Creating high-quality sheet metal parts from a mere concept can feel like staring at a puzzle with missing pieces. You want precision, durability, and efficiency, but without the right process, your ideas might hit a wall. Frustrated by design flaws or production delays? I've got you covered—let’s solve this puzzle together.
To turn your concept into high-quality sheet metal parts, you need to focus on design clarity, choosing the right materials, leveraging advanced fabrication technologies, and following through with thorough testing and quality control. A streamlined process ensures that your parts are manufacturable, cost-effective, and delivered on time.
Sound complicated? It doesn't have to be. Stick with me, and I'll guide you through every step of the process.
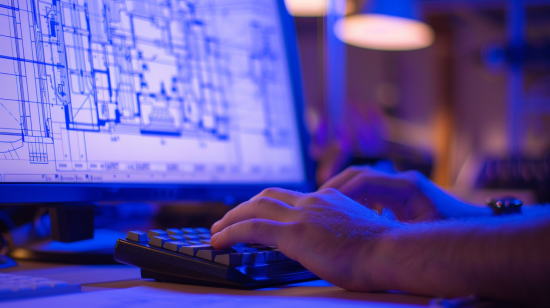
Understanding Your Design Requirements
Before anything else, let’s go back to the most important thing—figuring out what you want. Not all sheet metal parts are created equal, and different applications require different approaches. Are you designing parts for cars or medical devices? Do you need lightweight materials or are you working in a high-stress, heavy-duty environment?
What you’re designing for directly impacts how the parts are made. For example, if you’re designing parts for 5G equipment, you need to account for precision and thermal management. In contrast, automotive parts need to be corrosion-resistant and strong. You need to design parts to meet the need, or you’re going to fail.
Do you need help figuring out what you need? Let’s dive into it.
Design for Manufacturability (DFM) Considerations
We all know that not everything we design on paper can be made easily in the real world. That’s where Design for Manufacturability (DFM) comes in. If you’re like most of us, you don’t want to spend more money than you have to or waste time redesigning parts that don’t work.
This is where you need to work with engineers. You have to involve the people who are going to make your parts in the design process. They can tell you what you’re doing wrong. For example, your design might have too many tight tolerances or too many complex geometries. By fixing these things up front, you can make the parts easier to make, save money, and shorten lead times.
Do you want your parts to be easy to make or do you want to get behind schedule and have to redesign them?
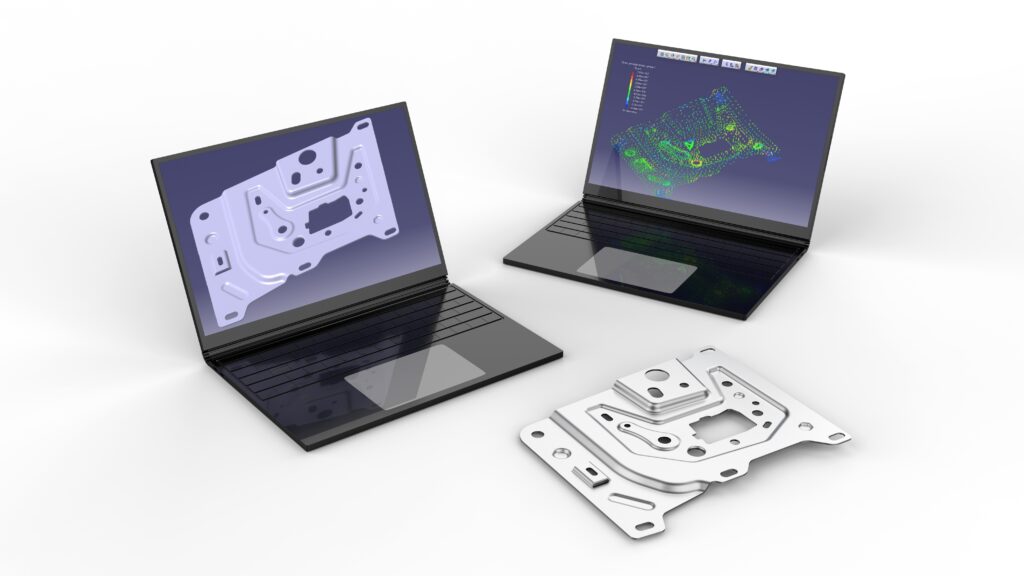
Choosing the Right Material
The material you choose is a big deal. If you’re designing parts for consumer electronics, you’re going to want to use lightweight metals, like aluminum, to make them easy to put together and to help dissipate heat. On the other hand, if you’re in aerospace, you’re going to want to use high-strength materials like titanium or stainless steel because they’re strong and resist corrosion.
