In the relentless quest for superior sound quality, the design and manufacturing of audio enclosures stand as pivotal. These enclosures not only house the technological marvels that bring music to life but also significantly influence the acoustic output. With advancements in sheet metal prototyping, designers and manufacturers have an unprecedented opportunity to refine these crucial components. But how does one navigate the myriad of material choices, design optimizations, and finishing techniques to truly hit the right note?
Sheet metal prototyping offers a versatile and efficient path for developing audio enclosures that meet the highest standards of sound quality and durability. By selecting optimal materials and employing advanced finishing techniques, designers can create enclosures that not only protect and enhance audio components but also contribute to the overall aesthetic appeal of the product. Rapid prototyping and small batch customization further allow for iterative design improvements, ensuring the final product perfectly aligns with audio performance goals.
The journey from concept to concert hall requires meticulous attention to detail. As we dive deeper into the nuances of sheet metal prototyping for audio enclosures, it becomes evident that this is not just about enclosure. It's about crafting an experience. From the resonance of bass to the clarity of high notes, every aspect of sound is influenced by the enclosure's design. Material choice plays a pivotal role, with options like aluminum and stainless steel offering distinct acoustic properties. Finishing techniques add not only protection but a visual signature. And with the advent of design for manufacturing (DFM) principles, the path to innovation is clearer than ever. But how do we navigate these choices to ensure our audio equipment stands out in a crowded market?
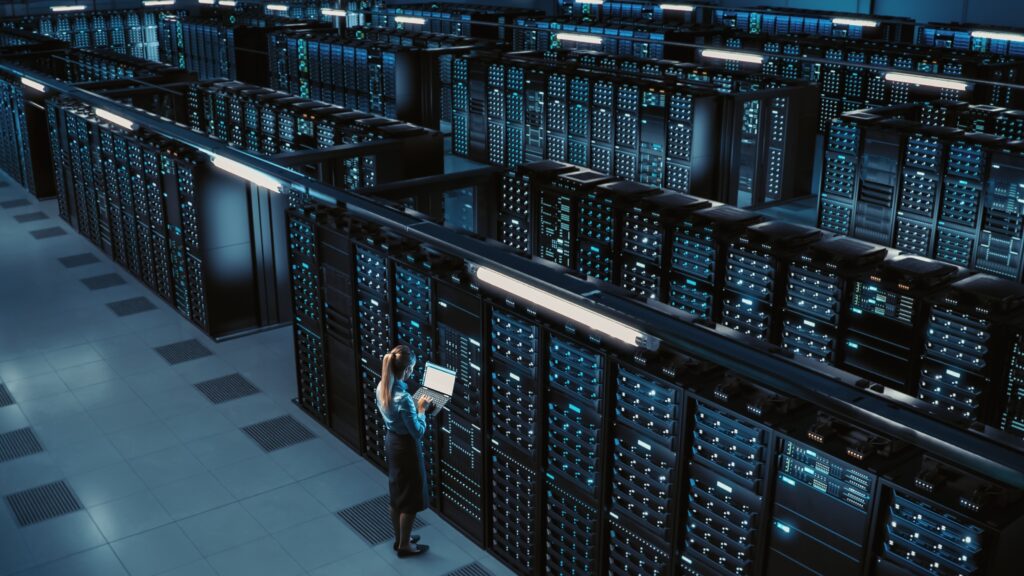
Why Is Material Selection Crucial for Audio Enclosure Performance?
Choosing the right material for your audio enclosure isn't just about aesthetics or cost; it directly impacts the sound quality. For instance, aluminum, known for its lightweight and excellent thermal conductivity, also provides a unique sound signature by reducing unwanted vibrations. Research from the Metal Construction Association indicates that aluminum's damping characteristics can enhance the acoustic performance of speakers by minimizing resonance peaks, leading to clearer sound reproduction. On the other hand, stainless steel, with its higher density, can provide a tighter, more focused sound, essential for high-fidelity audio systems.
How Do Finishing Techniques Impact the Aesthetics and Durability of Audio Enclosures?
A finish isn't just the final touch—it's a shield and a statement. Powder coating, for instance, not only offers a wide range of colors but also provides a durable surface resistant to scratches and environmental damage. The Powder Coating Institute notes that powder-coated surfaces are more resistant to chipping, fading, and wearing than other finishes, making them ideal for both indoor and outdoor audio equipment. This durability ensures that the visual appeal of the product remains intact, preserving the brand image.
What Are the Benefits of Rapid Prototyping and Small Batch Customization in Audio Enclosure Design?
Rapid prototyping transforms ideas into tangible products quickly, allowing designers to iterate and refine with precision. A study by the American Society of Mechanical Engineers showed that rapid prototyping could reduce development time by up to 63%, enabling more experimental and innovative designs to be tested and perfected. This agility in design and production not only accelerates the development cycle but also allows for custom solutions tailored to specific audio requirements, ensuring each product delivers the best possible sound experience.
