Designing sheet metal parts can be intimidating if you’re not familiar with the design constraints of the process. Whether you’re building a prototype or ramping up for low-volume production, selecting the right materials, understanding manufacturing processes, and accommodating design constraints are critical. Making mistakes early on can lead to higher costs, longer lead times, or a product that doesn’t work as intended.
That’s right, designing sheet metal parts is a big deal. You have to consider everything from the materials you use to the finishes you apply. With careful planning, you can design something that works well and doesn’t break the bank. Successful fabrication starts with good design principles, followed by thorough testing and prototyping to ensure your final product meets your expectations.
In this post, I’ll give you the lowdown on designing sheet metal parts. I’ll cover everything from material selection and manufacturing techniques to more advanced design strategies and finishing options. This post will help you design parts that not only meet your needs but also excel in quality, durability, and cost.
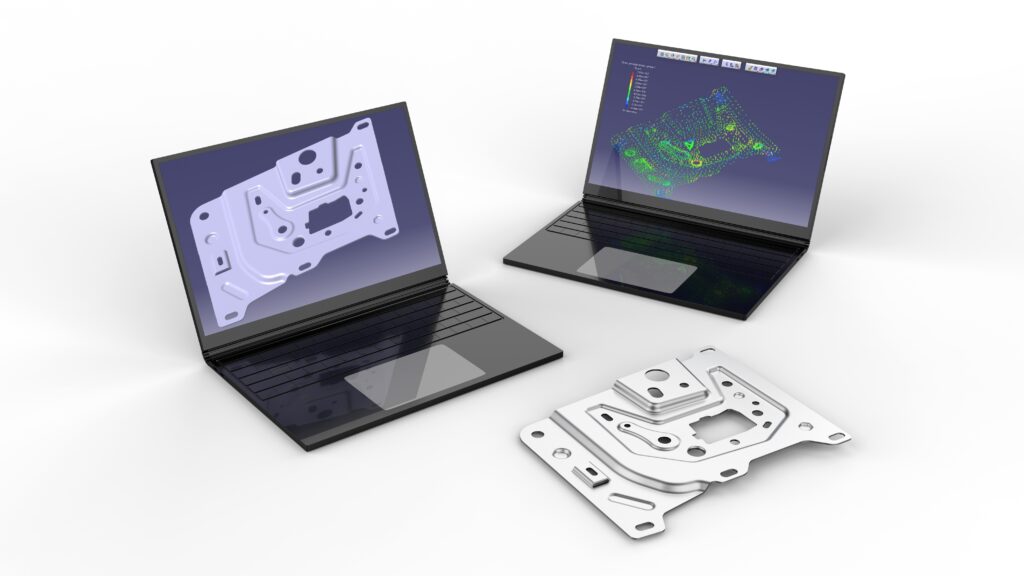
Why Choose Sheet Metal for Your Project?
Sheet metal is a great material that offers certain advantages over other manufacturing methods. It’s used in many industries, from automotive to consumer electronics, because it’s strong, lightweight, and flexible. Unlike subtractive processes like machining, sheet metal fabrication starts with flat sheets that are cut, formed, and assembled. This approach minimizes waste, reduces material costs, and allows for scalable production, making it ideal for both prototypes and high-volume manufacturing.
Furthermore, sheet metal works well with advanced technologies like CNC machining and laser cutting, which means you can create intricate, precise designs. This versatility is why sheet metal is the best choice for projects that require a balance of durability, aesthetics, and cost.
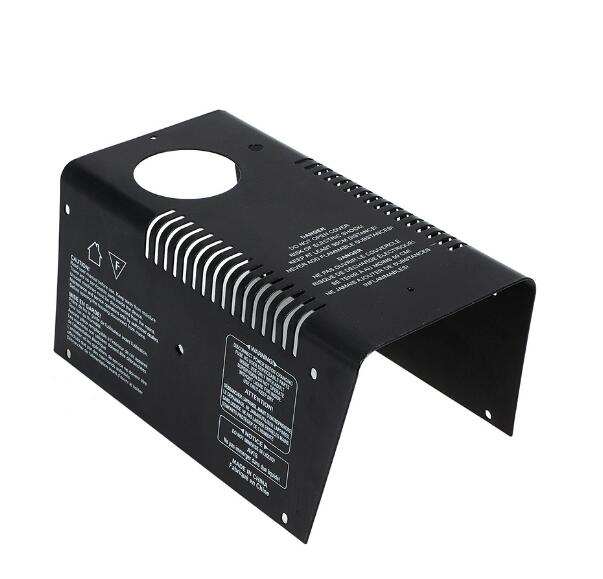
What Are the Best Materials for Sheet Metal Fabrication?
