Have you ever had a prototype that looked perfect, only for mass production to be riddled with issues? It's frustrating when your project hits snags, costing time and money. The pain of inconsistent quality or delays during production can be enough to make you rethink the entire process. But there is hope.
To ensure a smooth transition from sample to production, start with clear goals, involve suppliers early, prioritize tight tolerance control, and conduct thorough simulations. Use proper documentation, finish selection, and quality control to maintain consistency across batches.
Sounds easy enough, right? But if that were the case, why do so many projects still stumble during the production phase? Let’s break it down step by step.
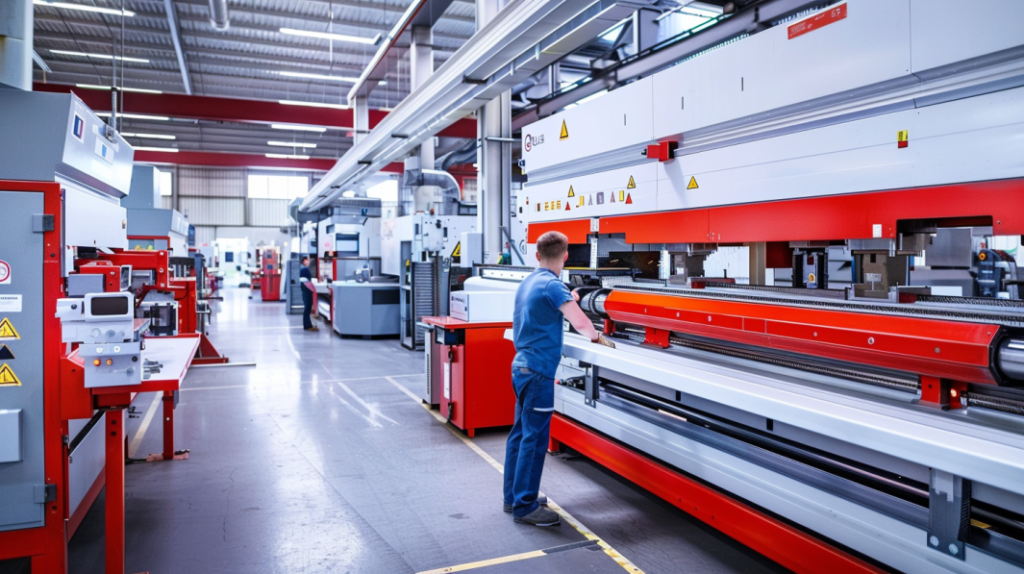
1. Define Project Goals Early
One of the biggest mistakes I see is when clients just start prototyping without having clear goals. Think about it. If you don’t know where you’re going, how can you expect to get there smoothly? You need to get clear on what you’re trying to achieve with your project. What do you want it to do? What are the performance expectations? When do you need it? What’s your budget? When you get clear on your goals up front, you’ll have a much better experience when you start getting samples because everyone is on the same page.
How do you make sure your goals align with what you’re going to do in production? You need to talk about what you need to end up with. What are you going to use the final product for? Is it going to be outside? Is it going to be in a harsh environment? By talking about these things up front, you can avoid those mid-production “Oh no!” moments.
2. Collaborative Design Stage
Have you ever heard the saying, “Two heads are better than one?” When it comes to going from sample to production, it’s absolutely true. You need to collaborate with your designers and your manufacturers during the design phase. We love it when clients bring us in early because we can help you avoid problems before they become costly.
Is your design manufacturable at scale? Many times, designs look great on paper but are hard to execute in real life. By bringing us in early, we can help you make changes that will make your design work better in the manufacturing process, so you can have efficiency and quality right from the start. Trust me, this will save you headaches later.
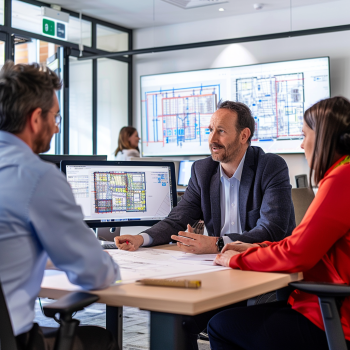
3. Material Selection & Feasibility
You wouldn’t wear a winter coat in the middle of summer, would you? The same concept applies to your project’s material selection. Picking the right material is critical for both prototypes and mass production. The material must perform consistently at scale, hold up, and be cost-effective.