How Does Design for Manufacturing (DFM) Contribute to Efficient Audio Enclosure Production?
DFM is the beacon guiding the manufacturing process, ensuring that designs are optimized for cost-effective and efficient production without compromising quality. By considering manufacturing constraints early in the design phase, DFM helps identify potential issues, saving time and resources. According to the Society of Manufacturing Engineers, incorporating DFM principles can lead to a reduction in manufacturing costs by up to 50%, highlighting its significance in producing high-quality audio enclosures at competitive prices.
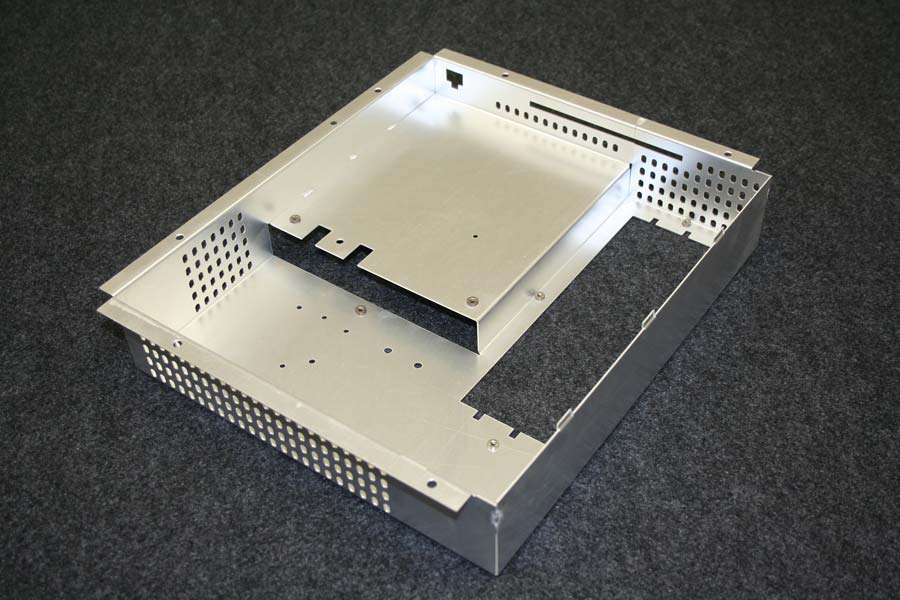
What Role Does Thermal Management Play in Audio Enclosure Design?
Effective thermal management within audio enclosures is crucial for dissipating heat away from electronic components, ensuring device longevity and stable performance. Metals like aluminum excellently conduct heat, aiding in the efficient removal of excess thermal energy. This proactive thermal management is key to maintaining sound quality and reliability, especially in high-performance audio systems.
How Important Is EMI Shielding for Audio Quality?
EMI shielding is vital for protecting sensitive electronics within audio enclosures from external electromagnetic interference, preserving the integrity of the audio output. Metal enclosures naturally offer EMI shielding, but additional coatings can enhance this property, ensuring that audio devices deliver high-quality, uninterrupted sound, even in electronically noisy environments.
How Does Precision Engineering Impact Audio Enclosure Performance?
The precision achievable through modern manufacturing techniques like laser cutting and CNC machining is essential for audio enclosures. Tight tolerances and exact engineering ensure seamless assembly and effective sound isolation, crucial for delivering the desired acoustic performance. This precision directly impacts the overall sound quality and durability of the audio device.
What Are the Benefits of User-Centric Design in Audio Enclosures?
User-centric design in audio enclosure prototyping enables tailored modifications and functional enhancements, directly addressing user needs and preferences. This approach allows for the development of audio devices that not only meet but exceed user expectations, providing a personalized audio experience through design innovations and customizable features.
Can You Provide an Example of Sheet Metal Prototyping's Impact on Audio Design?
A prime example of sheet metal prototyping's impact is seen in the development of an innovative speaker line, where precision prototyping enabled the integration of unique acoustic elements. This resulted in enhanced sound clarity and depth, illustrating how prototyping can significantly influence the final audio product's performance.
What Future Trends Are Expected in Audio Enclosure Design?
Future trends in audio enclosure design anticipate the integration of smart technologies and the exploration of new materials to achieve both functional and aesthetic advancements. Trends include enclosures with IoT capabilities for enhanced connectivity and the use of composite materials for improved acoustic properties, highlighting the evolving landscape of audio enclosure design.
Conclusion
Sheet metal prototyping undoubtedly elevates audio enclosure designs, marrying precision engineering with innovative manufacturing techniques. It addresses key aspects such as acoustic performance, environmental sustainability, thermal management, and EMI shielding, offering tailored, user-centric solutions. This approach not only enhances the audio experience but also paves the way for future advancements in audio technology, affirming its indispensable role in audio enclosure design.