Material selection is super important. The material you choose will impact how well your part works, whether it can be made, and how much it costs to make. Here are some common materials:
• Stainless Steel: Stainless steel is strong and resists corrosion, making it great for durable parts. It comes in different flavors like 304 and 316, which are good for different environments and uses.
• Aluminum: Aluminum is light and resists corrosion, making it perfect for parts where you want to reduce weight, such as in aerospace or automotive industries. Common kinds of aluminum include 5052 and 6061.
• Cold Rolled Steel (CRS): CRS is smooth and has tight tolerances, making it great for precision parts and general-purpose applications.
• Copper/Brass: These materials conduct electricity and are often used in electrical components and things that need to look pretty.
• Pre-Plated Steel: Galvanized or galvanealed steel has extra protection against rust, making it suitable for parts that will be outside or in environments where rust prevention is critical.
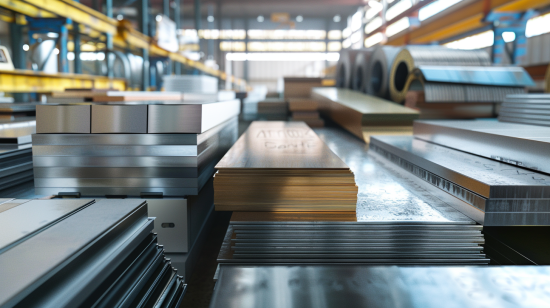
How Do Manufacturing Processes Impact Your Design?
The manufacturing process you choose will impact your design. Understanding these processes will help you design parts that work well and are made in a cost-effective way.
Cutting Methods
• Shearing: This traditional method is inexpensive for simple cuts, especially in thin materials.
• Punch Press: Great for high-volume production, a punch press is an efficient way to make simple shapes and holes. This is a good option when you don’t need the detail that laser or waterjet cutting offers.
• Laser Cutting: Laser cutting is super precise and can cut complex shapes with tight tolerances. It’s also good for a variety of materials and thicknesses.
• Waterjet Cutting: Waterjet cutting is excellent for cutting detailed designs without heat distortion, which is great for delicate or thick materials.
• Photochemical Machining: This process is used for really detailed parts. It involves controlled etching based on CAD-generated stencils.
Forming Techniques
• Bending: Bending sheet metal along a straight axis is super basic in fabrication and is used to make things like brackets, enclosures, and frames. Tools like press brakes are commonly used for bending.
• Stamping: Stamping is used for mass production and creating complex shapes, especially in the automotive industry.
• Deep Drawing and Hydroforming: These techniques are used for making hollow shapes, which are commonly seen in automotive body panels and appliance components.
• Hemming and Curling: These processes are used to reinforce or smooth out the edges of sheet metal parts to make them safer and more durable.
Joining Methods
• Welding: Welding is used to make strong, permanent joints. Depending on the application, different types of welding like MIG or TIG may be used.
• Fasteners and Riveting: These methods are good when you need flexibility in assembly or don’t want the heat-related issues that welding can cause, like warping.
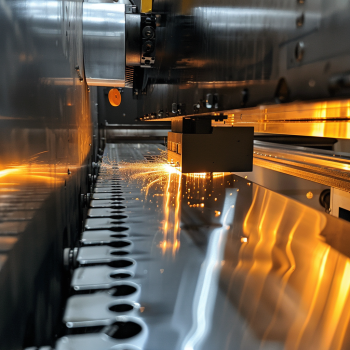
What Are the Key Design Considerations for Sheet Metal?