But it’s not just about strength or weight. You need to think about things like corrosion resistance, machinability, and even cost when you’re selecting materials. I’ve seen too many projects go off the rails because someone picked a material that was too expensive or not right for the job. If you’re not sure, ask your supplier. We can tell you what you should use based on how it performs, what you’re doing, and how much you have to spend.
Is the material you’re using good enough for what you’re making?
Taking Advantage of Advanced Fabrication Technologies
Here’s where we get into the cool stuff: technology. I’m talking laser cutting, CNC machining, and robotic welding—all designed to give your project the precision it deserves. What’s the big deal with advanced technologies? Well, imagine trying to hand-cut a sheet of metal versus using a laser cutter. The difference in precision is night and day.
Take CNC machining for example. This tech allows us to achieve high accuracy on intricate designs—perfect for industries like medical devices, where precision is paramount. Then there's laser cutting, a method that produces clean edges, eliminates burrs, and can handle various metals from steel to copper. The right technology ensures that your parts are produced efficiently and with minimal waste.
Want precision? Trust the machines.
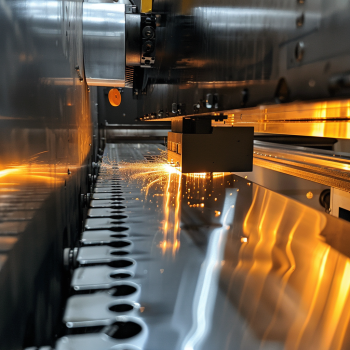
Prototyping and Production Scaling
You should never go from concept to mass production without prototyping. That’s where we test, validate, and refine. Think of it as a safety net—it ensures your design works before we make 10,000 pieces only to find out there’s a problem.
Let’s say you’re making a new industrial enclosure. By starting with a prototype, we can check things like fit, strength, and heat dissipation. Once we approve the prototype, we can scale up for mass production without worrying about potential problems.
Do you want to mitigate risks and avoid expensive mistakes? Start with a prototype.
Applying Custom Finishes
This is where we tie a bow on things—literally. Custom finishes aren’t just for looks (although who doesn’t love a shiny part?). Finishes like powder coating, anodizing, and bead blasting don’t just make parts look good—they also improve corrosion resistance, durability, and wear resistance. For example, outdoor applications such as power distribution enclosures benefit from weather-resistant coatings like powder coating.
But not all finishes are the same. Some are better for looks, while others provide more functional benefits. It’s all about picking the right finish for the part’s final environment. Trust me, nothing’s worse than spending good money on parts only to watch them corrode after six months in the field.
Do your parts need to look good or survive harsh conditions?
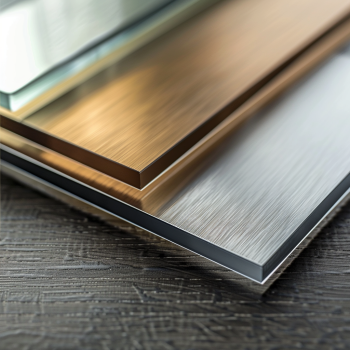
Importance of Tolerance Management
I It’s all about the details—tolerances are those little measurements that, if not managed properly, can make or break your project. If you’ve ever put something together only to find out the parts don’t quite fit, you know what I’m talking about.
When you’re designing sheet metal parts, especially parts that need to fit together in an assembly, you have to manage tolerances. It’s the difference between making a nice, functional product and one that rattles, squeaks, or—worst of all—doesn’t work at all. You need tight tolerances for high-precision applications like aerospace or medical devices, while looser tolerances might work for less critical uses.
Do you want things to go together easily? Get your tolerances right.