For example, if your project needs high corrosion resistance, we might suggest stainless steel or pre-plated galvanized steel. But if you need to worry about weight, you might be better off with aluminum. You need to balance material performance with cost-effectiveness, and that requires understanding both design and manufacturing needs.
4. Prototype Development
Ah, prototypes! They’re like the first pancake in a batch—you expect it to be a little off, but you still want it to taste good. When we make prototypes, the goal is to make something as close to the final product as we can. That includes material selection, dimensions, and even the finishing touches like powder coating or anodizing.
However, prototypes should also be flexible. The idea is to test, refine, and tweak until we get the right recipe for production. Make sure your prototype mirrors the realities of mass production as much as you can. It’s the only way to make sure that transition goes smoothly later.
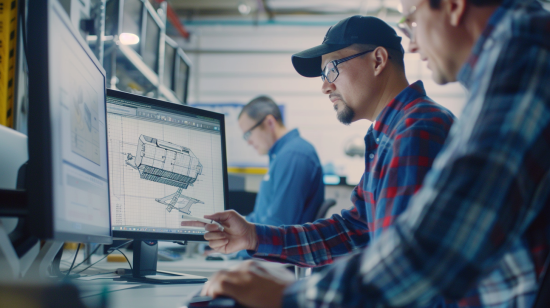
5. Tolerance Management
Let’s talk tolerances. You’d be amazed at how many people overlook this crucial part of production. Tolerances are the allowable variation in dimensions during manufacturing. If you don’t manage tolerances well, you’re setting yourself up for trouble. Parts won’t fit together, assemblies won’t work, and that beautiful prototype will feel like a distant memory.
The key is tight tolerance control during the design phase. This ensures that what worked for the prototype will also work at scale. It’s all about precision—if you get it right, you’ll have a much easier time transitioning to production.
6. Production Process Simulation
The last thing you want to do is build a prototype only to realize your process isn’t feasible for mass production. That’s where production process simulation comes in. Before we run a large batch, we simulate the manufacturing process—whether it’s laser cutting, welding, or bending.
What does this do? It helps us predict potential issues, like material distortion during bending or inconsistencies during surface treatment. By identifying these problems before production, we save time and money. Think of it as a dress rehearsal before opening night.
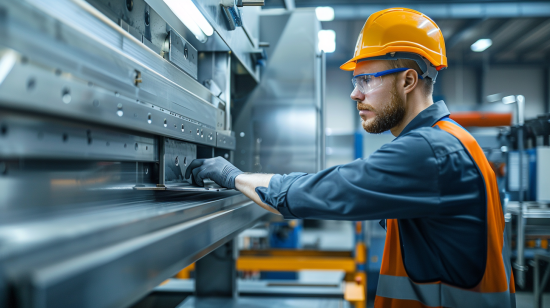
7. Supply Chain Reliability
A smooth transition isn’t just about getting the technical side right—it’s also about logistics. You need to ask yourself: Is my supplier reliable? Do they have a consistent source of materials? Supply chain disruptions will kill your project faster than anything else.
By vetting suppliers and ensuring they can deliver consistently, we reduce the risk of material shortages, delays, or quality problems. It’s one less thing for you to stress about when you scale up.
8. Prototype-to-Production Documentation
Here’s a bonus piece of advice: Document everything. And when I say everything, I mean everything—from material specifications to manufacturing processes to finishing steps. Good documentation ensures that when you move from prototype to production, there’s no confusion or deviation from the plan.
Accurate records help you maintain consistency and quality, and they also improve communication between all parties involved. When everyone follows the same playbook, there’s less room for mistakes.