Designing for fabrication is different from designing for other manufacturing processes. Here are some key things to think about:
• Sheet Metal Thickness: Sheet metal parts are made from sheets, and the thickness doesn’t change. When you design a part, you have to design it for a specific thickness. You can make parts thicker by welding multiple pieces together, but that costs more and is less common.
• Design for Cost: To keep costs low, design parts that can be made with common tools instead of requiring special tools. You can also design parts to be used in lots of different things, which is called a modular design, to keep costs down.
• Bend Radii: If you design parts with the same bend radius, like 0.030 inches, it will be easier to make them. You have to set up the machines fewer times, and you’ll make better parts.
• Tolerances: The tolerances for sheet metal parts are generally looser than for machined parts. Use statistical tolerance analysis during the design phase to figure out where you might have problems and fix them. This will make sure your parts fit when you put them together.
• Proximity to Bends: If you put features too close to bends, you can distort your parts. Follow the 4T rule: Keep features at least four times the thickness of the material away from bends.
• Heat Treatments: If you need to heat treat your parts to get them to work right, figure that out early. Think about how the heat treatment will affect the ability to bend, form, or weld the material. Make sure your design works with the heat treatment so you don’t end up with warped or cracked parts.
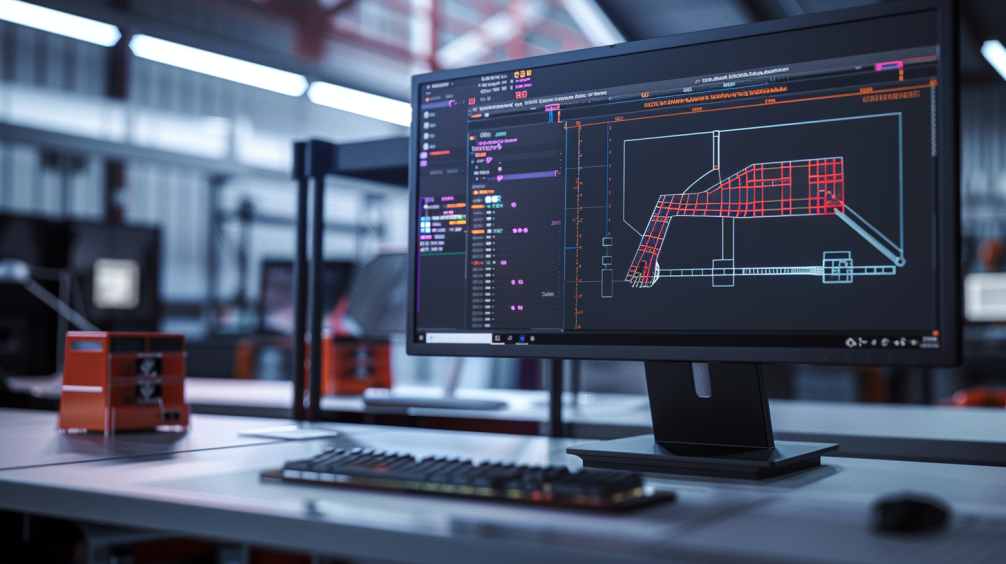
How to Incorporate Advanced Design Strategies?
Using Hybrid Manufacturing in Design
- Designing for Hybrid Fabrication: Modern manufacturing lets you combine 3D printing with traditional sheet metal fabrication. This can be especially helpful if you need parts with complex insides or custom features. By mixing 3D-printed parts with sheet metal parts, you can make your parts less complex, work better, and be easier to put together. When you design, think about how you can use these new methods to make your parts work better and make them faster.
Cost-Effective Design Strategies
- Optimizing Design for Cost-Effectiveness: To keep your costs down, design your parts to be made with common tools instead of special tools. You can also design your parts so they can be used in lots of things, which is called a modular design, to save money. When you cut your parts out, you can use a process called nesting to make sure you don’t waste material, which also saves money. If you think about all these things when you design, you can save a lot of money when you make your parts.
