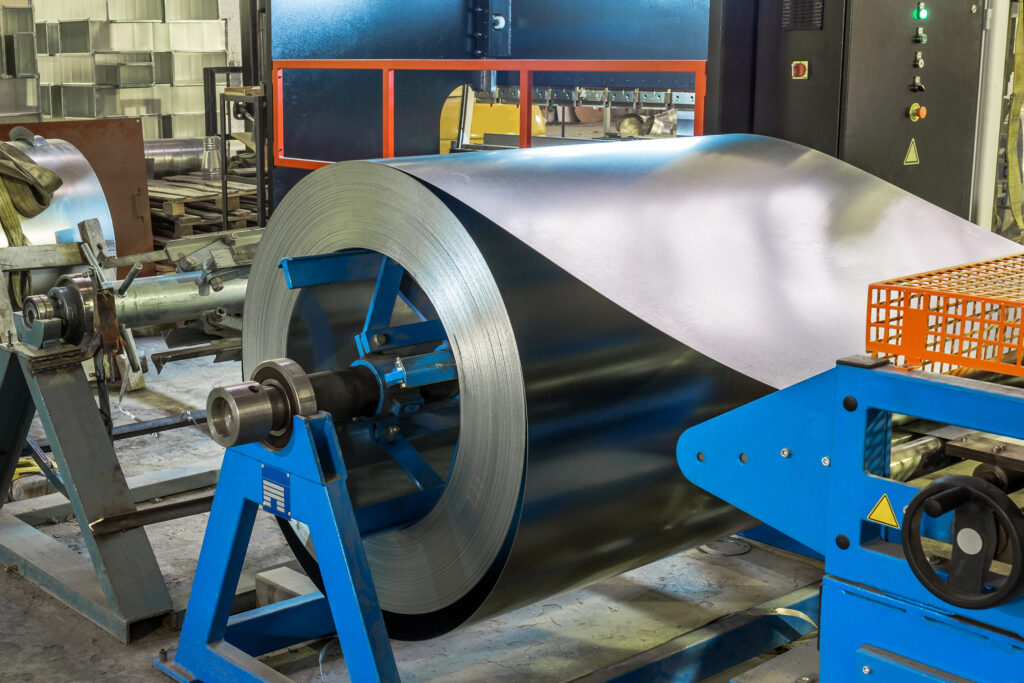
Sheet Metal Finishes
Finishing enhances appearance and durability. Options include:
- Powder Coating: Provides a tough, decorative finish. Powder coating is available in various colors and textures and offers excellent protection against corrosion and wear.
- Anodizing: Improves corrosion resistance and appearance. Anodizing is commonly used for aluminum parts and can be dyed in different colors.
- Plating: Options like zinc, chrome, and nickel for added protection. Plating adds a thin layer of metal to enhance durability and appearance.
- Bead Blasting: Provides a uniform matte finish. Bead blasting is used to clean and prepare surfaces for further finishing.
- Brushing: Creates a textured, linear finish. Brushing is often used for aesthetic purposes.
Brushing + Electropolishing: Enhances the smoothness and corrosion resistance of the surface. - Chromate Conversion Coating: Provides corrosion protection and a base for paint. Often used on aluminum and magnesium parts.
Each of these steps ensures that the final product is not only functional but also meets the highest standards of quality and durability. By understanding and optimizing these processes, you can produce efficient, cost-effective, and high-quality sheet metal parts.
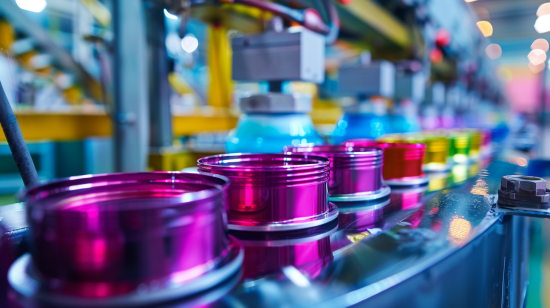
Joining Sheet Metal Parts
Joining methods vary based on the application:
- Welding: Strong but may require additional finishing. Welding is suitable for creating strong, permanent joints but may need further finishing to improve appearance.
- Riveting: Ideal for parts that need to be disassembled. Riveting provides a reliable and sturdy connection, often used in applications where parts may need to be taken apart.
- Adhesive Bonding: Good for joining different materials. Adhesives can bond metals to non-metals and provide a clean finish without the need for mechanical fasteners.
- Fasteners: Include screws, nuts, and bolts. Fasteners are versatile and allow for easy disassembly and maintenance.
- Soldering: Uses a filler metal to join parts at lower temperatures than welding. Soldering is suitable for joining smaller parts and delicate assemblies.
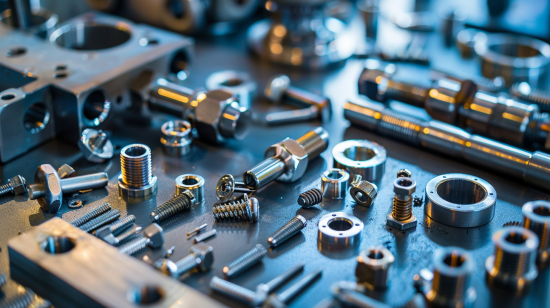
Quality Control and Testing
Ensuring high quality is essential:
- Deburring: Removes sharp edges for safety and quality. Deburring is crucial to prevent injuries and ensure smooth edges.
- Surface Finish Standards: Ensure consistency and aesthetic appeal. Standards such as orbital sanding and standard mill finishes are used to achieve the desired surface quality.
- Certifications: ISO 9001:2015, for instance, assures quality. Certifications demonstrate adherence to industry standards and ensure reliable, high-quality production.
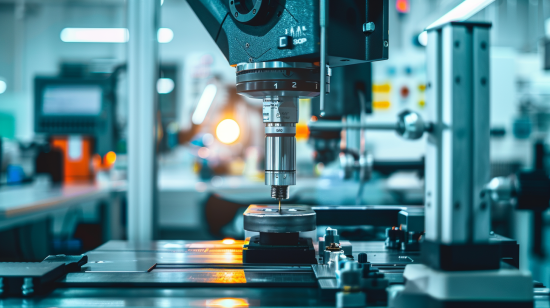
Challenges and Solutions
Common issues include inconsistent surface treatments, high defect rates, and delayed deliveries. Solutions involve:
- Design Optimization: Simplify designs for better manufacturability. Reducing complexity can help minimize errors and improve production efficiency.
- Advanced Techniques: Use precision cutting and forming to reduce defects. Investing in advanced machinery and techniques can enhance accuracy and reduce waste.
- Effective Communication: Collaborate closely with suppliers to ensure clear specifications and timely delivery. Regular communication helps prevent misunderstandings and ensures that projects stay on track.
Conclusion
Sheet metal fabrication is a versatile and efficient method for producing custom metal parts. Understanding the processes, materials, and design considerations can help you leverage its full potential. Whether you’re working on a small prototype or scaling to mass production, sheet metal fabrication offers the precision and scalability needed for success. By partnering with experienced manufacturers and adhering to best practices, you can achieve high-quality results that meet your project requirements.