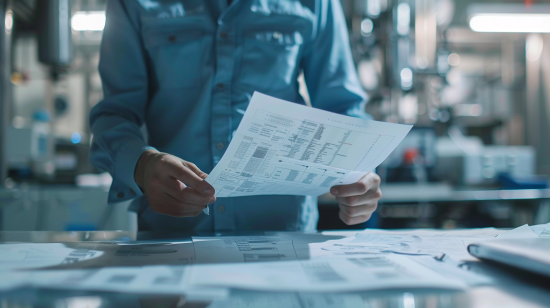
9. Check Out Finishing Options
It’s easy to get caught up in the big stuff, but don’t forget about the finishing touches. You want your final product to look as good as it works, right? Picking the right finish (like powder coating, anodizing, or plating) is critical.
But here’s the thing: not all finishes transition smoothly from prototype to production. Some finishes might look great on a small run but fall apart under mass production. Make sure whatever finish you choose can be replicated consistently across thousands of parts. If it can’t, you’re going to have a lot of problems during production.
10. Keep Quality Control Simple
Quality control is where the rubber meets the road. As you transition from prototype to production, you need to maintain the same high standards you set during prototyping. That means setting up checkpoints along the way to make sure every part meets your requirements.
Did you know one of the biggest reasons production fails is because people skip quality control? Whether it’s dimensional checks or surface inspections, don’t take shortcuts here. Make sure your QC process is strong and consistent throughout the entire production run.
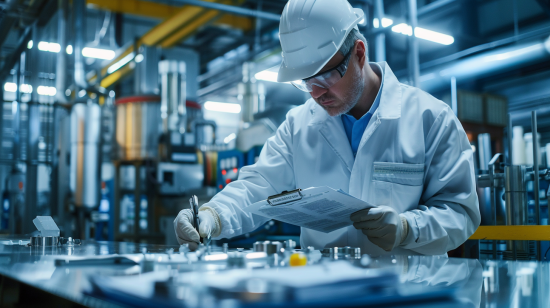
11. Testing for Environmental Resistance
If your product is going to live in a tough environment—whether it’s outdoors, in high temperatures, or under heavy use—you need to test its resistance early. This is especially true during the prototyping phase, where you can put the product through its paces.
How do we test? We simulate the environmental conditions the final product will face and make adjustments as needed. This ensures your product will perform in the real world, not just on the shop floor.
12. Packaging Considerations
Let’s talk about packaging. I’ve seen tons of projects crash and burn, not because of the product, but because of bad packaging. If you want your parts to show up at the destination in great shape, you need to consider packaging as part of the production process.
It’s not just about throwing the parts in a box—proper packaging can prevent scratches, dents, or warping during shipping. Plus, optimized packaging saves space and lowers shipping costs. Protect your investment by planning ahead.
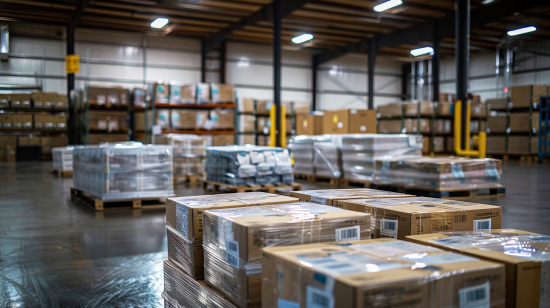
13. Flexible Production Scaling
Once you’ve nailed the prototype and gotten everything approved, it’s time to scale. But what if your supplier can’t handle bigger production runs? This is where making sure you can scale comes in.
We always suggest you confirm your supplier’s ability to scale before you commit to mass production. You want to make sure they have the resources, equipment, and people to run the larger quantities you need without sacrificing quality or lead times. This foresight will keep your project on track.
14. Timely Communication
Communication is the linchpin of all this. When problems pop up (and they will), the key is to deal with them immediately. There’s no time for a guessing game during production.
By keeping the lines of communication open, you ensure that adjustments can be made quickly, which reduces downtime and potential production delays. It’s always better to solve small problems before they become big ones.
Conclusion
To ensure a smooth transition from prototype to production, you need clarity, collaboration, and careful planning. Get your suppliers involved early, manage tolerances tightly, and make sure everything—from your documentation to your quality control—is consistent. By following these steps, you’ll have an easy transition to mass production, saving you time, money, and stress.
Remember, it’s not just about getting it done—it’s about getting it done right.