Designing for Tolerance Management
- Precision in Design Tolerances: Making sure your sheet metal parts fit together well when you put them together is really important. During the design phase, use statistical tolerance analysis to figure out where you might have problems before you try to make parts. Think about how the manufacturing process works, what the material is like, and what you’re going to do with the parts to set tolerances that make sense and make your parts work right.
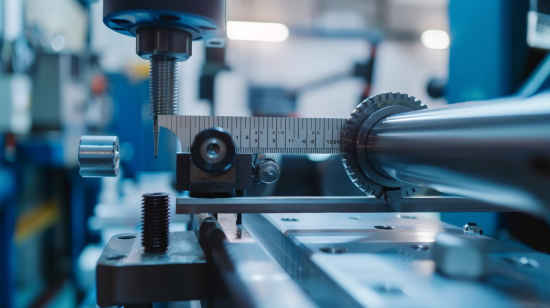
How Do You Finish Sheet Metal Parts?
Finishing is a huge part of making parts look good and work well. Here are some common finishing processes:
Surface Treatments
• Sandblasting: Sandblasting is used to roughen and clean the metal surface. This is usually done before painting, especially for stainless and carbon steels.
• Brushing: Brushing is a lot like sandblasting, but instead of using sand, you use abrasive brushes to clean and texture the metal surface. This is often the final finish on materials like aluminum and stainless steel.
• Polishing: Polishing makes the surface shiny. It’s often used on stainless steel, aluminum, and copper. You can’t paint over polished parts because the paint won’t stick.
• Powder Coating: Powder coating is a dry powder that is sprayed on the part. The part is then baked to cure the powder, creating a tough finish that is better than regular paint.
• Anodizing: Anodizing is a process that changes the surface of aluminum and other metals. This makes the part resistant to corrosion, tougher, and allows you to make the part different colors. It’s great for parts that are outside because the anodizing doesn’t peel off like paint does. Anodizing also provides insulation, so it’s good for parts that have to carry electricity like electronic parts.
• Plating: There are different ways to plate parts, depending on what you want:
o Passivation: Passivation cleans and protects stainless steel by removing free iron from the surface.
o Chromate Coating: Chromate is a conductive, anti-corrosion coating that is used on aluminum.
o Zinc Coating: Zinc protects steel from corrosion and is often used with chromate.
o Nickel Plating: Nickel gives the part a shiny finish and can be used as a base for other plating.
o Tin Plating: Tin is a conductive surface that can be soldered and is great for parts that carry electricity.
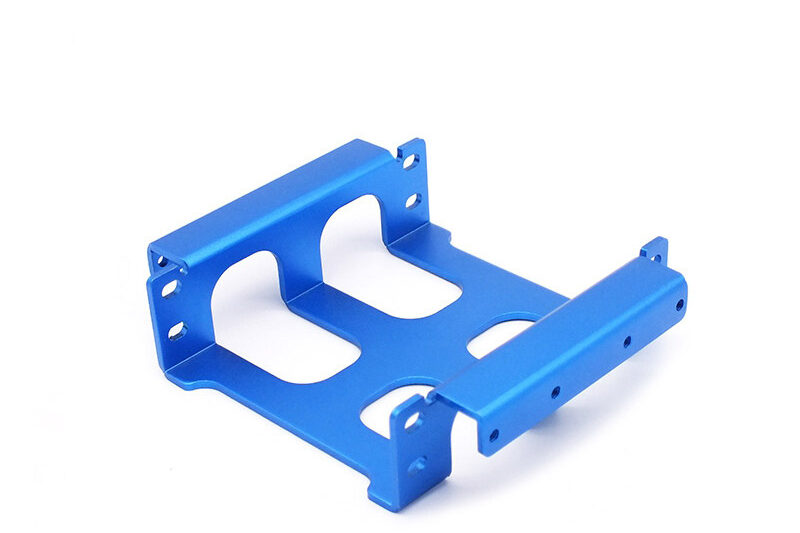
Surface Finishing in Design
• Designing for Anti-Microbial Coatings: If you are making parts for the medical or food processing industries, you might need to put special coatings on your parts to make them safe to use. When you design your parts, make sure you can put the coatings on evenly and not mess up the size or shape. This will help you make parts that work right and are safe to use.