Quality Control During Production
You can’t wait until the end to do quality control. You have to do it upfront. I’ve seen too many projects fail because of poor quality control—parts coming out with inconsistent dimensions, finishes flaking off, or, worse yet, critical features missing.
During production, we do real-time quality control checks to make sure every part meets the standards. This includes in-line checks and material testing. Whether you’re making parts for electronics or cars, maintaining strict quality control keeps you from having to redo work and getting behind schedule.
Do you want to prevent defects before they happen?

Reducing Waste and Enhancing Sustainability
Let’s be honest—nobody likes waste. Whether it’s time, money, or materials, inefficiency costs you money and is bad for the environment. That’s why we focus on optimizing materials and recycling. For example, using recyclable metals like aluminum saves you money and helps the environment.
By reducing waste in the manufacturing process and using environmentally friendly materials, we help you meet environmental regulations and save money. It’s a double win—less waste, lower costs, and a smaller carbon footprint.
Do you want to reduce your impact on the environment?
Post-Processing Customization for Specific Applications
Customization is huge in sheet metal fabrication. Depending on what you’re making, we offer a variety of post-processing options to fine-tune your parts. For example, anodizing improves the corrosion resistance of aluminum, making it perfect for marine applications. On the other hand, chromate conversion offers great conductivity for electronic enclosures.
Each finish has a specific purpose. Whether you need a decorative touch or additional protection, picking the right post-processing treatment ensures your parts meet the requirements of the final application.
What kind of customization does your project need?
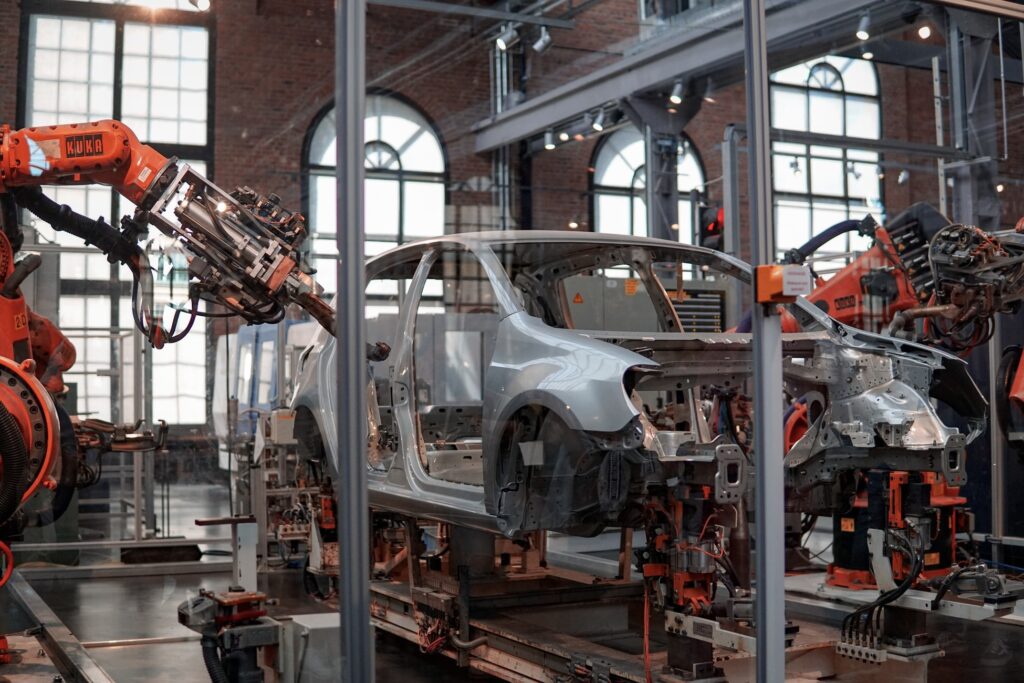
Conclusion
Taking a concept to a finished sheet metal part is a process—one that requires planning, using the right technology, and working closely with your supplier. By focusing on design, material selection, and quality control, we make sure that your project goes from idea to reality smoothly and efficiently. If you approach it the right way, you will be successful.
Are you ready to make your concept a reality? Let’s do it.