What Are Some Common Applications of Sheet Metal?
Sheet metal’s versatility allows it to be used in a wide range of applications. Some of the most common uses include:
- Automobile Parts: Essential components like body panels, chassis, and brackets are often fabricated from sheet metal.
- Home Appliances: Sheet metal is integral to the construction of refrigerators, freezers, and other household appliances.
- Aerospace Components: The lightweight yet strong properties of materials like aluminum make sheet metal ideal for aircraft and spacecraft components.
- Electrical Enclosures: Custom chassis, cabinets, and busbars for electronics are commonly fabricated from sheet metal.
- Industrial and Consumer Products: Metal sinks, countertops, mounts, and brackets are just a few examples of where sheet metal is used in both industrial and consumer markets.
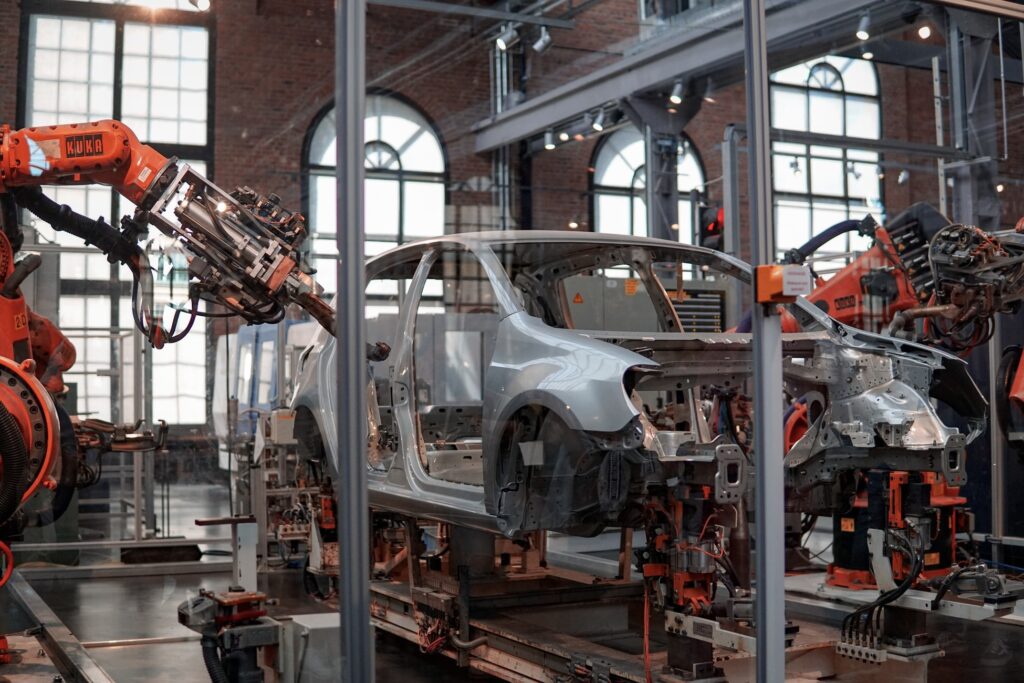
Final Thoughts on Choosing Sheet Metal Fabrication
Using sheet metal for your parts is a big deal. It starts with figuring out what your part has to do. This will help you choose the right material and thickness. Even though you can use tools like CAD and FEA to help you design your part, you still have to build a real part to make sure it works. You might have to build several parts before you get it right, but that’s OK. It’s important to test your part to make sure it meets all the requirements.
Once you have a great design, the next step is to find someone to make your part. Not everybody can make every part, so you have to get quotes from different places to find the one that can make your part the best. This way, you can make your parts quickly and cheaply, whether you’re making a few or a lot.

Conclusion
Designing parts for sheet metal fabrication means you have to know a lot about materials, how parts are made, and what you can and can’t do. By thinking about these things up front, you can avoid making expensive mistakes and make sure your project is a success. Working with people who make parts, building test parts, and finding the right finishes will help you make great parts that work the way you want them to.